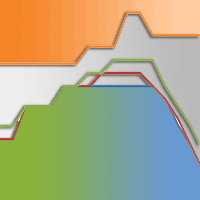
Thermo-modified native black poplar (Populus nigra L.) wood as an insulation material
iForest - Biogeosciences and Forestry, Volume 14, Issue 3, Pages 268-273 (2021)
doi: https://doi.org/10.3832/ifor3710-014
Published: May 29, 2021 - Copyright © 2021 SISEF
Research Articles
Collection/Special Issue: Research Project PRIN-MIUR 2015
The forest-wood value chain: biomass supply, traceability, C-footprint. Innovation for bioarchitecture and energy efficiency
Guest Editors: Scarascia Mugnozza G, Maesano M, Romagnoli M
Abstract
Extensive research projects have been carried out on thermal modification of wood material, yet thermal properties of thermally modified poplar wood have not been comprehensively investigated. Black poplar (Populus nigra L.) is a Eurasian species native to Italy which is rarely used for the production of high-performance products, though it is one of the least expensive hardwoods on the market. To explore alternative applications of poplar wood such as building facade or fire resistance materials, reliable data of thermal behaviour of thermally modified wood at high temperatures are needed. In this work, the thermal behaviour of native black poplar wood after thermal modification at different temperatures (180 °C, 200 °C and 220 °C) was analyzed. Thermal conductivity, thermal diffusivity and porosity were measured on poplar wood boards, as well as mass loss and wood color changes after heat treatment were quantified. Thermal conductivity of wood samples showed significant changes after treatment at 200 and 220 °C, but not at 180 °C. Wood porosity showed significant differences with the control when the samples were modified at a temperature of 220 °C. Increasing color differences were observed in wood samples by increasing the thermal modification temperature. Also, the mass loss of wood samples increased and equilibrium moisture content significantly dropped down after thermal modification. Our results showed that the use of thermally-modified black poplar wood could be considered as a viable alternative to chemically treated wood products for specific applications where high insulation is needed, such as saunas or windows, and for façades elements.
Keywords
Thermal Modification, Poplar, Insulation, Thermal Properties
Introduction
The Italian strategy for the forestry sector ([24]) reports Italy as one of the major importers of hardwood and softwood lumber in Europe, and calls for a more sustainable and competitive use of native species by the Italian wood industry. Poplar is the only species grown through dedicated forestry management practices in Italy. Poplar plantations account for only 1% of the total forest area, though it represents 50% of domestic wood production used in industrial wood processing. This makes poplar one of the most promising wood resources in the next future. Despite the cultivated area, Italian native poplar is currently used only for niche products; however, investigations are ongoing to develop new applications with higher quality and market value. Indeed, the main drawback of poplar wood is its durability, which is lower compared to the dominant commercial hardwood species, such as Chestnut and European oak, and this has hampered its industrial transformation in high performance products.
Current research efforts aimed at adding values to final poplar wood products are focused on processing techniques and wood modification processes. Among these, thermal modification of wood provide broadly recognized benefits, such as improved dimensional stability, uniform coloration and higher biological resistance. However, the lack of technical standards for the material properties and technological processes still represent a bottleneck to this aim, as limited knowledge is currently available on the defects of thermally modified wood, such as reduced mechanical properties, elevated internal tensions, checking and splitting ([41]).
Black poplar (Populus nigra L.) is a fast-growing, deciduous tree species belonging to Salicaceae family ([28]) which can be found in floodplain forests ([8]) throughout Europe, northern Africa, central and western Asia (Fig. S1 in Supplementary material). Its wood has many technological qualities; although not particularly strong, poplar wood is relatively fire-resistant and shockproof, and has a soft, fine texture. Traditionally, it was used for clogs, carts, furniture and also flooring near to open fireplaces ([7]). Nowadays, it is used for pulp and paper, and its fast growth rate makes it a suitable bioenergy crop ([15]). Moreover, poplar extracts have antioxidant and anti-inflammatory effects ([17], [40]).
The establishment of multipurpose tree plantations is currently increasing throughout Europe, due to the increasing demand for natural products, ecosystem services and sustainability issues. Consequently, there is a strong interest in physical, mechanical and chemical characterization of modified wood and its by-products, aimed to generate diversified, innovative and renewable products using on site bio-resources such as wood.
