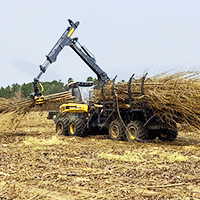
Logging residue chipping options for short rotation poplar plantations
iForest - Biogeosciences and Forestry, Volume 16, Issue 1, Pages 23-29 (2023)
doi: https://doi.org/10.3832/ifor4130-015
Published: Jan 15, 2023 - Copyright © 2023 SISEF
Research Articles
Abstract
Short rotation poplar plantations grow on flat and even terrain, and the interrow spacing is wide enough for easy machine access. If the terrain is firm enough, one may consider moving the classic roadside chipping operation directly into the field (i.e., terrain chipping), thus saving on wood extraction cost. This study compared the efficiency and cost of roadside and terrain chipping conducted with exactly the same equipment, to assess the benefits offered by the versatile deployment of a standard chipping operation, whereby the operation can be moved inside the stand whenever terrain conditions are suitable. The study was conducted at 12 sample plots, containing about one truck load of chips each (i.e., approximately 11 bone-dry tons or BDT). Plots were arranged as alternate windrows on a 8.5 ha field. Data was collected for the whole supply chain, from field to factory. The factory was located 14 km from the field. Delivered cost was 53 € BDT-1 and 70 € BDT-1 for roadside and terrain chipping, respectively, i.e., terrain chipping was 1/3 more expensive than roadside chipping, even if the latter included the additional cost of forwarding the residues to the roadside. The chipper-truck used for the test could not cope with small scattered residue piles (32 BDT ha-1), and the cumbersome reposition maneuver became the main hurdle to efficient operation. Further improvements might be achieved by pre-bunching the residues, introducing a dedicated terrain chipper or bundling the residues and taking the bundles to the factory for centralized chipping.
Keywords
Introduction
Compared with traditional forestry, tree farming grants faster returns but requires larger investments that must be repaid within a comparatively shorter time frame ([14]). The strategies to achieve immediate profitability oscillate between two options: maximizing value recovery through a relatively long rotation and careful product grading, or minimizing cost through a shorter rotation and a simplified product grading ([18]). The latter option has often been applied in the form of whole-tree chipping, which is the simplest and fastest harvesting option. However, the value of whole-tree chips has declined over time, making whole-tree chipping a viable option only under special conditions - for instance when a market is close by or when special circumstances determine a temporary spike in chip prices ([12]). In all other cases, profitability is only achieved when some higher-value assortment is obtained from the tree farm, such as timber or pulpwood ([10]). However, the trees obtained from most tree farms are relatively small, and a considerable portion of their total mass lacks the size for conversion into timber or pulpwood logs; therefore, tree farms will always yield a significant amount of residue that can be turned into a commercial product only through chipping ([29]). Given their relatively large quantity, those chips can make an important contribution to overall profitability and there is a strong interest in finding the most effective way for their production.
When it comes to building a chip supply chain, the key defining element is the so-called “point of comminution” ([1]), i.e., where chipping is performed. There are three main options: (i) chipping on the cutover (i.e., terrain chipping), before extraction; (ii) chipping at the landing after extraction; (iii) chipping at the plant, after extraction and transportation ([7]). Given the fundamental importance of that choice, the selection of the best option for each specific case has been the object of many studies over the past decades ([5]). In general, those studies aimed at matching the savings obtained by avoiding separate residue extraction and/or transportation against the higher efficiency of an increasingly centralized chipping operation. Obviously, terrain chipping is an option only if the stand is located on reasonably flat and even terrain, accessible to off-road vehicles - often dedicated ones ([31]). Therefore, almost all these studies contrast a dedicated terrain chipping operation with a dedicated roadside chipping operation, namely: an off-road chipper supported by suitable off-road chip forwarding equipment, or a larger roadside chipper supported by conventional slash forwarding equipment for bringing the uncomminuted residue to the roadside landing. However, tree farms generally grow on very flat and even terrain, which can be accessed by conventional road vehicles if soil bearing capacity is good enough. That is especially the case of poplar tree farms, which are always established on ex-arable land. There, machine traffic is only constrained by fluctuations of soil moisture content. If the soil is dry enough (or if it is frozen) road vehicles can access the field. The scenario is therefore one of changing trafficability, where windows of opportunity may open to in-field traffic and the whole roadside operation could be moved to the cutover, thus saving the cost of a forwarder for moving the residues to the roadside.
