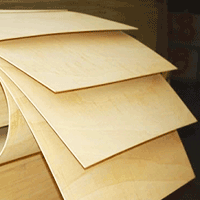
Physical-mechanical properties and bonding quality of heat treated poplar (I-214 clone) and ceiba plywood
iForest - Biogeosciences and Forestry, Volume 8, Issue 5, Pages 687-692 (2014)
doi: https://doi.org/10.3832/ifor1276-007
Published: Dec 17, 2014 - Copyright © 2014 SISEF
Research Articles
Abstract
The present paper investigates the physical and mechanical modifications of both poplar (I-214 clone) and ceiba veneers and plywood after heat treatments of different intensities (5 and 7 % of dry mass losses). Plywood panels were glued before and after heat treatment with urea-formaldehyde (UF) and melamine-urea-formaldehyde (MUF) resins. In order to assess the treatments’ effects on both the wood and the glues, the dry mass, the density, the bending strength, the Young’s modulus and the bonding quality were measured before and after heat treatment. The results of the different treatments were compared as well. Results showed that the loss in cell wall polymers due to the heat treatment caused a significant reduction of the equilibrium moisture content of the samples. From a mechanical point of view the treatment resulted in an important reduction of strength and in a small reduction of stiffness. Bonding quality as well as mechanical properties were widely affected by the heat treatment. The different intensities of the treatments (the treatment range was up to 5% and 7% of dry mass loss) did not show significant differences for most of the features assessed. The mechanical performance as well as the bonding quality of treated samples suggested that veneers should be glued after heat treatment. Apparent cohesive wood failure showed that different degradations affect wood and glues with a prominent effect on the glues for UF resins and a prominent effect on the wood for MUF resins.
Keywords
Heat Treatment, Poplar, Ceiba, Plywood, Bonding Quality, Physical-mechanical Properties
Introduction
Heat Treatment (HT) represents one of the possible solutions applied in order to permanently modify wood properties. According to various review articles ([10], [9], [11], [15]) HT is currently applied to timbers both from broadleaves (beech, ash, poplar) and coniferous species (spruce, pine). In particular, the change of water-related properties of heat-treated poplar was recently studied by Bak & Németh ([1]), who showed that a treatment at 160 °C reduced the equilibrium moisture content.
HT results in relevant modification of the physical and mechanical properties of wood. From a physical point of view, moderate HT results in a reduction of density, a reduction of equilibrium moisture content (EMC), an improvement of dimensional stability, an improvement of the decay resistance to Fungi and in a darkening of wood natural color. From a mechanical point of view, moderate HT results in a reduction of bending strength, in small variations of stiffness, in an improved hardness and in a reduction of shear strength.
Of great interest to the present work are the effects produced by HT on the main constitutive polymers of the cell wall. The losses of hygroscopic hemicelluloses, converted into furan base polymers, predominantly furfural and hydrossymethilfurfural ([11]), have on HT wood two main effects: a reduction of the total shrinkage and a reduction of wood mass according to the treatment intensity. The losses of dry mass make the material lighter and suitable for the production of very light wooden products if low density wooden species, e.g., poplar (Populus sp.) and ceiba (Ceiba pentandra (L.) Gaertn.), are chosen as the base material to be treated.
Rather limited is the literature available regarding applications of HT to wood derivatives, in particular to plywood. Experimental studies were conducted on laminated beams by Sernek et al. ([16]) and Poncsák et al. ([14]), and on oriented strand boards (OSB) with strands treated before gluing by Paul et al. ([13]). Tests on the mechanical characteristics of HT poplar laminated veneer lumber (LVL) were carried out by Nazerian & Ghalehno ([12]) and other studies on the mechanical resistance of silver nanoparticles-impregnated poplar were conducted by Taghiyari ([17]). Conversely, no information is available about HT on ceiba wood and its derivatives.
The present work aims to investigate the possible application of HT to poplar and ceiba plywood in order to improve their dimensional stability, durability and water repellency, all essential requirements to make these products suitable for external use.
Main goals of the experimentation were to determine if HT can be considered consistent with the glues actually used for plywood production and if HT should be better applied on veneers or directly on the glued panels.
