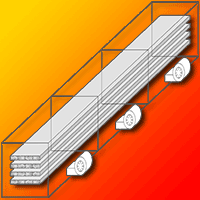
Pilot-scale drying of southern pine (Pinus spp.) lumber in a heated tube dryer
iForest - Biogeosciences and Forestry, Volume 18, Issue 1, Pages 10-15 (2025)
doi: https://doi.org/10.3832/ifor4583-017
Published: Feb 02, 2025 - Copyright © 2025 SISEF
Research Articles
Abstract
Drying is essential for preserving the strength and durability of wood and wood products. This study aimed to evaluate the performance of a pilot-scale tube-type lumber dryer. Solid sawn rough green southern yellow pine (Pinus spp.) specimens, approximately 2 inches thick by 6 inches wide, and 12 feet long (≈ 5 cm × 15 cm × 3.66 m), were inserted into heated tubes for drying. The pilot scale dryer had four sealed (but open at each end) steel heated tubes, and each tube was sized to hold four specimens. Each tube was 36 ft (≈11 m) long. The temperature of the tube was controlled by rapidly circulating hot air about the tubes’ exterior. Each tube had 3 temperature zones, and each temperature zone was controlled individually. Each lumber specimen was inserted into zone 1 and dried for a specified amount of time, and then advanced to zone 2 and zone 3. The delta moisture content of dried specimen was calculated based on the initial and final weight and final moisture content. The results showed that the delta moisture content was greatest at 425-425-400 °F (≈218-218-204 °C) and lowest at 400-400-350 °F (≈204-204-177 °C). Greater weight-loss rates were observed in the dried lumbers within the temperature range of 375-375-375°F (≈191-191-191 °C). In summary, this device rapidly dried the lumber, and moisture content standard deviations were relatively high.
Keywords
Delta Moisture Content, Varying Temperature Zones, Southern Yellow Pine, Heated Tube Dryer, Wood Drying
Introduction
As a biological and natural material, wood changes in response to its surrounding environment. It can be affected by weather factors such as air humidity, precipitation, biological issues, radiation (UV, IR), etc. Drying is an indispensable aspect within the realm of wood processing, leading to significant enhancements in the material’s physical characteristics, mechanical properties, dimensional stability, and its suitability for coatings ([6], [5], [7], [13]). Lumber with a moisture content (MC) below 20% is highly resistant to fungal issues like stain, decay, and mold. Dry lumber is stiffer than wet, thereby enhancing its structural performance. Fasteners perform better in dry as compared to wet lumber. Products from properly dried lumber experience minimal shrinkage and develop better gluing, machining, and finishing performance. Additionally, lumber intended for treatment with fire retardants or preservatives should be partially dried to facilitate chemical penetration ([2]).
Energy is essential to evaporate moisture during wood drying. Free water evaporates readily, while removing bound water requires increasing energy as MC decreases ([10]). Proper temperature control in drying is crucial. Higher temperatures hasten drying but prolonged exposure to wood, and cause defects like checking, cracking, and warping, while also impacting its color and deterring pests ([9]). Proper humidity control is essential for quality drying, with lower relative humidity accelerating the process but potentially causing issues like cracking, splits, and honeycomb in some cases ([11], [3]). Balancing time, temperature, and relative humidity to achieve the desired MC and quality can be challenging.
Various wood drying methods exist, including shed air drying, forced air shed drying, warehouse pre-drying, low-temperature kiln drying, platen vacuum drying, dehumidification drying, and conventional steam-heated kiln drying ([2]). Platen drying of lumber is a means by which wood is rapidly dried via conductive heat. There, smooth heated platens directly contact the wood surfaces and thus transfer energy to the wood directly. The selection of each method hinges on factors like cost, equipment availability, wood properties, and environmental factors.