However, chipping residues on the cutover is bound to decrease the efficiency of the chipper, since the material is less concentrated and frequent repositioning is required. Similarly, truck manoeuvres are more frequent and laborious. Therefore, the savings accrued from avoiding residue extraction will be eroded from an increase in the cost of chipping and transport. To our knowledge, no studies have addressed this specific issue. Operations managers have no quantitative references when making a decision about those two options.
The goal of this study was to produce a quantitative reference, where the same operation was alternatively used for roadside and terrain chipping in a short rotation poplar plantation. The study separately quantified the cost of all steps required for turning slash piles windrowed in the field after cut-to-length harvesting into chips delivered to the factory. The null hypothesis was that of no delivered cost differences between the two alternatives.
Materials and methods
The two chipping alternatives were tested in January and February 2022 in one of the short rotation poplar plantations established in western Slovakia by IKEA Industry for supplying their factory in Malacky. Around the factory, IKEA Industry has established over 2000 ha of poplar with the purpose of securing a stable supply of wood for their innovative high-value light-weight board that specifically relies on poplar wood. Therefore, poplar logs represent the target product, while biomass is a by-product that must supplement revenues and contribute to overall profitability. Since rotation length is quite short due to management considerations, biomass still represent at least one third of the plantation yield and should be harvested with the highest possible efficiency.
The test plantation was located near Lozorno (48° 20′ 14.77″ N; 17° 00′ 46.27″ E; WGS84), some 14 km from the factory. The site was characterized by sandy soil that guaranteed good water drainage and was generally favorable to in-stand machine traffic. Weather during all the test period was warm and dry, with occasional minor precipitations. The air temperature varied from -4 to +16 °C and the soil never froze.
The plantation was a 6-year-old poplar stand established at a spacing of 3.0 × 2.0 m with hybrid poplar (Populus × euramericana Dode [Guinier]). Harvesting was conducted according to the mechanized cut-to-length system, using the classic combination of a harvester and a forwarder. The harvester worked on a 5-row frontage and left the residue accumulated in small piles aligned with the row length, which formed discontinuous windrows. The plantation measured 8.56 ha and had a roughly rectangular shape. For the purpose of the study, the plantation was divided into 12 adjacent sections, each comprising one long windrow. Each section represented a repetition in the study and was approximately 15 m wide (corresponding to a 5-row frontage and a 3 m row spacing). Section length averaged 400 m, with variations due to the irregular field shape. The twelve sections were alternately assigned to the two treatments, on the assumption that a pure randomized design could be confusing for the operators and increase the potential for attribution errors, while the alternating design would still allow an even spread of eventual gradients. The beginning and the end of each section were clearly marked with high-visibility paint to facilitate attribution. The markings reported the section number and were in two different colors, each specific to one of the two treatments. Paint marking was repeated on the material eventually piled at the landing for the roadside chipping treatment, to avoid attribution errors.
In January, the biomass on all sections marked with an uneven number was forwarded to the roadside using a Ponsse Buffalo heavy forwarder (210 kW, 19 t own weight), equipped with hydraulically extending sides for maximizing volume capacity (Fig. 1a). The distance between the centre of the field and the roadside landing averaged 1020 m. Once at the roadside landing, the biomass was unloaded into separate piles, one per section. Piles were clearly marked with spray paint, reporting the number of the respective sections: they were eventually chipped in February, using a Muss-Max Terminator 11 XL chipper truck (350 kW - Fig. 1b). Chips were blown into 36 m3 roll-on roll-off containers, which were carried in pairs by a 5-axle truck and trailer rig. The complete chipping operation consisted of the chipper and two such rigs. Once loaded, the trucks would drive to the factory, unload their cargo and return to the worksite. The very same operation was also used for terrain chipping and deployed on the even-numbered sections. In that case, the chipper and the trucks would drive along the windrow, stopping by each residue pile for chipping and loading (Fig. 1c). Only the truck would drive into the field, while the trailer was parked at the field’s edge. Once the container on the truck was full, the truck would go back to the field edge and transfer the full container onto the trailer, then pick up the empty container sitting by the trailer. After filling the second container, the truck would drive out of the field, hitch the trailer and then leave for the factory.