In order to achieve these goals, poplar and ceiba veneers and plywood were heat treated at 180-190 °C up to a reduction of 5% and 7% of the initial dry weight. The treatments were carried out on the following experimental materials:
- veneers;
- plywood assembled before HT and bonded with urea-formaldehyde (UF) resins;
- plywood assembled before HT and bonded with melamine-urea-formaldehyde (MUF) resins;
- plywood assembled after HT of the veneers and bonded with MUF resins.
Materials and methods
The effect of HT was assessed by the comparison between control and treated samples for the following features:
- physical properties (mass and density);
- Young’s modulus (Modulus of Elasticity, MOE) of the panels;
- bending strength (Modulus of Rupture, MOR) of the panels; bonding quality (shear strength, apparent cohesive wood failure).
Heat treatments were applied to panels or veneers with dimensions 400 × 400 mm. Panels or veneers made of poplar (I-214 clone) or ceiba were first conditioned to SEC (for abbreviations, see Box 1), then measured and weighed. The base material used in the tests is reported in Tab. 1.
Box 1 - List of abbreviations.
The following abbreviations are used throughout the text:
- SEC: standard environmental conditions, 20 °C and 65 % RH;
- ODS: oven dry state, 103 ± 3 °C;
- M0: untreated oven dry mass [kg];
- M12: untreated mass at SEC [kg];
- ML0: mass loss because of thermal treatment at ODS referred to M0 [%];
- ML12: mass loss at SEC because of thermal treatment referred to M12 [%];
- ρ12: untreated density at SEC [kg m-3];
- ρL12: density loss because of thermal treatment at SEC referred to ρ12 [%];
- fv: shear strength;
- ACWF: apparent cohesive wood failure
Tab. 1 - Material subjected to heat treatment. The group codes indicate: species_ product_glue. (Species): poplar or ceiba; (product): panel (P) or veneer (V); (glue): UF or MUF. (#): number of samples measured and averaged.
Tested material |
Layers | Thickness (mm) |
---|---|---|
poplar_V | 1 | 2.2 #15 |
ceiba_V | 1 | 1.7 #10 |
poplar_P_UF | 3 | 5.4 #10 |
poplar_P_MUF | 5 | 9.3 #6 |
In order to start HT from exactly the same stage, samples were oven dried at 103 ± 3 °C. M0 was considered as a reference for the following thermal treatments, where ML0 is expressed as a % of M0.
Two heat treatments were applied: T1 - up to a ML0 of ~ 5 % - and T2 - up to a ML0 of ~ 7 % - laying the veneers and panels in an oven at 180-190 °C for different time periods. Panels were bonded using urea-formaldehyde (UF) and melamine-urea-formaldehyde (MUF) resin systems, respectively able to meet the requirements of bonding quality class 1 and 2 of EN 314, and hot pressed at 110 °C for 2 minutes at with a pressure of 0.6 MPa. Final panels satisfied the requirements of formaldehyde emission class E1 (EN 13986), complying with the national legislation ([2]). MUF resins were chosen since they are suitable for combining technical and economic feasibility. Testing was performed on UF glues as well for comparison.
Tab. 2 reports the complete set of panels each with its dimensions, number of layers and test performed. Panels glued before HT (i.e., the glue line is thermally treated as well) are reported with the suffix _pre, while panels glued after heat treatment (i.e., the glue line is not heat treated) are reported with the suffix _post. The control samples are reported with _test.
Tab. 2 - The experimental matrix. Group codes indicate: species_product_glue_treatment_ glue-application. For each group, _test is the control sample. (Species): poplar or ceiba; (product): panel (P) or veneer (V); (glue): UF or MUF; (treatment): test, 5% of dry mass loss (T1) and 7% of dry mass loss (T2). As regards bonding quality (EN 314-1): pre-treatment 5.1.1 means holding the specimens 24 hours in water at 20 °C, pre-treatment 5.1.2 means holding 6 hours the samples in boiling water and followed by cooling in water for at least 1 hour. The measured parameters are shear strength (fv) and wood fibre failure (wff). (#): number of samples tested. (L-T): longitudinal and transversal samples according to EN314.