Heat treatment of wood is an economically competitive process that has its stable market position in Europe due to its low environmental impact and technical advantages in extending wood products lifetime ([9]). In the last decade, technical advantages and disadvantages of thermal wood modification (TMT) have been widely investigated. According to Ferrari et al. ([13]), this process involves treating wood at high temperature up to 260 °C in oxygen-free environment to avoid combustion. Thermal modification is nowadays widely employed to increase the durability of wood or to modify the physical, mechanical, or aesthetic properties of sawn timber, veneer or particles used in the production of wood composites. The main drawback of this process is the reduction of mechanical performances of thermally modified wood. Thermal modification is, therefore, often proposed as a means for valorizing wood of species with low natural durability ([4]) or for new applications of timber and related materials which have few market outlets ([39], [33]). Recently, Sandberg et al. ([34]), reviewed the available methods for improving wood technological properties of several tree species. Rousset et al. ([30]) determined the mass transfer properties in the hygroscopic range before and after 200 °C treatment in wood samples from Populus × canadensis cv. robusta to define the usage of thermally modified products in the packaging sector, due to the influence of mass transfer properties on the gas and water vapour transfer capabilities. Goli et al. ([14]) investigated the effect of heat treatment on some physical and mechanical properties of poplar wood (Populus alba L.). The initial condition of the treated material (wet or dry) and the dry mass loss (7 to 10%) caused very different effects on the Modulus of Elasticity (MOE), as heat treatments applied on wet wood material resulted in a lower reduction of MOE when compared to the same treatments applied on oven-dry material. Kozakiewicz et al. ([20]) studied the effects of thermal process conditions on the chemical composition and mechanical properties of black poplar wood, finding that its surface properties were significantly altered by heat, thus affecting the technological applications of wood. Salca & Hiziroglu ([31]) reported that heat modification has a negative effect on the hardness characteristics of different wood species (including yellow poplar), while their surface quality improved. Chu et al. ([6]) studied the surface characteristics of poplar wood subjected to high temperature and concluded that the wettability of treated wood decreased, while the surface brittleness increased after treatment. Korkut et al. ([19]) found that wood thermal modification improves the dimensional stability and some other important wood properties such as thermal conductivity. Changes caused by heat modification on thermal conductivity and density of Pannonian poplar (Populus × euramericana cv. Pannónia) and spruce (Picea abies Karst.) were assessed by Sandak et al. ([33]). The authors found that the variation of the thermal conductivity was greater than the variation of density in both wood species. Using the same temperature treatment (180 °C), Pásztory et al. ([26]) reported of a reduction in both density and thermal conductivity of wood which was dependent on treatment duration. The influence of the duration of heat modifications on thermal conductivity properties of rubber wood was also investigated by Srivaro et al. ([36]). The thermal conductivity of rubber wood samples after long heating treatment resulted similar to typical insulation materials, such as fiberglass, rockwool and extruded polystyrene.
The objective of this study was to analyze the effect of different heat modification temperatures (180, 200 and 220 °C) on thermal, physical and mechanical properties (mass loss, color changes, and MOE) of native black poplar wood.
Materials and methods
Boards of black poplar wood (size: 200 × 20 × 3 cm, width × length × thickness) from 8 different trees grown in the high forest of Calvello (Basilicata Region, Southern Italy) were randomly selected. Each board was cut in plain-sawn.
Thermo vacuum modification
A thermal modification process in a press-vacuum plant developed by WDE Maspell s.r.l. (Terni, Italy) has been adopted. Black poplar wood boards were subjected to thermal modification at 180 °C, 200 °C and 220 °C for 3 hours at the Laboratory of Wood Technology, University of Basilicata, Italy. Boards were firstly dried for 4 h in vacuum conditions (185-200 mbar) at a temperature of 90 °C (Fig. 1). The thermal process was applied on the dried samples by gradually increase the temperature to the final temperature in about 15 h. More details regarding the Thermo-Vacuum process and its technical parameters are reported by Allegretti et al. ([1]) and Sandak et al. ([32]).
Fig. 1 - Thermal modification parameters used during the heat treatment of black poplar wood samples.
