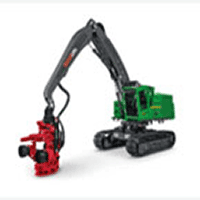
Deploying an early-stage Cyber-Physical System for the implementation of Forestry 4.0 in a New Zealand timber harvesting context
iForest - Biogeosciences and Forestry, Volume 17, Issue 6, Pages 353-359 (2024)
doi: https://doi.org/10.3832/ifor4651-017
Published: Nov 13, 2024 - Copyright © 2024 SISEF
Research Articles
Abstract
Industry 4.0 is a concept using enabling technologies to increase efficiency for industries that can digitalise production processes. Industry 4.0 is intended to be an interconnected system, shifting from centralised to decentralised production control, with optimisation completed at multiple levels in real time. It facilitates communication between humans and machines with data. Forestry 4.0 is the adaption to the forest industry where high mechanisation rates in forest harvesting operations provide a clear opportunity for digitalisation and optimisation. A Cyber-Physical System (CPS) is an enabling technology that connects the physical and virtual domains. Implementing a CPS across a mechanised harvesting operation presents opportunities such as real-time optimisation of machine tasking or predicting machine maintenance needs. While economic benefits are commonly cited as the main driver for Forestry 4.0, the literature indicates that barriers like technology, costs, education, and organisational structure have hindered progress to date. This paper develops a CPS for harvesting systems. Using a New Zealand-based case study, it demonstrates early-stage implementation where Controller Area Network data was live-streamed from a felling machine, analysed and presented on an interactive online dashboard. This system allows logging contractors to monitor the operations of their machines in real time outside the area of work, while also storing data for future analyses. However, without linking the entirety of the harvesting operations, the economic benefits and realisation of Forestry 4.0 are limited.
Keywords
Forestry 4.0, Cyber-Physical Systems, CANbus, New Zealand, Forest Harvesting, Industry 4.0, J1939
Introduction
Industry 4.0 has transformed how many businesses manage manufacturing, operational monitoring, material utilisation, and logistics processes ([17], [35]). Emerging from a high-tech strategy introduced by the German government in 2011, this initiative aims to enhance efficiency and innovation in industrial processes. This transformation is characterised by a shift from centralised to decentralised production control, enabling enhanced communication between humans and machines with data. Following the historic manufacturing milestones of mechanisation, electrification, and advanced electronics, Industry 4.0 is poised to further increase industrial efficiency ([17]).
Although initially centred on manufacturing, Industry 4.0 has adapted to various sectors, including forestry. This has been termed “Forestry 4.0” ([38]). Currently, the practical implementation of Forestry 4.0 remains limited, but this is changing. New Zealand’s forest harvesting sector presents a compelling case for integrating 4.0 concepts and its enabling technologies. The sector has high mechanisation rates with the average harvesting operation involving numerous machines ([43]). These operations generate substantial quantities of underutilised machine data. Collecting, analysing, and using this data (and more) is a key part of 4.0 implementation ([10]).
Adoption of Forestry 4.0 in forest operations will require the integration of new technology, systems, and ways of work for logging contractors. Literature on Forestry 4.0 integration into operations often focuses on the theoretical implementation (Fig. 1), presenting holistic frameworks for the entire forest products supply chain. For example, He & Turner ([15]) highlight several strategic outcomes like cost reduction and increased efficiency, without detailing how systems and technologies required for these outcomes are practically implemented within operations. Similarly, Feng & Audy ([10]) propose their holistic 4.0 framework for the forest supply chain. This underlines the requirement of new technologies such as Cyber-Physical Systems (CPS) and the Internet of Things (IoT) but again, provides little direction on how these are introduced in forest operations, particularly harvesting. In contrast, research on technology integration shows a staircase approach to implementing Forestry 4.0 technologies without realisation of the concept itself. Strandgard & Mitchell ([40]) showcased the beginnings of a CPS with automated time studies using GPS and vibration sensors in forwarders. French ([11]) experimented with computer vision for automating stem detection under yarder grapple carriages. Hoenigsberger et al. ([18]) used machine learning to analyse accidents in harvesting operations, forecasting the injured worker’s absence hours based on their accident. This literature demonstrates CPS integration in forest harvesting and provides developments on localised problems.