Tested material | Layers | Panel thickness | Test EN 310 | Test EN 314-1 |
---|---|---|---|---|
poplar_P_UF_test | 3 | 5.4 #10 | MOE-MOR (L-T) | 5.1.1, fv, wff, acc |
poplar_P_UF_T1_pre | 3 | 4.3 #10 | MOE-MOR (L-T) | 5.1.1, fv, wff, acc |
poplar_P_UF_T2_pre | 3 | 5.2 #10 | MOE-MOR (L-T) | 5.1.1, fv, wff, acc |
poplar_P_MUF_test | 5 | 9.3 #06 | MOE-MOR (L-T) | 5.1.2, fv, wff, acc |
poplar_P_MUF_T1_pre | 5 | 9.2 #02 | MOE-MOR (L-T) | 5.1.2, fv, wff, acc |
poplar_P_MUF_T2_pre | 5 | 9.1 #03 | MOE-MOR (L-T) | 5.1.2, fv, wff, acc |
poplar_P_MUF_test | 5 | 8.8 #10 | MOE-MOR (L-T) | 5.1.2, fv, wff, acc |
poplar_P_MUF_T1_post | 5 | 7.6 #10 | MOE-MOR (L-T) | 5.1.2, fv, wff, acc |
poplar_P_MUF_T2_post | 5 | 8.2 #06 | MOE-MOR (L-T) | 5.1.2, fv, wff, acc |
ceiba_P_MUF_test | 5 | 7.5 #04 | MOE-MOR (L-T) | 5.1.2, fv, wff, acc |
ceiba_P_MUF_T1_post | 5 | 7.3 #04 | MOE-MOR (L-T) | 5.1.2, fv, wff, acc |
Moisture content (MC) and density of _post panels were determined according to EN 322 and EN 323 technical standards. MC and density of _pre panels were determined according to the above mentioned standards with the exception of the samples with larger dimensions, because the treatment was performed on the whole panel that was then divided into samples after the treatment.
MOE and MOR of the panels were determined on small specimens for longitudinal (L) and transversal (T) direction according to the EN 310 and EN 326-1 standards. Bonding quality was determined according to the EN 314 standard using the pre-treatment 5.1.1 for UF resins and 5.1.2 for MUF resins. Pre-treatment 5.1.1 consists of holding the specimens 24 hours in water at 20 °C before testing, and pre-treatment 5.1.2 consists of holding the samples 6 hours in boiling water followed by at least 1 hour in cold water. According to the EN 314, fv and ACWF were determined. Regarding ACWF the EN 314 standard envisages to reject and repeat the tests where the failure occurs across the wood layers (i.e., perpendicularly to the glue line). In several cases, after treatment, the failure occurred perpendicularly to the glue line and the test could not be repeated due to the limited availability of specimens. In this case it was chosen to indicate the property as “non EN ACWF”. Statistical analysis was performed using the R software (R Foundation, Vienna, Austria - ⇒ http:// www.r-project.org/). The Mann-Whitney test for independent values, along with the Kruskal-Wallis non-parametric test and the pairwise Wilcoxon’s test as a post-hoc, were used for the statistical analysis. The homoscedasticity was verified by a non-parametric Levene’s test.
Results and discussion
Physical characterization of the material
ρ12, ρL12 and ML0 of veneers and panels glued before treatment (_pre) are reported in Tab. 3. Each of these data refer to the same samples before treatment (paired data). Once the veneers were treated they were assembled into plywood panels with MUF resins (_post) and ρ12 was determined. For _post panels ρL12 refers control samples (independent data) and the results are reported in Tab. 4.
Tab. 3 - Heat-treated base materials and their main physical properties before and after the treatment. Group codes indicate: species_product_glue_treatment_glue-application. For each group, _test is the control sample. (Species): poplar or ceiba; (product): panel (P) or veneer (V); (glue): UF or MUF; (treatment): test, 5% of dry mass loss (T1) and 7% of dry mass loss (T2); glue application before heat treatment of the veneers (_pre) or after heat treatment of the veneers (_post). (#): number of samples tested. Standard deviation (where available) is in brackets. (NA): not applicable.