Southern yellow pine (Pinus spp.) lumber and plywood are commonly used in construction due to its notable strength among softwood species ([14]). It is distinguished by its significant resin canals and distinct abrupt growth rings, which feature wide and prominent latewood bands. These wide latewood bands can slow the drying process and induce internal stresses due to varying shrinkage behaviors. The abrupt transition from earlywood to latewood can create stress concentrations within the wood, making it more susceptible to internal stresses and defects such as checking and splitting. The latewood percentage varies from approximately 25% to 60%. In younger and more rapidly grown plantation trees, the latewood percentage is generally lower in this range. The latewood percentage is often at the higher end of this range in older, more mature, slower-grown trees. Based on the author’s experience, the initial moisture content of freshly sawn southern pine lumber is approximately 110%, on a dry basis. The specific gravity of pine varies from approximately 0.50 to 0.60.
With respect to structural lumber, the southern pine group consists of four Pinus species varieties: P. echinata (shortleaf), P. elliottii (slash), P. palustris (longleaf), and P. taeda (loblolly). Once manufactured, the lumber from these species is indistinguishable. Of these, the vast majority of lumber comes from Pinus taeda. Based on the forest resource from which this lumber was manufactured, it is assumed that all material used in this study was Pinus taeda.
Controlling the drying process is critical to minimize these issues ([1]). Southern pine is, however, highly permeable, allowing water to pass rapidly through its wood cells. This characteristic helps prevent the formation of damaging moisture gradients during the drying process, which is a common concern in other wood species ([12]). Experience shows that southern pine wood can be dried rapidly and successfully at relatively high temperatures ([4]). As temperature increases, the mass of water vapor, as indicated by saturated vapor pressure that air can hold, increases dramatically. For this reason, if lumber can be dried at increasingly high temperatures, less total air volume is required to remove the water. Moreover, the moisture content of freshly cut lumber can range from over 200% in the sapwood to as low as 30-35% in the heartwood, posing a challenge for the ensuing wood drying process. In pine species, sapwood has a moisture content between 128% and 160%, whereas hardwood has a moisture content ranging from 30% to 50% ([8]).
Currently, no data is available for pilot-scale heated tube drying of southern yellow pine. Initial experiments suggest that heated tubes can effectively dry southern pine poles, lumber, and veneer. Moreover, smaller pieces of southern pine and possibly other wood species can likely be dried using this method. Demonstrating the advantages of employing heated tubes for wood product drying on a pilot scale can lead to technology adoption. It is crucial to emphasize that optimizing the drying process for various batches of sawn lumber is essential. This stems from differences in initial moisture content, wood densities, anatomical structures across wood species, and variations in lumber sizes. This study sought to design, construct, and test a gas-fired pilot-scale tube-type dryer. It also investigated the weight loss, and ΔMC, of pine lumber when exposed to different temperature zones and differing residence times.
Material and methods
Wood
Two inches by 6 inches by 12 feet (t × w × l) rough southern yellow pine (Pinus spp.) specimens were used (≈ 5 cm × 15 cm × 3.65 m). The assessed mean density of the material was 38 lb ft-3 (≈ 609 kg m-3). Lumber was procured from a regional production sawmill in Northeastern Mississippi. Its annual production was on the order of 150 million board feet per year (≈ 0.354 million cubic meters). Rough green freshly sawn lumber, from freshly felled logs was taken from the mill and brought to the laboratory at Mississippi State University for experimentation. Once the drying was completed, the rough (non-surfaced) dry lumber was returned to the mill for further processing and sale.
Heated tube drying process
The heated tube dryer (HTD) consisted of four heated solid-wall rectangular tubes is shown in Fig. 1. The inside dimensions of each tube were fixed at 2-inches high by 24-inched wide by 36-ft long (≈ 5 cm × 61 cm × 11 m). Each tube was constructed of quarter-inch (≈ 0.635 cm) thick plate steel. Each end of each tube was open. As such the only avenue for moisture vapor to exit the dryer was via the ends of the tubes. Vapor pressure provided the sole driving force for moisture removal.
Tubes were supported by a rigid frame such that they remained straight and true for the entire length. In contrast to press drying, this process had no moving platens. As each specimen shrank during drying, contact pressure between the wood and the platens decreased to nearly zero. It was recognized that this system was imperfect with respect to conductive heating, however it had the advantages of ruggedness, simplicity, and continuous process flow.