Thermal conductivity and thermal diffusivity
From the mentioned thermally modified boards, a total of 24 samples without defects (6 for each of the 3 thermal treatments, and 6 for control) were randomly selected and then cut to obtain specimens of size 17 × 17 × 2 cm (w × l × t - Fig. 2). A series of 3 measurements were performed on each of the 24 specimens for a total of 72 measurements. Thermal conductivity and diffusivity of specimens have been measured at 25 °C in the radial direction using a thermal properties analyzer ISOMET 2104 (Applied Precision Ltd., Bratislava, Slovakia - Fig. 2). The evaluation was based on the analysis of the temperature response of the analyzed material to heat flow impulses ([3]).
Fig. 2 - Set up of the measurement of thermal properties in three different points on each wood surface.
Colour variation and mass loss
Wood color modifications after heat treatment were recorded by measuring the three coordinates L*, a* and b*, according to the CIELAB system. The L* coordinate is the lightness, ranging from 0 (black) to 100 (white); a* refers to the position of specimens in the color space between red/magenta (positive values) and green (negative values); b* indicates the specimen position in the color space between yellow (positive values) and blue (negative values). A Minolta CM-2002 Spectrophotometer (Minolta Corp., Osaka, Japan) was used with a pulsed Xenon arc light source. The total color variation was determined as follows (eqn. 1):
The color measurements have been determined on a total of 16 boards, 4 for each of the thermal modification processes, and 4 for control. In particular, for each boards, 3 measurement areas with a diameter of 8 mm were assessed, for a total of 48 measurement areas. Their average value was then calculated and statistically analysed.
Mass loss (ML) after heat treatment was evaluated with 3 measurements on each of 12 boards, 3 for each of the thermal modification processes, and 3 for control, according to the formula (eqn. 2):
where mpreTMT is the initial oven-dried mass of wood sample and mpostTMT is the oven-dried mass of the same sample after thermal modification.
Porosity and moisture content
An Ultrapyc® 1200e pycnometer (Quantachrome Instruments Corp., Boynton Beach, FL, USA) was used to measure the porosity on 12 specimens, 3 for each of the heat treatments, and 3 for control, with dimensions of 2 × 2 × 1 cm (w × l × t), in terms of percentage of pore space within the sample. The moisture content (%) was calculated as the difference between the weight of the specimens after drying at 105 °C for 24 hours and the weight recorded at environmental conditions (T = 20 °C, RH = 50%. Density was also evaluated at environmental conditions on the same 12 non-standard wood specimens.
Modulus of elasticity
The modulus of elasticity (MOE, N mm-2 - also known as Young’s Modulus) was calculated for 72 boards equally distributed between modified and unmodified material. For each board 4 measurements of MOE were taken, for a total of 288 recorded values. MOE measures the stiffness of a material based on the relationship between stress (force per unit area) and strain (proportional deformation). The stress is proportional to strain within the elastic limit of the material according to Hooke’s law. The dynamic MOE was calculated by the Christoffel’s equation (eqn. 3):
where ρ is the density of the specimen at a given moisture content (kg m-3), and V is the velocity of sound propagation (m s-1). The MOE was measured using a Microsecond Timer (Fakopp Enterprise, Agfalva, Hungary), with a resonance frequency of 23 kHz. This device measures the stress wave velocity of wood samples in the fiber direction through a transducer pin placed at a distance of 1 m with an angle of 45°. The signal was generated by a hammer tap on the start sensor and the device measures the propagation time. By knowing the distance between the two sensors, the wave velocity was calculated. Each measurement lasted less than 1 minute with a time measurement error of ± 3 microseconds.
Statistical analysis
Differences between untreated and thermo-modified poplar wood samples in terms of thermal properties, color variation, mass loss, modulus of elasticity were tested by Analysis of variance (ANOVA) and the related Duncan’s mean separation test ([10]) using the software Excel 2007® (Microsoft, Redmond, WA, USA).
Results and discussion
Thermal and physical properties
Tab. 1 - Mean values ± standard deviation of thermal properties of black poplar wood subjected to different heat treatment. Different letters in columns indicate significant (p<0.05) differences between means after Duncan test.