Fig. 1 - The forwarder (a), the chipper and the truck engaged with roadside chipping (b) and the same engaged with terrain chipping (c).
Each machine had its own operator, who was a qualified professional with significant experience of his machine and specific task. Before starting the experiment, all operators were informed about the goal and the procedures of the experiment and received due assurance that data collection would not cause any additional risks or delays. They all accepted to participate to the study and did their best to assist with it.
All the chips from each section were loaded separately and taken to the certified weighbridge available at the factory. The weighing procedure included moisture content determination, conducted according to the gravimetric method on a 500-g sample per container. Occasionally, containers would be filled only partially in order to keep the sections separate and facilitate weight and time reconciliation. In that case, the fill rate of the container was visually estimated by the researcher on site and used to multiply the truck travel and unloading time pertaining to that specific container, on the assumption that full loads would be transported under normal work conditions (as opposed to experimental conditions). The researcher fill-rate estimates were checked by matching the actual net weight of the container and the average net weight of a range of full containers.
All the work was conducted under the supervision of three researchers, who collected time and motion data for all operations: forwarding (where applied), chipping and transportation. Time data were recorded using a portable PC fitted with the application UMT Laubrass, taking care to separate productive work time from delay time ([8]). The elemental time study technique was applied, to facilitate data analysis, identify problem areas and possibly build a more versatile simulation model. A description of the time elements is reported in Tab. 1.
Tab. 1 - Description of the time elements.
Machine | Operations | |
---|---|---|
Forwarder | Travel empty: the empty forwarder moves from the landing to the loading site | Travel loaded: the loaded forwarder moves from the loading site to the landing |
Loading: arrives to the loading site and starts loading. Ends when the loading space is full or the sample plot is finished | Unloading: arrives to the landing and deposits the load in a pile. Ends when the empty forwarder leaves the landing | |
Chipper | Driving: the chipper drives to the new chipping station. It includes the eventual maneuvers before the chipper prepares for chipping at the new station | Positioning: the chipper prepares for chipping at the new station. Includes the operator changing seats (from truck to loader), lowering the outriggers etc. Each move includes two episodes: leaving the old position and installing into the new one. |
Chipping: the loader is feeding the chipper | Piling: no wood is chipped, but the loader collects the brash, organizes it into piles, or improves the organization of existing piles. | |
Trucks | Travel empty: the empty truck leaves the factory and reaches the plantation | Travel loaded: the loaded truck leaves the plantation and reaches the factory |
Loading: from when the truck empty arrives to the plantation to when it departs from it with a load | Unloading: from when the loaded truck arrives to the factory to when it departs from it, empty | |
All (Forwarder, chipper and trucks) | Delay time: all non-productive work time, categorized according to its cause into: mechanical delay (depending on the machine), personnel delay (depending on the operator) and operational delay (depending on organizational factors, such as interference) |
Machine cost was the rates actually charged by the service providers. These were: 75 € per scheduled machine hour (SMH) for the heavy forwarder; 300 € SMH-1 for the chipper truck when engaged with work and 150 € SMH-1 for the same machine in the idle state (downtime); and 60 € SMH-1 for each of the two road rigs. The rates charged by the service providers selected for the study were in line with those charged by other service providers in the region, so that the rates and costs may be considered representative of the study region ([28]).
Statistical analysis of the study data aimed at finding reliable measures of centrality for each of the two treatments and at determining if the differences found between the two treatments were significant. The dataset comprised of 6 repetitions per treatment, each repetition represented by one full section. Additional detailed analyses were conducted for the forwarder and the trucks, with the goal to determine the distribution of total time by functional subtasks. Those analyses were conducted at the cycle level rather than the section level because the former was the most suited to subtask separation and analysis. The respective datasets comprised of 17 complete forwarder trips and 16 complete truck trips.