Fig. 1 - Forestry 4.0 architecture and enabling technologies ([10]).
The purpose of this article is to develop a framework for implementing Cyber-Physical Systems in forest harvesting operations.
Cyber-Physical Systems (CPSs)
A key concept that enables Forestry 4.0 is a Cyber-Physical System (CPS - [34], [10]). Forestry 4.0 is a broad term, regarding the integration of current and emerging technologies including Artificial Intelligence (AI), IoT, automation, and “smart” operations. Forestry 4.0 encompasses the entirety of the forest supply chain, from the planting of a tree through its transformation into a wood product and its eventual delivery ([10]). CPSs, on the other hand, are a component of Forestry 4.0. A CPS collects and analyses data in real time to provide stakeholders with insights for informed decision-making ([42], [35]). Lee et al. ([25]) suggested a five-step (5C) approach to CPS implementation: (1) data acquisition through smart connections, (2) conversion of data to information, (3) cyber (central hub), (4) cognition in the form of dashboards, and (5) configuration through a feedback loop between the virtual and physical worlds.
Controller Area Network (CAN) communications are a viable option as a data source for the smart connection layer. CAN is a serial communication protocol, developed by Bosch in the mid-1980s and standardised as ISO 11898 ([39]). It is a message-based communication protocol designed to connect Electronic Control Units (ECUs) where electrical noise and other electromagnetic disturbances may cause communication failures. Forest harvesting machinery manufacturers have adopted CAN as their communication protocol in their machines. Researchers have already used this for extracting machine data; for example, Prinz et al. ([37]) analysed CAN data of a Ponsse Scorpion and a Ponsse Ergo, comparing stem diameter and cutting time of trees with the fuel consumption CAN metric.
Converting data to useful information for logging contractors is key to realising the potential of Forestry 4.0. The literature presents several analyses that can provide useful insights, including real-time operation monitoring and predictive maintenance applications.
Mattetti et al. ([27]) studied the mission profile of an agricultural tractor using CAN data. Their analysis showed that the tractor was used for 579 hours over 107 days, resulting in working, idle, and moving states for 65%, 18%, and 16% of the time, respectively. Mattetti et al. ([28]) used machine data for activity-based costing of field operations. The results of the study showed that 59% of the time the tractor was working on on-field activities, it also had a significant idle time of 25%. The cost analysis showed that labour and fuel were the two highest-cost drivers, 71% and 63%, respectively. Choi et al. ([7]) studied driver behaviour using the CAN data, to promote driver safety and distraction alerts in vehicles. The authors used unsupervised learning models to predict if a driver was distracted during driving.
Kruczek et al. ([24]) explored predictive maintenance in mining machinery via two case studies. The first analysed conveyor belt damage using electric current and drivetrain temperature, employing regression analysis for automatic damage period diagnosis and anomaly threshold setting. The second examined “load haul dump machines” (LDHs), utilising engine coolant temperature to identify condition changes, aiding in damage detection and repair verification. Tiddens et al. ([41]) examined predictive maintenance in various industries through six case studies. A notable study involved a model-based method for military helicopter parts to assess their Remaining Useful Life (RUL). This model features three decision-making stages: detection, where it identifies unacceptable situations; diagnostics, evaluating part conditions continuously; and prognostics, estimating RUL after each flight for mission and maintenance planning.
The data and subsequent analyses of multiple machines and vehicles are then merged, creating the central hub (cyberspace) of information. From here, the cognition and configuration steps are integrated within the central hub. Ninikas et al. ([33]) showcase this through the design of a fleet management system for courier operations. Their system eliminated the human factor inefficiencies associated with route selection, significantly improving the routing of courier drivers. This system effectively showcases the cognition and configuration feedback loop between cyberspace and the machines in operation, re-evaluating the machine’s future actions based on newly received data.
Drivers and barriers
Understanding logging business drivers and goals could help expedite the phased transition to Forestry 4.0. The literature on drivers for Industry 4.0 indicates four overarching driver categories: digital, economic, environmental, and social ([6], [19], [32], [46], [5]). For instance, in the manufacturing industry, education, IT infrastructure and its reliability were key in the digital category. Economically, the drivers included maximising production efficiency, minimising costs, mitigating competitive pressure, and enhancing flexibility ([16]). Environmentally, reducing greenhouse gas emissions, waste reduction, and optimising energy consumption were most crucial. The social drivers included upskilling the current workforce, enhancing connectivity between production stages and consumer requirements, and increasing product customisation.