Treatment | Thermal conductivity (W m-1 K-1) |
Volumetric heat capacity (×106 J m-3 K-1) |
Thermal diffusivity (×10-6 m2 s-1) |
---|---|---|---|
220 °C | 0.100 ± 0.008 a | 0.530 ± 0.052 a | 0.189 ± 0.006 a |
200 °C | 0.111 ± 0.007 b | 0.593 ± 0.044 b | 0.188 ± 0.009 a |
180 °C | 0.118 ± 0.004 bc | 0.682 ± 0.034 c | 0.173 ± 0.006 b |
Control | 0.124 ± 0.004 c | 0.723 ± 0.033 d | 0.172 ± 0.004 b |
The measurement probe was located in three different points of the larger face of each specimen. The average value and the standard deviation for each material was then calculated (Tab. 1). Based on the results, the thermal conductivity decreases with the heat temperature, while the thermal diffusivity has an opposite trend. Previous studies showed that the thermal conductivity values decrease as the temperature increases, and the rate of decrease strongly depends on the temperature of the thermal modification ([18], [25], [26]). This implies that, in terms of insulation, thermo-modified wood would perform better than unmodified wood. The thermal wood properties are linked to the coefficient α, which represents the ratio between the coefficient of thermal conductivity (K) and the product of specific heat capacity (c) and density (ρ - eqn. 4):
where ρ multiplied by c represents the volumetric heat capacity. The coefficient α could be used for testing the efficiency of the wood heating process for industrial purposes ([29]). It reflects how long the heating or cooling process will take under a given supply. The thermal diffusivity, which is the component of the thermal conductivity equation, provides a measure of the heat transfer, i.e., the velocity of heat propagation in the wooden material. The lower its value, the longer the heat takes to pass through the material. Thus, the effectiveness of the insulation of a material depends on the thermal conductivity value as well as on the heat transfer velocity ([38]).
Tab. 2 reports the results of the physical properties of each set of specimens. The wood porosity dramatically drops when the temperature increases from 200 to 220 °C. However, this trend is in contrast with the thermal conductivity trend. Indeed, the reduction in porosity for poplar wood modified at 220 °C would predict an increase in density and thermal conductivity, which is in contrast with the results obtained. This could be due to changes in the wood chemical composition after thermal modification that could causes a degradation of the cell wall ([23], [22]). However, the effect of moisture content within the wood on its thermal conductivity could be more prominent than porosity. As reported by Zhou et al. ([42]), the conductivity increased almost linearly with moisture content at a given temperature, which is explained by the conduction properties of the water.
Tab. 2 - Mean values ± standard deviation of density, porosity and moisture content. Different letters in columns indicate significant (p<0.05) differences between means after Duncan test.
Treatment | Density (kg m-3) |
Porosity (%) |
Moisture content (%) |
---|---|---|---|
220 °C | 401.5 ± 11.8 a | 53.3 ± 0.4 a | 5.0 ± 0.5 a |
200 °C | 407.6 ± 19.9 b | 59.1 ± 1.7 b | 5.2 ± 0.5 a |
180 °C | 406.8 ± 9.2 b | 59.1 ± 1.8 b | 7.3 ± 0.6 b |
Control | 441.3 ± 10.0 c | 61.3 ± 1.4 b | 9.9 ± 0.9 c |
Color variation and mass loss
Wood color variation represents one of the most significant changes associated with thermal modification (Fig. 3). Wood darkens under the influence of heat ([35]). According to Patzelt et al. ([27]), color changes are strongly correlated with mass loss, while Bekhta & Niemz ([2]) stated that color variations could be used to predict the mechanical alterations of modified wood. Sundqvist ([37]) reported that an increase in temperature during modification produces a decrease in lightness. Tab. 3 shows a dramatic variation of L* in black poplar wood after thermal modification at 220 °C, reaching a very low value (L* = 42.14 ± 3.09) as compared to control sample (L* = 72.36 ± 1.84). The a* value increased significantly after thermal modification in all cases, while black poplar wood modified at a temperature of 180 °C showed a higher b* value (27.17 ± 2.88) compared to unmodified specimens (22.01 ± 0.73), thermally modified specimens heated at 200 °C (21.84 ± 1.84) and those heated at 220 °C (19.91 ± 3.71). Thus, thermal modification caused an extensive darkening of wood (strong reduction of L*), a reddening (increase of a* value) and a weakly yellowing (increase of b* value).
Fig. 3 - Example of color variation in poplar wood samples after thermal modification. (CTRL): unmodified (control); (180, 200, 220): thermally modified samples at 180.200, and 220 °C,respectively.
Tab. 3 - Mean values ± standard deviation of color coordinates in poplar wood. Different letters indicate significant (p<0.05) differences between means after Duncan test.
