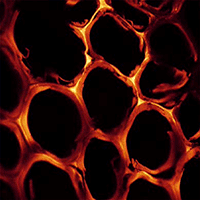
Wood modification technologies - a review
iForest - Biogeosciences and Forestry, Volume 10, Issue 6, Pages 895-908 (2017)
doi: https://doi.org/10.3832/ifor2380-010
Published: Dec 01, 2017 - Copyright © 2017 SISEF
Review Papers
Collection/Special Issue: COST action FP1407
Understanding wood modification through an integrated scientific and environmental impact approach
Guest Editors: Giacomo Goli, Andreja Kutnar, Dennis Jones, Dick Sandberg
Abstract
The market for new durable products of modified wood has increased substantially during the last few years, especially in Europe. This increased interest depends partly on the restricted use of toxic preservatives due to increased environmental concern, as well as the need for reduced maintenance for wood products that are mainly for exterior use. Furthermore, as sustainability becomes a greater concern, the environmental impact of construction and interior materials should be included in planning by considering the entire life cycle and embodied energy of the materials used. As a result, wood modification has been implemented to improve the intrinsic properties of wood, widen the range of sawn timber applications, and acquire the form and functionality desired by engineers, without bringing environmental friendliness into question. The different wood modification processes are at various stages of development, and the challenges that must be overcome to expand to industrial applications differ amongst them. In this paper, three groups of wood modification processes are discussed and exemplified with modified wood products that have been newly introduced to the market: (i) chemical processing (acetylation, furfurylation, resin impregnation etc.); (ii) thermo-hydro processing (thermal treatment); and (iii) thermo-hydro-mechanical processing (surface densification). Building on these examples, the paper will discuss the environmental impact assessment of modification processes and further development needs.
Keywords
Chemical Treatments, Thermo-hydro-mechanical, LCA, Acetylation, Furfurylation, Resin Impregnation, Environmental Impacts, Densification
Introduction
As a natural renewable resource, wood is in general a non-toxic, easily accessible and inexpensive biomass-derived material. Since ancient times, wood has been used by mankind based on its inherent properties, meaning that a particular species or part of the tree was utilised to achieve the best performance. Aside from drying, modification of sawn timber has been rare from a historical perspective. Nevertheless, as wood is a natural product that originates from different individual trees, limits are imposed on its use, and the material needs to be transformed to acquire the desired functionality. Modification is applied to overcome weak points of the wood material that are mainly related to moisture sensitiveness, low dimensional stability, hardness and wear resistance, low resistance to bio-deterioration against fungi, termites, marine borers, and low resistance to UV irradiation.
Nowadays, wood modification is referred to as a process used to improve the physical, mechanical, or aesthetic properties of sawn timber, veneer or wood particles used in the production of wood composites. This process produces a material that can be disposed at the end of a product’s life cycle without presenting any environmental hazards greater than those that are associated with the disposal of unmodified wood.
The wood modification industry is currently undergoing major developments, driven in part by environmental concerns regarding the use of wood treated with certain classes of preservatives. Several “new” technologies, such as thermal modification, acetylation, furfurylation, and different impregnation processes, have been successfully introduced in the market and demonstrate the potential of these modern technologies.
The main reasons for the increased interest during the last decades in wood modification with regard to research, the industry, and society in general can be summarised as:
- a change in wood properties as a result of changes in silvicultural practices and the way of using wood (e.g., in construction);
- awareness of the use of rare species with outstanding properties, such as durability and appearance;
- awareness and restrictions by law of using environmental non-friendly chemicals for increased durability and reduced maintenance of wood products;
- increased interest from the industry to add value to sawn timber and by-products, from the sawmill and refining processes;
- EU policies supporting the development of a sustainable society; and
- the international dimension on climate change and related activities mainly organised within the frame of the United Nations (UN), such as the Paris Agreement under the United Nations Framework Convention on Climate Change ([93]).