Given the relatively small number of data and their frequent violation of some of the main statistical assumptions (i.e., normality), the data was analyzed using non-parametric techniques, which are reasonably accurate and robust against any such violations. The Mann-Whitney unpaired comparison test was used for determining the significance of any differences between the median productivity and cost values found for the two treatments. However, conventional means and standard deviations were used for the pie and bar graphs since they were easier to visualize. For all analyses, the significance level was set at α < 0.05. The analyses were implemented with the software MiniTab® v. 17 (State College, PA, USA).
Results
Overall, the field yielded 276 green tons (gt) of chips at a mean moisture content of 54% (wet basis). The corresponding dry mass was 128 bone-dry tons (BDT). Surface yield was 32 gt ha-1 and 15 BDT ha-1, respectively. The residue harvest was evenly distributed between the two treatments, with 68 BDT allocated to roadside chipping and 60 BDT to terrain chipping.
Under the terrain chipping treatment, the powerful chipper truck deployed for the experiment could not achieve its full production potential and reached half the same productivity as it did under the alternative roadside chipping treatment (Tab. 2). That would reverberate downstream to the truck fleet, which was 1/3 less productive under the terrain chipping treatment compared with the roadside chipping treatment. As a result, the total delivered cost was 70 € BDT-1 and 53 € BDT-1 for the terrain chipping and the roadside chipping treatment, respectively, i.e., 33% more expensive for the terrain chipping treatment.
Tab. 2 - Productivity and cost by task and treatment (median values from the section-level study); p-value obtained from the Mann-Whitney non-parametric unpaired comparison test; (gt): green tons; (PMH): productive machine hours, excluding delays; (SMH): scheduled machine hour, including delays; (BDT): bone-dry tons. Productivity is reported in gt and cost in BDT because those are the most commonly used units for performance assessment and cost accounting, respectively; (Util%): Utilization (100 · productive time excluding delays/scheduled time including delays).
Treatment | Units | Roadside (n = 6) |
Terrain (n=6) |
Delta (%) |
p-value |
---|---|---|---|---|---|
Forwarding | gt PMH-1 | 11.4 | 0 | - | - |
gt SMH-1 | 8.9 | 0 | - | - | |
€ BDT-1 | 19.3 | 0 | - | - | |
gt PMH-1 | 42.4 | 17.1 | -59 | 0.0163 | |
Chipping | gt SMH-1 | 24.2 | 11.6 | -52 | 0.0163 |
€ BDT-1 | 20.6 | 47.6 | 131 | 0.0039 | |
Util % | 57 | 68 | 19 | 0.4233 | |
Transportation | gt PMH-1 | 11.3 | 7.3 | -33 | 0.0039 |
gt SMH-1 | 8.7 | 5.8 | -33 | 0.0039 | |
€ BDT-1 | 13.9 | 22.1 | 59 | 0.0039 | |
Total cost | € BDT-1 | 52.6 | 70.1 | 33 | 0.0782 |
€ gt-1 | 25.5 | 33.0 | 29 | 0.0374 |
The average duration of a forwarding cycle was slightly more than 1 hour, for a distance of 1000 m. The latter was measured on Google Earth® maps and covered the forwarder route from the centre of the field to the centre of the roadside landing; therefore, individual trips were conducted under slightly shorter or longer distances. The long extraction distance was an important factor in the expansion of cycle time, that was compounded by the relatively low travel speed, which averaged 4.5 km h-1 and 4.2 km h-1 for the empty and the loaded travel, respectively. The large incidence of travel time is easily visualized in Fig. 2. Overall, travel times took longer than loading and unloading, that is 28 minutes vs. 24 minutes per cycle, over a total cycle time of 63 minutes, including delays. The study did not determine payload size for each single forwarder cycle and therefore mean payload size was obtained simply by dividing total forwarded mass (i.e., that delivered from the 6 terrain chipping sections) times total forwarder cycles (i.e., 17 full trips). The grand mean was 8.7 green tons per cycle, or 4.0 BDT cycle-1. While not exuberant, that load was enough to achieve a productivity of 8.3 green tons SMH-1 or 3.8 BDT SMH-1.