Immediately surrounding the tubes was a heated and insulated chamber. Heat was provided via natural gas burners. As such the outside of the tubes was directly heated via the combustion gases. Burners were thermostatically controlled to approximately plus or minus 35 °F (≈ 2 °C). Along the 36-ft (≈ 11 m) long dryer there were three natural gas burners and three walled-off zones. As such, some amount of zone temperature control (three zones) which is shown in Tab. 1 was possible for the individual boards in each zone of the dryer. Temperature and residence time were variables of interest.
Tab. 1 - Temperature zones in HTD with corresponding total durations.
Varying Temperature Zones (°F) (≈°C) Zone 1- Zone 2 - Zone 3 |
Total duration (hours) |
---|---|
425-425-425 (≈218-218-218) |
7:39 |
425-425-375 (≈218-218-191) |
7:20 |
425-425-350 (≈218-218-177) |
7:37 |
425-425-315 (≈218-218-177) |
7:00 |
425-425-400 (≈218-218-204) |
6:15 |
425-400-400 (≈218-204-204) |
6:41 |
425-400-350 (≈218-204-177) |
7:30 |
400-400-400 (≈204-204-204) |
7:39 |
400-400-350 (≈204-204-177) |
6:30 |
375-375-375 (≈191-191-191) |
5:10 |
375-330-330 (≈191-166-166) |
6:55 |
375-330-300 (≈191-166-149) |
7:15 |
To charge each tube, four pieces of green specimens were aligned edge to edge, effectively making a 2 × 24 inches slab (about 5 × 61 cm). The four specimens were then inserted simultaneously into the dryer tube. Because the green specimens fit tightly into the tubes considerable ram force was required. To expedite dryer charging, a forklift was used to provide the necessary ram force. The process was repeated for the remaining tubes until all four tubes contained specimens. At that point, the 36 ft (≈ 11 m) long dryer contained specimens, each 12 ft (≈ 4 m) long. These specimens were in “zone 1” of the dryer. After a target amount of residence time, another set consisting of 16 pieces of 2 × 6 inches (≈ 5 × 15 cm) specimens were inserted into the four dryer tubes. The total duration (h) is calculated by summing the residence time in zones 1, 2, and 3 (Tab. 1). This additional set of specimens pushed the first specimens that were already in the dryer into “zone 2”. The process was repeated until the dryer was full. At full capacity, the dryer contained 48 pieces of lumber, equivalent to 48 ft3 (≈ 1.4 m3). Eventually all the pieces passed through all three zones of the dryer.
Data was collected on each individual board that was processed through the dryer. In the log breakdown process at the sawmill, the moisture in the wood is transferred to the sawn lumber, establishing the initial moisture content for the subsequent wood drying process. The initial weight of each green specimen was determined using a weighing scale. The final weight of the specimen was promptly quantified upon their exit from the heated tube dryer. Final MC of dried specimen was calculated using a moisture meter. The initial moisture content (MCi, %) of the lumber was calculated based on the following equation (eqn. 1):
where wi is the initial weight (lb) and wod is the over dry weight (lb). Delta Moisture Content (ΔMC %) was calculated as follows (eqn. 2):
where MCi and MCf are the initial and the final moisture content (%), respectively. Weight-loss rate (WLRs, lb/h) was calculated as (eqn. 3):
where Wi and Wf ar the initial and the final weight (lb), respectively, and h is the duration (in hours).
Aside from moisture content, lumber quality was not noted. Thus, warp as crook, bow, or twist along with checking and other potential drying defects, were not tabulated. Once the rough lumber was dried it was returned to the cooperating sawmill for their subsequent further processing.
Statistical analysis
The experimental data underwent statistical analysis, utilizing an analysis of variance (ANOVA) along with Fischer’s F-Test, and Spearman Rank Order Correlations, employing STATISTICA™ version 14 software (StatSoft Inc., Tulsa, OK, USA).