For agriculture, economic drivers are a top priority, with farm size, cost reduction, and total income being the most crucial ([36]). Larger farming businesses, benefiting from economies of scale and facing more complex management challenges are more inclined to adopt 4.0 technologies than smaller farms. In the digital category, education on technology was found to significantly influence its adoption. Farmers’ environmental drivers focused on sustainability, mainly reducing their fertiliser use and wastage.
Historical evidence demonstrates that New Zealand’s forest harvesting industry responds swiftly when motivated by compelling factors. In 2013, a push for better safety and reduced worker harm led to an increase in mechanised steep slope harvesting from 5% to 94% by 2022, indicating the potential for similar adoption rates of 4.0 technologies with the right drivers ([22]). However, this shift may require external support, as seen in international examples like Valentini, an Italian yarding manufacturer ([12]). Valentini integrated a CPS into their machinery, a move facilitated by a government-industry grant ([29], [30]). External support of this nature lowers the cost barrier for a small-medium enterprise, thereby expediting the adoption of 4.0.
There are also cultural barriers to the adoption of 4.0 and its technologies. Traditional organisational cultures can often be resistant to change, inhibiting the transition ([10], [23]). Resistance often stems from a perceived lack of benefit, potential disruption of the current system, or simply a fear of the unknown. Implementing Industry 4.0 technologies including data capturing, transmitting, and storing, are often associated with high upfront costs ([2]).
Technical challenges including the establishment of industry-wide data standards, ensuring robust IT system security against increasing cyber threats, and the technical complexities involved in data protection can make it challenging for 4.0 adoption ([31], [46], [2], [13]). For industries working in remote locations, issues involving reliable data connectivity and robust sensor and data-collecting methods pose significant technological barriers.
Designing a CPS
To implement Forestry 4.0 at the logging contractor level, a simplified four-step process for CPS integration is suggested: (1) data capture, (2) transmission and storage, (3) processing and analysing, and (4) display and decide.
Step 1: Data Capture
For any successful CPS, reliable and autonomous data collection is required. Leveraging existing CAN data streams in logging machinery with data loggers offers a solution for both constraints. The data logger is connected to each machine’s bus system either through the CAN wires directly or through a diagnostic port. In harvesting machines, it is typical for excavators (felling and harvesting machines) to have different branded base machines and heads. The two have separate CAN buses that can be connected using an ISOBUS (ISO 11783) network ([8]). The ISOBUS facilitates communication between the two, allowing the machine seamless use of the felling or harvesting head. It is imperative to check that the implement’s (harvesting or felling head) CAN data is collected via the base machine’s diagnostic port. Where this is unachievable, ensure a second connection of the data logger to the implement’s diagnostic port.
Step 2: transmission and storage
Transmission
Following data acquisition, it is required to be transferred offsite and stored. Several communication protocols could potentially work in the remote, forest environment including Zigbee (IEEE 802.15.4), Cellular (2G to 5G and LTE), Wi-Fi (IEEE 802.11), Bluetooth (IEEE 802.15.1), and LoRa (LoRaWAN) ([3], [26]). Cellular, being the most widely available network, can have limited coverage in remote locations. However, if not, this would be the ideal communication protocol for contractors due to its familiarity, simplicity, and low cost. Similarly, Wi-Fi, particularly when satellite-based and Bluetooth stand out for these reasons. However, Bluetooth’s limited range may hinder its adoption compared to other protocols. LoRa’s effectiveness in forest environments has been demonstrated through research ([3]), however its familiarity when compared to cellular, Bluetooth and Wi-Fi may mean it is viewed less favourably. Zigbee is likely to be viewed similarly for the same reason. Ultimately, the communication protocol(s) adopted should balance familiarity with the technology, whether cellular coverage is available, together with setup and ongoing costs.