Type | Tested material |
ρ12 pre treatment (kg m-3) |
Veneers / Panels |
T (°C) |
Treat. Time (hh) |
ρL12 (%) |
ML0 (%) |
ML12 (%) |
Thickness (mm) |
---|---|---|---|---|---|---|---|---|---|
Heat treated veneers |
poplar_V_test | 327 #05 (8) | V | - | - | - | - | - | - |
poplar_V_T1 | 319 #05 (14) | V | 180 | 23 | NA | 5.7 | 8.3 | - | |
poplar_V_T2 | 315 #05 (8) | V | 180 | 33 | NA | 6.7 | 8.2 | - | |
ceiba_V_test | 300 #05 (16) | V | - | - | - | - | - | - | |
ceiba_V_T1 | 305 #05 (11) | V | 180 | 23 | NA | 6.9 | 9 | - | |
Heat treated plywood |
poplar_P_UF_test | 459 #10 (10) | P | - | - | - | - | - | 5.4 (0.1) |
poplar_P_UF_T1_pre | 460 #05 (4) | P | 180 | 23 | 6.5 | 4.6 | 7.9 | 5.3 (0.0) | |
poplar_P_UF_T2_pre | 454 #05 (7) | P | 180 | 33 | 7.0 | 6.2 | 8.9 | 5.2 (0.1) | |
poplar_P_MUF_test | 454 #03 (17) | P | - | - | - | - | - | 9.4 (0.1) | |
poplar_P_MUF_T1_pre | 459 #04 (18) | P | 190 | 8 | 7.0 | 4.9 | 9.8 | 9.0 (0.0) | |
poplar_P_MUF_T2_pre | 474 #02 (8) | P | 190 | 23 | 9.9 | 7.6 | 12.1 | 9.2 (0.1) |
Tab. 4 - Panels realized by gluing heat treated veneers, main physical properties. Group codes indicate: species_product_glue_treatment_glue-application. For each group, _test is the control sample. (Species): poplar or ceiba; (product): panel (P) or veneer (V); (glue): UF or MUF; (treatment): test, 5% of dry mass loss (T1) and 7% of dry mass loss (T2), glue application before heat treatment of the veneers (_pre) or after heat treatment of the veneers (_post). (#): number of samples tested. Standard deviation (where available) is in brackets.
Tested material | ρ12 (kg m-3) |
Veneers / Panels |
ρL12 (%) |
Thickness (mm) |
---|---|---|---|---|
poplar_P_MUF_test | 490 #10 (31) | P | - | 8.8 (0.1) |
poplar_P_MUF_T1_post | 496 #10 (22) | P | -1.2 | 7.6 (0.4) |
poplar_P_MUF_T2_post | 457 #10 (23) | P | 6.7 | 8.2 (0.2) |
ceiba_P_MUF_test | 401 #04 (9) | P | - | 7.5 (0.1) |
ceiba_P_MUF_T1_post | 377 #04 (15) | P | 6.0 | 7.3 (0.1) |
As displayed in Fig. 1, for veneers and panels glued before treatment, ρ12, M0 and M12 show a clear reduction. The largest reduction affects M12, the lower M0. This observation confirms that part of the mass is loss due to cell wall components’ degradation and part due to the lower EMC after treatment at the same environmental conditions. ρL12 (where available) lays between ML0 and ML12, since a given ML0 corresponds to a given permanent dimensional loss that finally results in a lower reduction of density as compared with that of the mass.
Fig. 1 - Graph of ρL12 (density loss at standard environmental conditions because of treatment), ML0 (oven dry mass loss because of treatment) and ML12 (mass loss because of treatment at standard environmental conditions) for different treatments and materials treated.
With regards to panels glued after treatment, in one case an increase of density is recorded (Tab. 4). This behavior is explained by the occurrence of permanent deformation during pressing operations (consequence of the reduction of the ultimate strength of the material after HT). In fact, as from Tab. 4, for the increased density a permanent reduction of thickness is observed if compared with the other treatments (7.6 mm of poplar T1 treatment against the 8.8 mm of the test and 8.2 of T2 treatment). This observation highlights a very relevant manufacturing problem for panels assembled after HT process.
Among the analyzed parameters, the difference between ML12 and ML0 (ΔML12-0) has shown to be sensitive to the material and not to the type of treatment. T1 and T2 treatments in fact have not shown statistically significant differences by a Mann-Whitney test for independent values. T1 and T2 groups were then analyzed together using a Kruskal-Wallis non-parametric test, highlighting statistically significant differences between the different materials used. A pairwise Wilcoxon’s test for independent values used as post-hoc test has shown statistically significant differences between all the groups except between poplar and ceiba, both to be considered as massive wood (Fig. 2).