Results and discussion
The results of the effects of average temperature (°F) and total duration (h) of drying time on ΔMC (%) and WLRs (lb/h) are shown in Tab. 2. It is evident from the P-values that the monitored factors, average temperature (°F) and total duration (h), have a significant effect on the characteristics, ΔMC (%) and WLRs (lb/h).
Tab. 2 - Analysis of variance (one-way ANOVA) of ΔMC (%) and WLRs (lb/h) for the effect of average temperature (°F), and total duration (h). (df): degree of freedom; (SS): Sum of Squares; (MS): Mean square.
Characteristics | Monitored factors | SS | df | MS | F-value | Prob. |
---|---|---|---|---|---|---|
ΔMC (%) | Temperature (°F) | 10.431 | 3 | 3477 | 9.305 | <0.05 |
Error | 199.908 | 535 | 374 | |||
Total Duration (h) | 24.340 | 10 | 2434 | 4.669 | <0.05 | |
Error | 667.265 | 1280 | 521 | |||
WLRs (lb/h) | Average Temperature (°F) | 116.61 | 3 | 38.87 | 104.97 | <0.05 |
Error | 198.12 | 535 | 0.37 | |||
Total Duration (h) | 183.2 | 10 | 18.32 | 46.03 | <0.05 | |
Error | 509.35 | 1280 | 0.40 |
Fig. 2 displays the ΔMC (%) of pine specimens dried with varying temperature zones over a period of times in the HTD. Notably, the highest ΔMC (78%) is observed in the temperature zones at 425-425-400 °F (≈ 218-218-204 °C) over a residence time of 6 h and 15 min. In contrast, at 400-400-350 °F (≈ 204-204-177 °C), ΔMC (%) is significantly lower, at 50%, at a residence time of 6 h and 30 min. Higher ΔMC (%) levels indicate greater amounts of moisture evaporated during HTD, while lower levels demonstrate less moisture evaporation. This result is interesting and suggests that the varying temperature at 425-400-400°F (≈ 218-204-204 °C) is the optimal choice for at 6 hours and 15 minutes residence time.
Fig. 2 - The effect of varying temperature zones (°F) on the ΔMC (%) of dried pin lumbers. The small squares represent mean values and bars represent ± 0.95 confidence intervals.
Another finding from the Fig. 2is that 83% of all grouped samples (10 from all 12 groups) have a ΔMC ranging from 64% to 77.9%, while the remaining grouped samples (17%) have ΔMC values between 50% and 57% (based on the significant different in Tab. 3). The target was to achieve that 90% of all samples would be at or below 15%; 66% of the total samples are at or below 15%, while the remaining 33% are above 15%.
Tab. 3 - Tukey’s Honest Significant Difference (HSD) test for the significance of differences between pairs of ΔMC (%) means. (***): p<0.05.
Varying Temperature Zones (°F) (≈°C) |
Mean ΔMC (%) | |||||||||||
---|---|---|---|---|---|---|---|---|---|---|---|---|
72.7 | 76.4 | 71.2 | 69.6 | 77.9 | 77.3 | 64.1 | 65.1 | 50.3 | 64.6 | 57.1 | 64.7 | |
425-425-425 (≈218-218-218) |
- | 1.00 | 1.00 | 1.00 | 0.99 | 1.00 | 0.75 | 0.88 | *** | 0.81 | *** | 0.83 |
425-425-375 (≈218-218-191) |
1.00 | - | 0.48 | 0.94 | 1.00 | 1.00 | 0.21 | 0.33 | *** | *** | *** | *** |
425-425-350 (≈218-218-177) |
1.00 | 0.48 | - | 1.00 | 0.62 | 0.23 | 0.91 | 0.97 | *** | 0.52 | *** | 0.64 |
425-425-315 (≈218-218-177) |
1.00 | 0.94 | 1.00 | - | 0.79 | 0.86 | 0.99 | 1.00 | *** | 0.99 | 0.18 | 0.99 |
425-425-400 (≈218-218-204) |
0.99 | 1.00 | 0.62 | 0.79 | - | 1.00 | 0.09 | 0.16 | *** | *** | *** | *** |
425-400-400 (≈218-204-204) |
1.00 | 1.00 | 0.23 | 0.86 | 1.00 | - | 0.13 | 0.22 | *** | *** | *** | *** |
425-400-350 (≈218-204-177) |