Storage
Cloud storage is the final link for transporting the data off-site. Online platforms for data storage (e.g., iCloud, OneDrive, Dropbox), offer advantages over traditional methods such as user-friendliness, security, and cost-effectiveness ([34]). These platforms accept various data types from multiple acquisition systems.
Alternatively, edge computing offers an approach where, rather than sending data off-site, data is processed within the original network, on-site. This concept addresses the challenges of limited service, cloud computing setup, and potential system downtime ([1]). Data processing and analytics are performed onsite and fed back into the system on the same (closed) network, enhancing analytical efficiency as bandwidth issues are reduced. Either option may be suitable for NZ-based logging contractors; however, cloud storage, and particularly cloud data processing (see Step 3) provides significant advantages.
Step 3: processing and analysing
Processing and analysing data are inherently different processes but have been combined in this framework. This was because both processes are often dependent on each other, as many analyses have data processing prerequisites. Combining the two allows for seamless integration within the cloud server and offers more control when implementing new analytics. Simplifying the current CPS frameworks was also a primary reason for combining the two. The framework is designed for contractors to easily understand how each step works.
Processing
Captured CAN data is initially not in a format understandable by humans, requiring a pre-processing step. This is done by applying a DBC (Database CAN) file, which contains the rules for how to decode CAN data. DBC files are available in two main variants: industry-standard (e.g., SAE J1939 for heavy-duty vehicles) and OEM (Original Equipment Manufacturer) specific. The industry standard DBC files encapsulate CAN IDs and signals that are widely recognised across various machine manufacturers. Conversely, OEM-specific DBC files, are unique to the manufacturer’s equipment and are often not available to the public. Reverse-engineering some OEM CAN signals is feasible, however, it is labour-intensive, becomes increasingly complex with the variety of machine brands, requires specialised equipment, and needs domain expertise ([21]).
Analysing
By using decoded CAN data, operational monitoring of harvesting machines can be achieved. As an example, a simple work-time analysis could take the engine speed variable and determine when the machine is idling or operating. This could be done through either predetermined thresholds or using unsupervised classification algorithms such as k-nearest neighbour or random forest. For a more comprehensive analysis of machine usage, additional CAN signals such as joystick movements, button presses, machine orientation and fuel consumption can be included.
CAN data from forest machines contains a variety of engine and hydraulic variables, which can be used for predictive maintenance applications. Machine learning algorithms can give insight into massive volumes of data and have been used in research for anomaly detection, Remaining Useful Life (RUL) analysis, and predictive failure models ([45]). Anomaly detection models are particularly useful in identifying atypical data points or patterns, especially in the absence of training data. RUL models estimate the remaining operational lifespan of a machine or its components, which is valuable for assessing when replacements are necessary ([44]). Predictive failure models require extensive historical data regarding past failures. Their primary function is to anticipate machine, component, or quality failures before they occur. These models could provide logging contractors with detailed information on their machine’s maintenance requirements, possibly improving maintenance scheduling and reducing abrupt failures.
Step 4: display and decide
The design of a user interface allows the presentation of clear and concise information to operators, supervisors, and forest owners for decision support. Graphical User Interface (GUI) dashboards offer a perspective on both machine-level metrics and broader operational performance ([2], [25], [47]). GUIs can allow collaborative decision-making, where automated analyses provide suggestions. In this step, the synergy between the system and human expertise comes to the forefront ([25]). The CPS utilises models from the analysis stage to generate recommendations while the human actions, revises, or declines the CPS-generated solution. In a forestry context, this application might encompass real-time updates to cutting plans, machine path selection, yarder bunch size optimisation, or daily harvesting strategy, for example.
Case study
A CPS was introduced into a New Zealand mechanised forest harvesting operation for 111 working days, which covered two different harvest areas. The first from July 10th to October 5th 2023 was located in Chaney’s Forest (Site A - 43° 25′ 34″ S, 172° 40′ 06″ E) and the second from October 9th 2023 to February 19th 2024 in Ashley Forest (Site B - 43° 11′ 26″ S, 172° 34′ 23″ E).