Fig. 2 - Difference between ML12 (mass loss at standard environmental conditions) and ML0 (mass loss at oven dry state) with T1 and T2 results pooled together.
Fig. 2 displays how the heat treatment of massive wood corresponds to a cell wall degradation that leads to a ΔML12-0 of about 2-2.5 %. In the case of the panels glued before heat treatment the degradation leads to about a 3 % difference for panels glued with UF resins and to about a 4.5 % difference for panels glued with MUF resins. This can be explained by different behaviors in the re-collocation of water between massive wood and glues, with a measurable difference between UF and MUF glues.
Mechanical characterization of the material
Longitudinal (L) and transversal (T) MOE and MOR results are summarized in Tab. 5. The non-valid (NV) values reported therein are due to the fact that none of tested specimens was broken within the time of 60 ± 30 seconds required by the EN 310 standard. For every material, values of the treated samples were compared with the control sample by means of Kruskal-Wallis non-parametric test. Where statistically significant, differences were highlighted, and a Pairwise Wilcoxon test for independent values was performed. Statistical analyses revealed no significant differences among MOEs, for either L or T samples. For MOR, a statistically significant difference was observed among the controls, and both T1 and T2 treatments and in some case differences between T1 and T2 were highlighted too.
Tab. 5 - Mechanical performances of treated and test panels according to EN 310. (_post): glued after thermal treatment; (_pre): glued before treatment. (NV): non-valid value because all the specimens tested were broken outside the time window of 60 ± 30 seconds prescribed by the EN 310. (#): number of samples tested.
Tested material | MOE L (MPa) | Group | MOR L (MPa) | Group | MOE T (MPa) | Group | MOR T (MPa) | Group |
---|---|---|---|---|---|---|---|---|
poplar_P_UF_test | 7993 #28 | a | 66 #30 | a | NV | NV | 18 #22 | a |
poplar_P_UF_T1_ pre | 7616 #3 | a | 47 #18 | b | NV | NV | 11 #14 | b |
poplar_P_UF_T2_pre | NV | NV | 45 #18 | b | NV | NV | 8 #14 | b |
poplar_P_MUF_test | 5448 #30 | a | 48 #30 | a | 3123 #30 | a | 33 #30 | a |
poplar_P_MUF_T1_pre | 4924 #18 | a | 30 #18 | b | 3020 #18 | a | 23 #12 | b |
poplar_P_MUF_T2_pre | 5471 #12 | a | 23 #18 | c | 2947 #4 | a | 15 #12 | c |
poplar_P_MUF_Test | 6507 #6 | a | 51 #6 | a | 2304 #6 | a | 30 #6 | a |
poplar_P_MUF_T1_post | 6496 #12 | a | 38 #12 | b | 2143 #12 | a | 19 #12 | b |
poplar_P_MUF_T2_post | 6335 #6 | a | 35 #6 | b | 2029 #6 | a | 18 #6 | b |
ceiba_P_MUF_test | 3447 #3 | a | 37 #3 | a | 1178 #3 | a | 18 #3 | a |
ceiba_P_MUF_T1_post | 3645 #3 | a | 24 #3 | b | 1268 #2 | a | 13 #3 | b |
Based on statistical analysis, no significant differences arose on MOE after HT, while for MOR relevant reductions were detected. MOR reductions, both for L and T samples, are reported in Fig. 3. As a general rule, _post (glued after treatment) panels present better performances than _pre (glued before treatment) panels, and in some cases it is documented that T2 treatment results in a higher MOR reduction if compared to T1 treatment. For UF resins, the transversal samples present larger MOR reductions when compared to longitudinal samples, even though it cannot be determined whether this is a consequence of the resins or of the number of layers. As for MUF resins, _post panels presented better results than _pre panels.
Bonding quality
Bonding quality was tested according to EN 314-1, 2 standards with 5.1.1 protocol for UF resins and 5.1.2 protocol for MUF resins. The main results are summarized in Tab. 6. For every case the treated panels showed a lower fv than control panels. Such differences were determined to have statistical significance by a Kruskal-Wallis test and by a pairwise Wilcoxon’s test for independent values as post-hoc test. Both T1 and T2 presented statistically significant differences with the control sample and in one case even differences between T1 and T2 treatments could be detected.