0.75 | 0.21 | 0.91 | 0.99 | 0.09 | 0.13 | - | 1.00 | 0.09 | 1.00 | 0.92 | 1.00 |
400-400-400 (≈204-204-204) |
0.88 | 0.33 | 0.97 | 1.00 | 0.16 | 0.22 | 1.00 | - | *** | 1.00 | 0.81 | 1.00 |
400-400-350 (≈204-204-177) |
*** | *** | *** | *** | *** | *** | 0.09 | *** | - | 0.06 | 0.94 | 0.06 |
375-375-375 (≈191-191-191) |
0.81 | *** | 0.52 | 0.99 | *** | *** | 1.00 | 1.00 | 0.06 | - | 0.33 | 1.00 |
375-330-330 (≈191-166-166) |
*** | *** | *** | 0.18 | *** | *** | 0.92 | 0.81 | 0.94 | 0.33 | - | 0.40 |
375-330-300 (≈191-166-149) |
0.83 | *** | 0.64 | 0.99 | *** | *** | 1.00 | 1.00 | 0.06 | 1.00 | 0.40 | - |
All the pieces are dried together in a typical lumber dry kiln and in a shared community atmosphere. There, temperature, humidity and airflow are regulated. As such the wetter pieces tend to dry more and the dryer pieces tend to dry less as they attempt to equilibrate with the atmosphere. In the tube dryer, there was little atmospheric mixing adjacent to any specimen. Each tube contained a maximum of twelve isolated pieces. In each tube there was no direct control of humidity or air circulation. Additionally, initial lumber thickness, surface roughness, and shrinkage characteristics (which impact wood-to-platen contact) were considered sources of variation in the tube drying process.
The results of WLRs of pine specimens dried at varying temperature zones in HTD is demonstrated in Fig. 3. The highest weight loss-rate (WRLs = 4.5 lb/h, ≈ 2 kg/h), was observed at varying temperature zones of 375-375-375 °F (≈ 191-191-191 °C), based on Tab. 4. at this zone, the ΔMC was 64.6% over a duration of 5:10 hours (Fig. 2). The higher WLRs are considered the best option for HTD.
Fig. 3 - The effect of varying temperature zones (°F) on the WLRs (lb/h) of dried pine specimens. The small squares represent mean values, and the bars represent ± 0.95 confidence intervals.
Tab. 4 - Tukey’s Honest Significant Difference (HSD) test for the significance of differences between pairs of means WLRs (lb /h). (***): p<0.05.
Varying Temperature Zones (°F) (≈°C) |
Mean WLRs (lb/h) | |||||||||||
---|---|---|---|---|---|---|---|---|---|---|---|---|
3.4 | 3.5 | 3.3 | 3.6 | 4.2 | 3.9 | 3.3 | 3.2 | 3.3 | 4.5 | 3.7 | 3.4 | |
425-425-425 (≈218-218-218) |
- | 1.00 | 1.00 | 0.69 | *** | *** | 1.00 | 0.98 | 1.00 | *** | 0.14 | 1.00 |
425-425-375 (≈218-218-191) |
1.00 | - | 0.15 | 1.00 | *** | 0.00 | 0.89 | 0.51 | 0.91 | *** | 0.04 | 0.96 |
425-425-350 (≈218-218-177) |
1.00 | 0.15 | - | 0.37 | *** | 0.00 | 1.00 | 1.00 | 1.00 | *** | *** | 1.00 |
425-425-315 (≈218-218-177) |
0.69 | 1.00 | 0.37 | - | *** | 0.38 | 0.24 | 0.05 | 0.26 | *** | 1.00 | 0.67 |
425-425-400 (≈218-218-204) |
*** | *** | *** | *** | - | 0.48 | *** | *** | *** | *** | *** | *** |
425-400-400 (≈218-204-204) |
*** | *** | *** | 0.38 | 0.48 | - | 0.00 | 0.00 | 0.00 | *** | 0.26 | *** |
425-400-350 (≈218-204-177) |
1.00 | 0.89 | 1.00 | 0.24 | *** | *** | - | 1.00 | 1.00 | *** | 0.02 | 1.00 |
400-400-400 (≈204-204-204) |
0.98 | 0.51 | 1.00 | 0.05 | *** | *** | 1.00 | - | 1.00 | *** | *** | 0.99 |
400-400-350 (≈204-204-177) |
1.00 | 0.91 | 1.00 | 0.26 | *** | *** | 1.00 | 1.00 | - | *** | 0.02 | 1.00 |
375-375-375 (≈191-191-191) |
*** | *** | *** | *** | *** | *** | *** | *** | *** | - | *** | *** |
375-330-330 (≈191-166-166) |