Treatment | L* | a* | b* |
---|---|---|---|
220 °C | 42.14 ± 3.09 a | 7.91 ± 1.58 a | 19.91 ± 3.71 a |
200 °C | 46.76 ± 2.91 b | 8.05 ± 0.49 a | 21.84 ± 1.84 b |
180 °C | 57.94 ± 5.41 c | 7.42 ± 1.04 a | 27.17 ± 2.88 c |
Control | 72.36 ± 1.84 d | 2.95 ± 0.43 b | 22.01 ± 0.73 b |
Black poplar wood after heat treatment showed a mass loss of 4.4%, 7.8% and 9.6% at 180, 200 and 220 °C, respectively, compared with control wood. This confirms previous evidences on mass loss after heat treatment due to changes in chemical composition of wood, which are strongly dependent on temperature ([11]). Moreover, we found that color difference increased as heating temperature increased: mean ΔE* value was 15.8, 24.6 and 33.1 for treatments at 180, 200, and 220 °C, respectively (Tab. 4).
Tab. 4 - Mean values ± standard deviation of mass loss and color parameters variation. Different letters in columns indicate significant (p<0.05) differences between means after Duncan test.
Treatment | Mass loss | ΔL* | Δa* | Δb* | ΔE* |
---|---|---|---|---|---|
220 °C | 9.67 ± 0.57 a | 32.09 ± 7.08 a | -5.34 ± 1.92 a | 1.27 ± 5.63 a | 33.07 ± 6.97 a |
200 °C | 7.88 ± 0.77 a | 23.80 ± 2.36 b | -5.19 ± 0.60 b | 0.55 ± 3.34 b | 24.55 ± 2.54 b |
180 °C | 4.40 ± 0.20 b | 14.38 ± 3.64 c | -4.01 ± 1.50 a | -4.69 ± 2.96 b | 15.76 ± 4.51 c |
Control | - | - | - | - | - |
Modulus of elasticity
The modulus of elasticity (MOE) of poplar wood specimens was significantly higher for wood samples modified at 180 °C than for those heated at 220 °C. Compared to control (10.392 N mm-2), MOE increased to 11.509 N mm-2 at 180 °C and then decreased to 9.778 N mm-2 at 220 °C. Based on these results, MOE seems to increase after milder heat modification of wood, while it decreases with strong modification temperatures (Tab. 5). Hill ([16]) reported a slight increase in MOE when the wood is thermally modified for a short period time. Kubojima et al. ([21]) reported an increase of the MOE of Picea sitchensis Carr. in the first 2 hours of treatment, followed by a constant value for wood treated at 120 °C and 160 °C. However, the reduction in wood strength after thermal modification is explained mainly by the degradation of wood structural components such as hemicelluloses, cellulose and lignin. Fengel & Wegener ([12]) showed the degradation of hemicelluloses at low temperature because of their low molecular weight. Burmester ([5]) reports that the thermal modification of wood results in a strong reduction of the hemicellulose content. Thus, high temperature treatments promote chemical changes in the wood material which becomes more fragile, due to the decomposition of polymers which consequently leads to a decrease in elasticity.
Tab. 5 - Mean values ± standard deviation of Modulus of elasticity (MOE). Different letters indicate significant differences (p<0.05) between means after Duncan test.
Treatment | MOE (N mm-2) |
---|---|
220 °C | 9.778.8 ± 379.3 a |
200 °C | 10.268.2 ± 2562.4 ab |
180 °C | 11.509.9 ± 1633.7 b |
Control | 10.392.6 ± 703.7 ab |
Conclusions
Thermal modification processes at different temperatures have been applied to native black poplar wood with the aim of assessing their influence on some important properties of wood for non-structural applications. One of the main concerns of wood thermal modification is the decrease in mechanical strength; therefore, thermally modified wood cannot be used for structural applications so far. According to our results, mean MOE values of sample wood slightly increased after heat treatment at 180 °C compared to control samples, though it substantially decreases when the temperature increased.
Black poplar wood showed an increase of mass loss with increasing heat modification temperature. The thermal modification treatment affects the chemical structure of wood and consequently its color. However the thermal modification had a considerable effect on the thermal conductivity of poplar wood samples, which decreased with increasing the treatment temperature.
Black poplar wood may have some potential in the future if thermally treated wood could be used in the structural application, also considering its interesting workability. The low thermal conductivity value, along with the low cost of production and processing, make this wood a promising material for the thermal insulation of the building envelope.