Tab. 6 - Bonding performances of treated and test panels according to EN 314. (_post): glued after thermal treatment; (_pre): glued before treatment; (fv): shear strength; (ACWF): percentage of apparent cohesive wood failure. (#): number of samples tested.
Tested material | Test | fv (MPa) |
Group | non EN ACWF (%) |
Group |
---|---|---|---|---|---|
poplar_P_UF_test | 5.1.1 | 0.9 #24 | a | 90 | a |
poplar_P_UF_T1_pre | 5.1.1 | 0.3 #12 | b | 86 | a |
poplar_P_UF_T2_pre | 5.1.1 | 0.2 #12 | b | 90 | a |
poplar_P_MUF_test | 5.1.2 | 1.3 #45 | a | 36 | a |
poplar_P_MUF_T1_pre | 5.1.2 | 0.4 #45 | b | 100 | b |
poplar_P_MUF_T2_pre | 5.1.2 | 0.3 #30 | c | 100 | b |
poplar_P_MUF_test | 5.1.2 | 1.4 #18 | a | 57 | a |
poplar_P_MUF_T1_post | 5.1.2 | 0.5 #30 | b | 88 | b |
poplar_P_MUF_T2_post | 5.1.2 | 0.6 #18 | b | 97 | b |
ceiba_P_MUF_test | 5.1.2 | 0.8 #12 | a | 100 | a |
ceiba_P_MUF_T1_post | 5.1.2 | 0.3 #12 | b | 100 | a |
Fig. 4 shows the reduction of fv after T1 and T2 referred to the control sample. The fv reduction for MUF resins, though tested following the 5.1.2 protocol, is in line with the reduction of UF resins, tested following the 5.1.1 protocol. This fv reduction can be ascribed to the decreased wood mechanical properties, to the thermal degradation of the glues during HT for _pre panels and to the lower adhesion properties of glues to the heat-treated wood for _post panels.
Fig. 4 - Shear strength reduction of panels with different treatments as referred to a control sample, after EN 314 method.
In order to understand the influence of the thermal treatment on the glue and on the wood, respectively, ACWF was determined. As already mentioned, ACWF was determined with some differences with respect to the EN 314 standard and it is mentioned as “non EN ACWF”. Results are reported in Fig. 5, and can be summirized as follows:
Fig. 5 - Percentage of apparent cohesive wood failure for the control samples and groups of samples subjected to different heat treatments.
- UF poplar panels glued before HT show a high value of non EN ACWF for the control and for both T1 and T2 treatments. This means that the treatment affects the glue and the wood in a similar way.
- MUF poplar panels glued before HT present a lower non EN ACWF if compared with T1 and T2. This indicates that the failure occurs mainly on the glue instead of the wood, and that the HT determines a larger degradation of wood than of the glue resulting in an increased non EN ACWF.
- MUF poplar panels glued after HT show a trend very similar to MUF panels glued before heat treatment, indicating that this behavior is mainly dependent upon the wood rather than the glues.
- MUF ceiba panels glued after treatment both for treated or untreated samples permanently break on wood, indicating that for ceiba the strength of material is the prominent problem compared to glues degradation.
Conclusions
Treated panels have shown mass and density reductions at dry state, after treatment, as well as at standard environmental conditions after re-moisturizing. The loss in dry mass resulted lower than that at standard environmental conditions and to that of density, indicating that the loss in cell wall polymers (e.g., hemicellulose) determined by the treatment significantly affects EMC.
As far as ML12 and ML0 are concerned, the difference between the two values of mass was dependent on the type of products treated (massive wood, MUF panels glued before treatment and UF panels glued before treatment). However, differences in mass losses within the same product were constant (not significant differences) either after treatment T1 or T2, suggesting that the treated material is more important than the treatment intensity.
On each product, both the treatment and its intensity showed a significant influence on MOR, but no influence on MOE values was observed (variations not statistically significant). Differences in MOR values were always present between the control and the treated samples in all the directions tested, but only occasionally between the two treatments’ intensity (T1 and T2). The higher MOR loss was detected for samples glued before HT as compared with samples glued after treatment.