One data logger was attached to a John Deere® 959 MH felling machine with a SATCO 630E felling head (Tab. 1). The data logger was programmed to connect to a Wi-Fi Local Area Network, with the Wi-Fi hardware located in the machine’s cabin and automatically uploaded data to an Amazon Web Service (AWS) S3 bucket in 50 MB packets. As the data files were uploaded, an AWS Lambda script automatically converted the raw data into a human-readable form using the J1939 protocol ([9]). These decoded CAN files were then stored in an S3 Parquet data lake. AWS Glue (Triggers) and Athena allowed data to be queried and interpreted by third-party software. A Graphical User Interface (GUI) in the form of a dashboard was created using Grafana and then linked to the Athena data source (Fig. 2). This allowed metrics such as engine speed, GPS position, work time, and machine tilt to be displayed in real-time.
Tab. 1 - John Deere 959 MH and SATCO 630E specifications.
Specifications | John Deere 959 MH |
Specifications | SATCO 630E |
---|---|---|---|
Engine Output (kW) | 246 | Weight (kg) | 2.150 |
Engine Torque (Nm) | 1.390 | Capacity (cm) | 12.5 - 86 |
Weight (kg) | 40.910 | Close Min (cm) | 12 |
Rated Speed (rpm) | 1.900 | Open Max (cm) | 128 |
Cab Levelling tilt (deg) | 26 forward, 14 rear |
Saw | 43″ bar with ¾ inch chain |
Cab Levelling tilt (deg) | ± 7 side | Saw Motor (cc) | 45 Rexroth motor |
To calculate the work time, the engine speed variable was used. Eight hundred and ninety to 910 Revolutions Per Minute (RPM) was considered “idling”, >1800 RPM was considered “operating”, 0 (zero) RPM was “engine off”, and the remainder was labelled as “idling up and down”. These ranges were based on the machine specifications and information provided by the operator. Idle was set at 900 RPM, and the rated speed was around 1900 RPM - hence a lower threshold of 1800 was used. This was then taken a step further including joystick CAN signals to determine the amount of time the machine was tracking (working state) when “operating”. The machine was considered “tracking” when either joysticks 3 or 4 were in use (> 0%). The pitch and roll angles of the machine were then examined using their respective CAN signals. Extended pitch and roll angle signals were ignored due to sensor degradation alerts in the dataset. Finally, the engine fuel rate variable was used to determine the fuel consumption (l h-1) of the machine in its different working states (Tab. 2).
Tab. 2 - Example and results of potential CAN data analyses for forest harvesting machinery.
Characteristic | Feature | Site A | Site B | Total |
---|---|---|---|---|
Efficiency (%) | Operating | 75.7 | 80.5 | 77.6 |
Idling | 19.3 | 16.8 | 18.3 | |
Idling Up and Down | 0.7 | 0.5 | 0.6 | |
Engine Off | 4.3 | 2.2 | 3.5 | |
Tracking (%) | Stationary | 41.2 | 45.2 | 42.9 |
Tracking | 58.8 | 54.8 | 57.1 | |
Roll angle (%) | 0 to +/- 5 | 72.8 | 49.4 | 63.5 |
+/-5 to +/-10 | 23.9 | 32.1 | 27.2 | |
+/-10 to +/-15 | 3.3 | 18.5 | 9.2.3 | |
15+ | 0.0003 | 0 | 0.0002 | |
Pitch angle (%) | -10 to -5 | 3.6 | 0.3 | 2.3 |
-5 to 0 | 58.9 | 6.9 | 38.3 | |
0 to 5 | 32.4 | 14.4 | 25.2 | |
5 to 10 | 4.1 | 21.8 | 11.4 | |
10 to 20 | 0.9 | 51.0 | 20.8 | |
20+ | 0.02 | 5.6 | 2.1 | |
Fuel consumption by working state (l h-1) | Operating | 35.7 ± 15.9 | 34.3 ± 15.3 | 35.1 ± 15.7 |
Operating (Stationary) | 25.3 ± 13.7 | 27.2 ± 13.5 | 26.1 ± 13.7 | |
Operating (Tracking) | 43.0 ± 12.9 | 40.1 ± 14.2 | 41.9 ± 13.5 | |
Idling | 2.0 ± 0.4 | 2.0 ± 0.4 | 2.0 ± 0.4 | |
Idling Up and Down | 7.1 ± 10.3 | 6.5 ± 9.2 | 6.9 ± 10.0 |
The analysis reveals that the felling machine at Site B had a utilisation 4.8% greater than Site A. Similarly, fuel consumption data indicate that, overall, Site B’s machine operated more fuel-efficiently than that at Site A. However, Site A exhibited greater fuel efficiency when the machine was stationary. The results for roll and pitch angles underscore the terrain differences between the two sites: Site A is relatively flat, with 72.8% of roll angles and 91.3% of pitch angles within the -5 to +5 degrees range. In contrast, Site B features steeper terrain, with pitch and roll angles predominantly in the -5 to -15 and 5 to 20 degrees range. Despite these terrain differences, they are not mirrored in the fuel consumption analysis, whereas Site B’s tracking fuel consumption was significantly lower than Site A’s. This discrepancy may result from operational planning, where the contractor has limited the machine’s time spent tracking uphill. This minimised load on the engine, resulting in lower fuel consumption.