0.14 | 0.04 | 0.00 | 1.00 | *** | 0.26 | 0.02 | *** | 0.02 | *** | - | *** |
375-330-300 (≈191-166-149) |
1.00 | 0.96 | 1.00 | 0.67 | *** | *** | 1.00 | 0.99 | 1.00 | *** | *** | - |
The degrees of dependence between monitored factors (average temperature and total hours), and the analyzed characteristics (ΔMC and weight loss-rates) is shown in Tab. 5. The negative moderate degree of dependence was observed between WLRs and total duration. However, there was a weak degree of dependency between monitored factors and analyzed characteristics. This might relate to the lack of homogenous environment surrounding each specimen in the tube dryer. In many softwood mills, after cutting, some lumber goes straight to the kiln for drying. In other cases, the lumber is first left to air dry on the yard before going to the kiln. This creates different initial moisture levels when the kiln drying process begins.
Tab. 5 - Spearman order correlation between monitored factors and characteristics. Strength of the relationship between variables: (Positive) weak: 0.10 to 0.29; moderate: 0.30 to 0.49; strong: 0.50 to 1; (Negative) weak: -0.10 to -0.29; moderate: -0.30 to-0.49; strong: -0.50 to -1.
Spearman Rank Order Correlations |
ΔMC (%) |
WLRs (lb/h) |
Average temp. (°F) |
Toral duration (h) |
---|---|---|---|---|
ΔMC (%) | 1.00 | 0.64 | 0.21 | 0.07 |
WLRs (lb/h) | 0.64 | 1.00 | 0.08 | -0.49 |
Average Temperature (°F) | 0.27 | 0.08 | 1.00 | 0.12 |
Total duration (h) | 0.07 | -0.49 | 0.12 | 1.00 |
Conclusion
The efficiency of a tube dryer on a pilot scale for southern yellow pine lumber was investigated. Over half of the total specimens were dried at or below a moisture content (MC) of 15%. Optimization of HTD’s parameters, including drying temperatures and total duration, was achieved based on calculated characteristics ΔMC (%) and WLRs (lb/h). A low correlation was observed between the average temperature and ΔMC (%). Therefore, to be commercially effective, tube-dried lumber would likely have to be moisture sorted and a portion of it redried similar to the process flow of structural veneer drying, to achieve the desired moisture uniformity. Incorporating moisture sorting and redrying can improve lumber uniformity and benefit industries needing consistent quality. Future research should explore the effects of drying temperatures and duration on moisture content and investigate how integrating these processes can enhance the commercial viability of tube-dried lumber. Additionally, examining different wood species and conditions could expand the application of tube-type dryers.
Acknowledgments
The authors wish to acknowledge the support of the U.S. Department of Agriculture (USDA), Research, Education, and Economics (REE), Agriculture Research Service (ARS), Administrative and Financial Management (AFM), Financial Management and Accounting Division (FMAD) Grants and Agreements Management Branch (GAMB), under Agreement No. 58-0204-0-098. Any opinions, findings, conclusions, or recommendations expressed in this publication are those of the authors and do not necessarily reflect the view of the U.S. Department of Agriculture. This material is also based upon work supported by the National Institute of Food and Agriculture, U.S. Department of Agriculture, McIntire Stennis project under accession number 7004892 (accession number as provided by NIFA award).