The purpose of this review is to present state-of-the-art wood modification processes recently introduced in European market with a specific focus on chemical processing (acetylation, furfurylation, impregnation modifications) and thermo-hydro and thermo-hydro-mechanical processing (thermal treatment, surface densification). Continuous surface densification is given as an example of a modification process that has been under development for a long time, but is now close to industrial application. The importance of integrating environmental impact assessments into the optimisation of industrial processes and the development of new modification processes is discussed. The dynamics of the research interest these modification treatments have received is presented with an overview of the number of publications published in the field during the period 1990-2016.
Wood modification in scientific publications
Scientific articles related to wood modification have been increasing over the past decade. Fig. 1a-b search amongst article titles, abstracts, and keywords in the Scopus® database of peer-reviewed literature using keywords related to thermal-based modification and chemical modification. While the increased number of articles indicate the development of wood modification in general, chemical modification of wood has been studied more frequently in recent years, showing nearly 50 times more articles than thermal-based modification. Furthermore, about half of the chemical modification articles are related to wood preservation.
Fig. 1 - Number of publications found in the Scopus® database of peer-reviewed articles 1990-2016 using keywords related to: (a) thermo-based modification methods; (b) chemical modification methods; and (c) “modified wood” and “LCA”, and “LCA” and “wood”.
This review of the Scopus® database shows that wood modification area is receiving an increased interest in the scientific community, much of which has been driven by environmental concerns and increased wood use in novel applications to replace fossil-based materials. However, it is important that environmental impact assessments, such as life cycle assessments (LCAs) of wood products, especially of modified wood, are included in the development of new treatments, wood-based materials, and products. Fig. 1c shows the number of articles using keywords related to modified wood and LCA. Increased involvement of LCA in research has been the consequence of standardised requirements and guidelines for LCA. In the entire search time frame, there were only 15 publications that included the keywords “modified wood” and “LCA”. To optimise modification processing and minimise environmental impacts, more information must be gathered about all process-related factors affecting the environment. This is also the aim of COST Action FP1407 “Understanding wood modification through an integrated scientific and environmental impact approach”, in which members from 26 European countries participating from March 2015 to April 2019. The initiative will facilitate the critical mass of Europe-wide knowledge needed to achieve future developments in the wood modification processing with the integration of process parameters assessments, developed product properties, and environmental impacts.
Wood modification
Wood modification is an all-encompassing term to describe the application of chemical, mechanical, physical, or biological methods to alter the properties of the material. Such a definition of wood modification includes almost everything that happens within the wood material after it has left the forest. Hill ([19]) has provided a well-accepted definition of wood modification: “Wood modification involves the action of a chemical, biological or physical agent upon the material, resulting in a desired property enhancement during the service life of the modified wood. The modified wood should itself be nontoxic under service conditions, and furthermore, there should be no release of any toxic substances during service, or at end of life, following disposal or recycling of the modified wood. If the modification is intended for improved resistance to biological attack, then the mode of action should be non-biocidal”. It should be noted that the above does not necessarily exclude the use of a hazardous chemical in the preparation of modified wood, provided that no hazardous residues remain once the wood modification process is complete.
To modify wood, four main types of processes can be implemented: (1) chemical treatments; (2) thermo-hydro (TH) and thermo-hydro-mechanical (THM) treatments; (3) treatments based on biological processes; and (4) physical treatment with the use of electromagnetic irradiation or plasma. In this review paper, only the two first processes will be discussed.
While chemical treatments are the most numerous type of processes, and the range of chemical agents is extremely broad, only heat and water are used during TH and THM treatments, albeit supplemented with mechanical forces in the latter case.
Principal mechanisms of wood modification
Modification of wood can involve active modifications, which result in a change of the chemical nature of the material, or a passive modification, in which a change in properties results without altering the chemistry of the material. Most active modification methods investigated to date have involved the chemical reaction of a reagent with cell-wall polymer hydroxyl groups. These hydroxyl groups play a key role in the wood-water interaction while simultaneously being the most reactive sites (Fig. 2). In moist wood, the water molecules settle between the wood polymers, forming hydrogen bonds between the hydroxyl groups and individual water molecules. A change in the number of these water molecules results in shrinkage and swelling of the wood. All possible types of wood treatments affect the wood-water interaction mechanism. The main wood-treatment interaction mechanisms that may be responsible for new wood properties are summarised in Fig. 2.