Discussion
By modifying the CPS framework by Lee et al. ([25]), a simplified CPS was designed for a New Zealand case study. The CPS has four functions: data capture, transmission and storage, processing and analysing, and display and decide. The CPS was then applied to an active felling machine in New Zealand over 111 days. The system enabled near-real-time analytics of operational efficiency, fuel consumption, and pitch and roll angle metrics in a real harvesting environment.
Literature on deployed CPSs and real-time analysis in forest harvesting operations is limited. Research such as Prinz et al. ([37]) shows the potential of CAN data analysis in gaining more insight into machines’ inner workings in harvesting operations. Bacescu et al. ([4]) used John Deere’s telematics system JDLink™ to conduct similar analyses seen in this paper on two forwarders and two harvesters. Both analyses are not conducted in real time, showing the use of such a system, albeit with limited realisation of Forestry 4.0.
Although this research shows one implementation pathway of a CPS in mechanised harvesting operations, there are still several challenges that need to be overcome. Firstly, using the J1939 dictionary to decode CAN signals from harvesting machines provides an array of variables, however, OEM-specific variables remain undecoded. These remaining variables potentially hold more useful data for contractors. This analysis would have benefited from key metrics (decoded CAN signals) such as when the main saw was engaged, or the grapple arm position (0-100% closed). Accessing these CAN signals and others similar will improve the insights gained through this system.
A possible solution to this is the inclusion of machine learning models in the analysis step to determine the operational status of machines or to decode OEM signals. Using the current CAN signals available, machine learning models can identify patterns that coincide with the specific tasks the machine is carrying out. For example, joystick inputs, felling head position, and engine load patterns could be used to determine whether the machine was felling, shovelling, or repositioning in the stand. This could then be used for further analyses such as determining productivity as a function of the forest stand variables and work patterns.
The second key limitation of the tested CPS was the need for cellular service to transfer the data offsite. As New Zealand’s production forests are often located in areas with limited or no cellular service, the CPS is not robust for real-time transfer to the online server. Recently, there has been significant growth in satellite Wi-Fi capabilities such as Starlink™. This is a key constraint, and it is recognised that any data transfer service adopted by a forest harvesting sector pushing for 4.0 must be both reliable in remote locations and capable of moderate data upload rates.
The final challenge is the dynamic relationship between the logging contractor and the forest owner or contracted manager. Currently, in New Zealand, there is a limited exchange of “data” between the two parties. Full adoption of Forestry 4.0 such as ideas like “live log priority setting to customer demand” may require a review of what is traded between the logging contractor and forest owner/manager, how harvesting is managed, and how that is valued. The most obvious issue the new system presents relates to the ownership rights of the captured data. Establishing ownership is often a difficult task due to the complexity of defining what ownership means ([20]). This complexity is compounded when considering the entitlements to use and access the data ([14]). Thus, it is imperative to establish clear boundaries concerning these rights before commencing data sharing between contracted parties.
Conclusion
There are some challenges ahead for the adoption of Forestry 4.0 in fully mechanised forest harvesting operations. This research demonstrates the ability to layer existing technologies to create a CPS within a current harvesting operation in a way that partially fulfils the needs of 4.0. The technical ability is shown; now, it is crucial to tailor 4.0 developments to the specific decision-support needs of harvesting contractors. Doing so will more clearly showcase the potential to enhance harvesting business and production.