Large reductions of shear strength were observed even with better results for the specimens glued after treatment compared with specimens glued before treatment.
Apparent cohesive wood failure shows that different degradations affect wood and glues with a prominent effect on glues for UF resins and a prominent effect on the wood for MUF resins.
Acknowledgements
The authors acknowledge the financial support of the Regional Administration of Tuscany through the POR CReO project line, as well as the FESR.
References
Gscholar
Gscholar
Authors’ Info
Authors’ Affiliation
Marco Fioravanti
GESAAF, University of Florence, v. S. Bonaventura 13, I-50145 Firenze (Italy)
Francesco Negro
Roberto Zanuttini
DiSAFA, University of Turin, v. L. da Vinci 44, I-10095 Grugliasco (TO - Italy)
Corresponding author
Paper Info
Citation
Goli G, Cremonini C, Negro F, Zanuttini R, Fioravanti M (2014). Physical-mechanical properties and bonding quality of heat treated poplar (I-214 clone) and ceiba plywood. iForest 8: 687-692. - doi: 10.3832/ifor1276-007
Academic Editor
Marco Borghetti
Paper history
Received: Feb 24, 2014
Accepted: Sep 11, 2014
First online: Dec 17, 2014
Publication Date: Oct 01, 2015
Publication Time: 3.23 months
Copyright Information
© SISEF - The Italian Society of Silviculture and Forest Ecology 2014
Open Access
This article is distributed under the terms of the Creative Commons Attribution-Non Commercial 4.0 International (https://creativecommons.org/licenses/by-nc/4.0/), which permits unrestricted use, distribution, and reproduction in any medium, provided you give appropriate credit to the original author(s) and the source, provide a link to the Creative Commons license, and indicate if changes were made.
Web Metrics
Breakdown by View Type
Article Usage
Total Article Views: 52372
(from publication date up to now)
Breakdown by View Type
HTML Page Views: 44107
Abstract Page Views: 3004
PDF Downloads: 3770
Citation/Reference Downloads: 57
XML Downloads: 1434
Web Metrics
Days since publication: 3909
Overall contacts: 52372
Avg. contacts per week: 93.78
Article Citations
Article citations are based on data periodically collected from the Clarivate Web of Science web site
(last update: Mar 2025)
Total number of cites (since 2015): 19
Average cites per year: 1.73
Publication Metrics
by Dimensions ©
Articles citing this article
List of the papers citing this article based on CrossRef Cited-by.
Related Contents
iForest Similar Articles
Research Articles
Heat treatment of poplar plywood: modifications in physical, mechanical and durability properties
vol. 16, pp. 1-9 (online: 09 January 2023)
Research Articles
Hardness and contact angle of thermo-treated poplar plywood for bio-building
vol. 14, pp. 274-277 (online: 29 May 2021)
Research Articles
Physical and mechanical characteristics of poor-quality wood after heat treatment
vol. 8, pp. 884-891 (online: 22 May 2015)
Research Articles
Improving dimensional stability of Populus cathayana wood by suberin monomers with heat treatment
vol. 14, pp. 313-319 (online: 01 July 2021)
Research Articles
Kinetic analysis of poplar wood properties by thermal modification in conventional oven
vol. 11, pp. 131-139 (online: 07 February 2018)
Research Articles
Physical, chemical and mechanical properties of Pinus sylvestris wood at five sites in Portugal
vol. 10, pp. 669-679 (online: 11 July 2017)
Short Communications
Changes in Populus sp. wood subjected to heat treatment: anatomy and silica content
vol. 18, pp. 223-226 (online: 09 August 2025)
Short Communications
Influence of thermo-vacuum treatment on bending properties of poplar rotary-cut veneer
vol. 10, pp. 161-163 (online: 13 June 2016)
Research Articles
Mechanical and physical properties of Cunninghamia lanceolata wood decayed by brown rot
vol. 12, pp. 317-322 (online: 06 June 2019)
Research Articles
Thermo-modified native black poplar (Populus nigra L.) wood as an insulation material
vol. 14, pp. 268-273 (online: 29 May 2021)
iForest Database Search
Search By Author
Search By Keyword
Google Scholar Search
Citing Articles
Search By Author
Search By Keywords
PubMed Search
Search By Author
Search By Keyword