References
Gscholar
Authors’ Info
Authors’ Affiliation
Laya Khademibami 0000-0002-6849-9237
Fatemeh Rezaei
Department of Sustainable Bioproducts, Mississippi State University, Starkville, MS (USA)
Corresponding author
Paper Info
Citation
Shmulsky R, Khademibami L, Rezaei F (2025). Pilot-scale drying of southern pine (Pinus spp.) lumber in a heated tube dryer. iForest 18: 10-15. - doi: 10.3832/ifor4583-017
Academic Editor
Luigi Todaro
Paper history
Received: Feb 07, 2024
Accepted: Oct 28, 2024
First online: Feb 02, 2025
Publication Date: Feb 28, 2025
Publication Time: 3.23 months
Copyright Information
© SISEF - The Italian Society of Silviculture and Forest Ecology 2025
Open Access
This article is distributed under the terms of the Creative Commons Attribution-Non Commercial 4.0 International (https://creativecommons.org/licenses/by-nc/4.0/), which permits unrestricted use, distribution, and reproduction in any medium, provided you give appropriate credit to the original author(s) and the source, provide a link to the Creative Commons license, and indicate if changes were made.
Web Metrics
Breakdown by View Type
Article Usage
Total Article Views: 3635
(from publication date up to now)
Breakdown by View Type
HTML Page Views: 1268
Abstract Page Views: 881
PDF Downloads: 1285
Citation/Reference Downloads: 0
XML Downloads: 201
Web Metrics
Days since publication: 205
Overall contacts: 3635
Avg. contacts per week: 124.12
Article Citations
Article citations are based on data periodically collected from the Clarivate Web of Science web site
(last update: Mar 2025)
(No citations were found up to date. Please come back later)
Publication Metrics
by Dimensions ©
Articles citing this article
List of the papers citing this article based on CrossRef Cited-by.
Related Contents
iForest Similar Articles
Research Articles
Characterization of VOC emission profile of different wood species during moisture cycles
vol. 10, pp. 576-584 (online: 08 May 2017)
Research Articles
Changes in moisture exclusion efficiency and crystallinity of thermally modified wood with aging
vol. 12, pp. 92-97 (online: 24 January 2019)
Review Papers
Moisture in modified wood and its relevance for fungal decay
vol. 11, pp. 418-422 (online: 05 June 2018)
Research Articles
NIR-based models for estimating selected physical and chemical wood properties from fast-growing plantations
vol. 15, pp. 372-380 (online: 05 October 2022)
Research Articles
Behavior of pubescent oak (Quercus pubescens Willd.) wood to different thermal treatments
vol. 8, pp. 748-755 (online: 16 February 2015)
Research Articles
Physical, chemical and mechanical properties of Pinus sylvestris wood at five sites in Portugal
vol. 10, pp. 669-679 (online: 11 July 2017)
Research Articles
Kinetic analysis of poplar wood properties by thermal modification in conventional oven
vol. 11, pp. 131-139 (online: 07 February 2018)
Short Communications
Changes in Populus sp. wood subjected to heat treatment: anatomy and silica content
vol. 18, pp. 223-226 (online: 09 August 2025)
Research Articles
Estimation of total extractive content of wood from planted and native forests by near infrared spectroscopy
vol. 14, pp. 18-25 (online: 09 January 2021)
Research Articles
Characterization of technological properties of matá-matá wood (Eschweilera coriacea [DC.] S.A. Mori, E. odora Poepp. [Miers] and E. truncata A.C. Sm.) by Near Infrared Spectroscopy
vol. 14, pp. 400-407 (online: 01 September 2021)
iForest Database Search
Search By Author
Search By Keyword
Google Scholar Search
Citing Articles
Search By Author
Search By Keywords
PubMed Search
Search By Author
Search By Keyword