Acknowledgements
This study is funded by Forest Growers Research New Zealand and is part of their wider project “Automation of Cable Yarding”.
References
CrossRef | Gscholar
CrossRef | Gscholar
CrossRef | Gscholar
CrossRef | Gscholar
Authors’ Info
Authors’ Affiliation
Campbell Harvey 0000-0002-2445-4942
Rien Visser 0000-0003-2137-9198
School of Forestry, University of Canterbury (New Zealand)
Corresponding author
Paper Info
Citation
Humphrey P, Harvey C, Visser R (2024). Deploying an early-stage Cyber-Physical System for the implementation of Forestry 4.0 in a New Zealand timber harvesting context. iForest 17: 353-359. - doi: 10.3832/ifor4651-017
Academic Editor
Marco Borghetti
Paper history
Received: May 27, 2024
Accepted: Aug 31, 2024
First online: Nov 13, 2024
Publication Date: Dec 31, 2024
Publication Time: 2.47 months
Copyright Information
© SISEF - The Italian Society of Silviculture and Forest Ecology 2024
Open Access
This article is distributed under the terms of the Creative Commons Attribution-Non Commercial 4.0 International (https://creativecommons.org/licenses/by-nc/4.0/), which permits unrestricted use, distribution, and reproduction in any medium, provided you give appropriate credit to the original author(s) and the source, provide a link to the Creative Commons license, and indicate if changes were made.
Web Metrics
Breakdown by View Type
Article Usage
Total Article Views: 3539
(from publication date up to now)
Breakdown by View Type
HTML Page Views: 1475
Abstract Page Views: 926
PDF Downloads: 930
Citation/Reference Downloads: 1
XML Downloads: 207
Web Metrics
Days since publication: 290
Overall contacts: 3539
Avg. contacts per week: 85.42
Article Citations
Article citations are based on data periodically collected from the Clarivate Web of Science web site
(last update: Mar 2025)
(No citations were found up to date. Please come back later)
Publication Metrics
by Dimensions ©
Articles citing this article
List of the papers citing this article based on CrossRef Cited-by.
Related Contents
iForest Similar Articles
Research Articles
Comparison of alternative harvesting systems for selective thinning in a Mediterranean pine afforestation (Pinus halepensis Mill.) for bioenergy use
vol. 14, pp. 465-472 (online: 16 October 2021)
Research Articles
Modifying harvesting time as a tool to reduce nutrient export by timber extraction: a case study in planted teak (Tectona grandis L.f.) forests in Costa Rica
vol. 9, pp. 729-735 (online: 03 June 2016)
Research Articles
Exploring the reliability of CAN-bus data in assessing forwarder rolling resistance under real working conditions
vol. 17, pp. 360-369 (online: 13 November 2024)
Research Articles
NIR-based models for estimating selected physical and chemical wood properties from fast-growing plantations
vol. 15, pp. 372-380 (online: 05 October 2022)
Research Articles
Physical, chemical and mechanical properties of Pinus sylvestris wood at five sites in Portugal
vol. 10, pp. 669-679 (online: 11 July 2017)
Research Articles
Mechanical and physical properties of Cunninghamia lanceolata wood decayed by brown rot
vol. 12, pp. 317-322 (online: 06 June 2019)
Short Communications
Changes in Populus sp. wood subjected to heat treatment: anatomy and silica content
vol. 18, pp. 223-226 (online: 09 August 2025)
Research Articles
Improving sustainability in wood coating: testing lignin and cellulose nanocrystals as additives to commercial acrylic wood coatings for bio-building
vol. 14, pp. 499-507 (online: 11 November 2021)
Research Articles
Examining the evolution and convergence of wood modification and environmental impact assessment in research
vol. 10, pp. 879-885 (online: 06 November 2017)
Research Articles
Identification of wood from the Amazon by characteristics of Haralick and Neural Network: image segmentation and polishing of the surface
vol. 15, pp. 234-239 (online: 14 July 2022)
iForest Database Search
Search By Author
Search By Keyword
Google Scholar Search
Citing Articles
Search By Author
Search By Keywords
PubMed Search
Search By Author
Search By Keyword