The selected chipper truck took longer to perform all its assigned subtasks under the terrain chipping than under the roadside chipping treatment (Fig. 3). Differences were statistically significant for all subtasks, except for driving. The larger incidence of positioning time was easily explained by the frequent relocation needed to reach a biomass feedstock that was spread along the windrows in relatively small piles. Feedstock scatter compounded with a machine design that was not conceived for dynamic chipping but required the machine to realign the loader and prop the outriggers before and after each move. The long time devoted to piling was another obvious consequence of feedstock scatter, which made it harder for the loader to keep up with the chipper demand for wood and was the cause of the low productivity recorded for the chipping subtask. Besides, smaller piles implied that a longer proportion of total chipping time was devoted to mopping up the scattered tops and branches at the end of each pile.
Fig. 3 - Chipping: breakdown of total cycle time by time element (sub-task). Mean of 6 sections per treatment. Lines on the bar ends represent the standard deviation.
The incidence of downtime was higher under the terrain chipping treatment compared with the roadside chipping treatment, but the difference was not statistically significant, due to the large variability typical of delay time. However, the results were suggestive of a more difficult operation, troubled by recurrent halts, which might be partly related to the additional complexity imposed on trucking (Fig. 4).
Fig. 4 - Trucking: breakdown of total cycle time by time element (sub-task). Mean of 16 trips. Lines on the bar ends represent the standard deviation.
The close connection between chipping and trucking was clearly reflected in the elemental time study of the transportation phase. A single trip from the factory and back took almost 2 hours under the roadside chipping treatment, and over 3 hours under the terrain chipping treatment; that is: 1h 57 min and 3h 14min, respectively. The reason for such difference was the much longer time spent at the loading site under the terrain chipping treatment, due to a slower chipping operation that took longer to fill up the trucks. For the rest, the study found no significant differences between the two treatments: unloading time was virtually identical, while the 14 km distance between the plantation and the factory was regularly covered at the average speed of 30 km h-1, regardless of treatment. Load size varied between 7.5 and 8.5 BDT, with no significant differences between treatments.
The combined cost of chipping and trucking under the terrain chipping treatment was almost exactly twice as large as the same cost under the roadside chipping treatment; the difference was 35 € BDT-1, which would easily absorb the additional forwarding cost of 19 € BDT-1 (Fig. 5).
Discussion
The main limitation of this study is the small number of replications, which may have been too few for highlighting some of the finer differences between treatments. In particular, the study was unable to determine whether one treatment was plagued by delays more than the other, given that the occurrence of delays is typically erratic and differences can only be captured with long-term studies ([23]).
On the other hand, this is one of the few point-of-comminution studies that was controlled, detailed and comprehensive, as it covered the whole chip supply chain from field to factory, not just the chipping task. Furthermore, the observations were few, but each of them was relatively large so that stable performance levels would be achieved for each individual observation. Non-parametric statistics were preferred to transformation, to avoid introducing a bias. Nevertheless, the experiment was powerful enough to highlight important differences and offer significant insights into the studied machines and supply chains.
Concerning the machines, noticeable was the limited payload carried by the heavy forwarder. Even when fitted with extending sides, the heavy forwarder could not pack more than 9 green tons on its deck, which was slightly more than half its rated payload (i.e., 15 tons). Loose forest residue is a bulky feedstock that does not allow full utilization of a carrier’s payload ([2]): at best, a 65% fill rate can be achieved by fitting carriers with an enlarged load space ([11], [19]), but standard vehicles can hardly reach a 50% fill rate, especially with low-density wood such as poplar ([16]). The fact that payload was much below rated capacity was further reflected by the fact that travel speed was the same for the unloaded and the loaded machine. Low travel speed was another limitation of the studied forwarder, which seemed unable to move faster than walking pace, even when empty and on easy ground, like for many conventional hydrostatic-drive forwarders ([20]). A faster machine would certainly be more productive, and new forwarders are now available that can reach a speed in excess of 20 km h-1 ([27]).
The study also pointed at the good productivity of the selected chipper-truck and at its low utilization. Pure chipping productivity ranged between 35 and 60 green tons per hour, which is a very good result for a machine of that type ([4]). On the other hand, utilization was relatively low, although in line with the figures reported in previous studied ([3]). Incidentally, the higher utilization recorded for terrain chipping compared with roadside chipping matches quite well the available benchmark figures ([23]). Here like in most of the quoted studies, the main reason for low chipper utilization was the insufficient availability of transport vehicles. Therefore, it could make sense to detach a third truck to support the operation; even if that resulted in an expansion of truck waiting time, the trade-off would likely be worthwhile because the truck rate was less than half the idle chipper rate, as it was the case in the study by Eliasson et al. ([9]).