Acknowledgments
We thank Dr. D. Franco for taking part in the thermal analysis of the wood samples.
References
Gscholar
CrossRef | Gscholar
Gscholar
Gscholar
Gscholar
Gscholar
Gscholar
Gscholar
Gscholar
Gscholar
Authors’ Info
Authors’ Affiliation
Valentina Lo Giudice
Nicola Moretti 0000-0001-6897-8310
School of Agricultural, Forest, Food and Environmental Science (SAFE) -University of Basilicata, Potenza (Italy)
Pietro Stefanizzi 0000-0001-7506-5202
Department of Civil Engineering Sciences and Architecture - Polytechnic University of Bari, Bari (Italy)
Department of Agro-Environmental Sciences - University of Bari (Italy)
Corresponding author
Paper Info
Citation
Todaro L, Liuzzi S, Pantaleo AM, Lo Giudice V, Moretti N, Stefanizzi P (2021). Thermo-modified native black poplar (Populus nigra L.) wood as an insulation material. iForest 14: 268-273. - doi: 10.3832/ifor3710-014
Academic Editor
Giacomo Goli
Paper history
Received: Nov 30, 2020
Accepted: Apr 08, 2021
First online: May 29, 2021
Publication Date: Jun 30, 2021
Publication Time: 1.70 months
Copyright Information
© SISEF - The Italian Society of Silviculture and Forest Ecology 2021
Open Access
This article is distributed under the terms of the Creative Commons Attribution-Non Commercial 4.0 International (https://creativecommons.org/licenses/by-nc/4.0/), which permits unrestricted use, distribution, and reproduction in any medium, provided you give appropriate credit to the original author(s) and the source, provide a link to the Creative Commons license, and indicate if changes were made.
Web Metrics
Breakdown by View Type
Article Usage
Total Article Views: 33751
(from publication date up to now)
Breakdown by View Type
HTML Page Views: 28937
Abstract Page Views: 2197
PDF Downloads: 2057
Citation/Reference Downloads: 2
XML Downloads: 558
Web Metrics
Days since publication: 1544
Overall contacts: 33751
Avg. contacts per week: 153.02
Article Citations
Article citations are based on data periodically collected from the Clarivate Web of Science web site
(last update: Mar 2025)
Total number of cites (since 2021): 10
Average cites per year: 2.00
Publication Metrics
by Dimensions ©
Articles citing this article
List of the papers citing this article based on CrossRef Cited-by.
Related Contents
iForest Similar Articles
Research Articles
Kinetic analysis of poplar wood properties by thermal modification in conventional oven
vol. 11, pp. 131-139 (online: 07 February 2018)
Research Articles
The physicomechanical and thermal properties of Algerian Aleppo pine (Pinus halepensis) wood as a component of sandwich panels
vol. 15, pp. 106-111 (online: 21 March 2022)
Research Articles
Reversible and irreversible effects of mild thermal treatment on the properties of wood used for making musical instruments: comparing mulberry to spruce
vol. 15, pp. 256-264 (online: 20 July 2022)
Short Communications
Influence of thermo-vacuum treatment on bending properties of poplar rotary-cut veneer
vol. 10, pp. 161-163 (online: 13 June 2016)
Research Articles
Hardness and contact angle of thermo-treated poplar plywood for bio-building
vol. 14, pp. 274-277 (online: 29 May 2021)
Research Articles
Examining the evolution and convergence of wood modification and environmental impact assessment in research
vol. 10, pp. 879-885 (online: 06 November 2017)
Research Articles
Improving dimensional stability of Populus cathayana wood by suberin monomers with heat treatment
vol. 14, pp. 313-319 (online: 01 July 2021)
Review Papers
Wood modification technologies - a review
vol. 10, pp. 895-908 (online: 01 December 2017)
Technical Advances
Thermal canopy photography in forestry - an alternative to optical cover photography
vol. 8, pp. 1-5 (online: 07 May 2014)
Research Articles
Heat treatment of poplar plywood: modifications in physical, mechanical and durability properties
vol. 16, pp. 1-9 (online: 09 January 2023)
iForest Database Search
Search By Author
Search By Keyword
Google Scholar Search
Citing Articles
Search By Author
Search By Keywords
PubMed Search
Search By Author
Search By Keyword