Overall, this study shows that roadside chipping is a better option compared with terrain chipping. Roadside chipping reflects a North American operational approach that aims at creating the best conditions for the deployment and utilization of industrial equipment. Under those conditions, one can deploy larger and more productive equipment to the benefit of reduced chipping cost. For this reason, roadside chipping has become increasingly popular also in Europe, including the Nordic region that was the strongest advocate of terrain chipping ([6], [21], [30]). However, the generally better performance reported for roadside chipping partly depends on the possibility to use a bigger and more productive machine than one would otherwise deploy in-field. That is against the initial assumption of this study, which endeavored to explore versatile deployment of the same machine. If terrain and weather allow, one would chance in-field chipping to spare the cost of residue forwarding. In this study that was not worth it, but it has been in other reported instances, which indicated potential savings in the 10%-25% range ([25], [26]). What was different then? Analysis of those studies suggests that feedstock concentration was the main difference: residue had been pre-bunched as a result of cable yarding ([26]), or windrows ([25]) were built with whole trees (not lop and top) and accounted for over 80 BDT ha-1 instead of 30 BDT ha-1 like in this study. Feedstock concentration is known to have a very strong impact on forwarder productivity ([17]). Similarly, pile size affects forwarding ([32]) and comminution ([33]) productivity alike. A logical conclusion is that the residue available on the experimental site was too little and too sparse for efficient chipping, especially if the machine took as long to re-position as the chipper truck used for the study. Therefore, efficiency would be increased by introducing pre-bunching of scattered residue and/or a more mobile chipper.
Pre-bunching could be performed by the same forwarder tasked with log extraction, after the latter task has been completed. That operation would take a fraction of the time required by forwarding proper, especially if the extraction distance was as long as in the case of this study. Yet, one could use a small excavator for the purpose, which could also assist with feeding the chipper, since a separate loader is often more efficient than the integral loader fitted to most chippers ([22]).
The market also offers highly mobile industrial chippers, capable of road and off-road traffic. Those machines have been specifically designed for terrain chipping and fast independent relocation between sites, which is more problematic for traditional forwarder-base terrain chippers. Recent studies indicate that those chippers may achieve the same high productivity regardless of chipping point: terrain or roadside ([15]). Those are likely a better option for setting up a versatile chipping operation.
Given that feedstock scatter is one of the main constraints encountered with terrain chipping, a radical solution could consist in bundling the residues using a forwarder mounted machine ([13]). Such machine would offer the same all-weather benefits of any standard forwarder, since it would be able to operate even when the terrain is not firm enough for truck access. Then, when dry weather would bring a window of opportunity, trucks could be introduced to the field for picking up the bundles and move them directly to the factory for centralized chipping ([24]). In order to maximize payload, trucks would be loaded on site by an independent loader, which could be relocated some time in advance for concentrating the bundles into larger piles to speed up truck loading later on. In fact, it seems that forwarder-mounted bundlers might find their competitive niche when the residue load is low ([28]), which is exactly why terrain chipping might be at a disadvantage in short-rotation poplar plantations.
Conclusions
A chipper-truck is still a truck and it is best suited for roadside chipping, not terrain chipping. It can drive into the plantation if the terrain is firm enough, but it cannot cope with small scattered residue piles. In that case, the cumbersome reposition maneuver becomes a main hurdle to efficient operation. Under those conditions, terrain chipping requires a machine that can handle the residues and process them while moving along the windrows. Fitting a forwarder with an enlarged load space and taking all the residues to the landing is a better option than trying to reach them with a truck-based chipper. Further improvements might be achieved by pre-bunching the residues, by introducing a dedicated terrain chipper or by bundling the residues and taking the bundles to the factory for centralized chipping.
Acknowledgments
This study was funded by the Bio Based Industries Joint Undertaking under the European Union’s Horizon 2020 research and innovation program under grant agreement no. 745874 “Dendromass for Europe” (D4EU). Additional support was provided by the Pahernik foundation, University of Ljubljana, Slovenia (⇒ https://www.uni-lj.si/news/news/6498/).
References
Gscholar
Gscholar
Gscholar
Gscholar
Gscholar
Authors’ Info
Authors’ Affiliation
Natascia Magagnotti 0000-0003-3508-514X
Consiglio Nazionale delle Ricerche, Istituto per la Bioeconomia - CNR IBE, Firenze (Italy)
University of Ljubljana, Biotechnical faculty, Ljubljana (Slovenia)
Corresponding author
Paper Info
Citation
Spinelli R, Mihelič M, Kováč B, Heger P, Magagnotti N (2023). Logging residue chipping options for short rotation poplar plantations. iForest 16: 23-29. - doi: 10.3832/ifor4130-015
Academic Editor
Rodolfo Picchio
Paper history
Received: May 09, 2022
Accepted: Nov 15, 2022
First online: Jan 15, 2023
Publication Date: Feb 28, 2023
Publication Time: 2.03 months
Copyright Information
© SISEF - The Italian Society of Silviculture and Forest Ecology 2023
Open Access
This article is distributed under the terms of the Creative Commons Attribution-Non Commercial 4.0 International (https://creativecommons.org/licenses/by-nc/4.0/), which permits unrestricted use, distribution, and reproduction in any medium, provided you give appropriate credit to the original author(s) and the source, provide a link to the Creative Commons license, and indicate if changes were made.
Web Metrics
Breakdown by View Type
Article Usage
Total Article Views: 23203
(from publication date up to now)
Breakdown by View Type
HTML Page Views: 19812
Abstract Page Views: 1610
PDF Downloads: 1392
Citation/Reference Downloads: 1
XML Downloads: 388
Web Metrics
Days since publication: 948
Overall contacts: 23203
Avg. contacts per week: 171.33
Article Citations
Article citations are based on data periodically collected from the Clarivate Web of Science web site
(last update: Mar 2025)
Total number of cites (since 2023): 2
Average cites per year: 0.67
Publication Metrics
by Dimensions ©
Articles citing this article
List of the papers citing this article based on CrossRef Cited-by.
Related Contents
iForest Similar Articles
Research Articles
Comparison of alternative harvesting systems for selective thinning in a Mediterranean pine afforestation (Pinus halepensis Mill.) for bioenergy use
vol. 14, pp. 465-472 (online: 16 October 2021)
Research Articles
Changes in moisture exclusion efficiency and crystallinity of thermally modified wood with aging
vol. 12, pp. 92-97 (online: 24 January 2019)
Research Articles
Deploying an early-stage Cyber-Physical System for the implementation of Forestry 4.0 in a New Zealand timber harvesting context
vol. 17, pp. 353-359 (online: 13 November 2024)
Research Articles
Identification of wood from the Amazon by characteristics of Haralick and Neural Network: image segmentation and polishing of the surface
vol. 15, pp. 234-239 (online: 14 July 2022)
Research Articles
NIR-based models for estimating selected physical and chemical wood properties from fast-growing plantations
vol. 15, pp. 372-380 (online: 05 October 2022)
Research Articles
Examining the evolution and convergence of wood modification and environmental impact assessment in research
vol. 10, pp. 879-885 (online: 06 November 2017)
Research Articles
Evaluation of operating cost management models for selection cutting in Scandinavian continuous cover forestry
vol. 16, pp. 218-225 (online: 12 August 2023)
Research Articles
Improving dimensional stability of Populus cathayana wood by suberin monomers with heat treatment
vol. 14, pp. 313-319 (online: 01 July 2021)
Research Articles
Physical and mechanical characteristics of poor-quality wood after heat treatment
vol. 8, pp. 884-891 (online: 22 May 2015)
Research Articles
Characterization of VOC emission profile of different wood species during moisture cycles
vol. 10, pp. 576-584 (online: 08 May 2017)
iForest Database Search
Search By Author
Search By Keyword
Google Scholar Search
Citing Articles
Search By Author
Search By Keywords
PubMed Search
Search By Author
Search By Keyword