Fig. 2 - Schematic diagram illustrating the effect of chemical modification (courtesy: Emil Engelund Thybring, University of Copenhagen, Denmark).
Several wood-treatment interaction mechanisms tend to occur at the same time. In thermal modification, as one example, parts of the cell-wall polymers are altered, which may lead to cross-linking, reduction of OH-groups, and undesired cleavage of the polymer chains.
It should be noted that most of the wood modification processes that are developed or under experimentation have full or partial origins in the pioneering research and seminal work of Alfred J. Stamm and his colleagues at the Forest Products Laboratory in Madison, Wisconsin, during the 1940s and 1950s.
Chemical wood modification processes
Chemical modification of wood takes place when a chemical reaction of an agent occurs with the polymeric constituents of wood (lignin, hemicelluloses, or cellulose), thus resulting in the formation of a stable covalent bond between the reagent and the cell-wall polymers ([71]).
Consequently, chemical modification of wood is considered as an active modification because it results in a chemical change in the cell-wall polymers. Much is known about the modes of action of modified wood, which incorporates a combination of the following: (i) the equilibrium moisture content is lowered in modified wood, and it is harder for fungi to obtain the moisture required for decay; (ii) a physical blocking of the entrance of decay fungi from the micro pores of the cell walls; and/or (iii) inhibition of the action of specific enzymes ([19], [20], [73], [76]). To date, these are the three most important aspects of the entire mechanism that have been speculated.
Impregnation modification of wood is another type of modification. It implies that there is an impregnation of the cell wall of wood with a chemical, or a combination of chemicals, that reacts to form a material that is “locked” into the cell wall ([19]). It is a passive modification process, meaning that although the wood properties are affected, there is no alteration in the chemistry of the material. This type of wood modification includes either impregnation of the cell wall with a monomer, which is subsequently polymerised in situ, i.e., acts by bulking the cell wall, or the lumens being impregnated. While the latter does not affect the dimensional stability or durability, the impregnant molecules must be small enough to enter the cell wall in the former, i.e., the cell wall micropore diameter should be approximately 2-4 nm. The most important chemical processes of wood modification are discussed as follows.
Acetylation
In Germany, Fuchs ([13]) carried out the first experiment on wood acetylation using chemical agents like acetic anhydride and sulphuric acid as catalysts. Tarkow ([88]) was the first researcher who described the use of the acetylation process to stabilise wood from swelling in the water. Since the 1940s, many laboratories worldwide have executed studies on the acetylation of wood in a variety of ways by using several wood species ([71]). However, early attempts proposed by Koppers Inc. in 1961 to commercialise the process of wood acetylation in the USA failed due to the high production costs involved ([74], [76]). Innovative laboratory work to extend acetylation to the semi-industrial level was successfully performed at Stichting Hout Research in the Netherlands by Militz and his colleagues during the 1990s ([51], [5], [23]).
Wood acetylation using primarily acetic anhydride was first generated as a liquid phase reaction ([71]). This work was initiated using acetic anhydride catalysed by zinc chloride or pyridine. Since then, several other catalysts, including sodium acetate, potassium acid, urea-ammonium sulphate, have been tested both with liquid and vapour systems ([71], [19]). Most acetylation reactions today are realised without the use of a catalyst ([44], [76], [49]).
The reaction of acetic anhydride with wood polymers results in the esterification of accessible hydroxyl groups in the cell wall with the formation of a by-product, acetic acid (Fig. 3). This by-product is mostly removed from the modified wood, as the human nose is quite sensitive to the odour of acetic acid. Like untreated wood, acetylated wood is comprised only of carbon, hydrogen, and oxygen, and contains no toxic constituents ([19]). Furthermore, acetylation of wood is a single-addition chemical reaction ([71]), which means that one acetyl group reacts with one hydroxyl group without any polymerisation (Fig. 3).
Many scientists today believe that wood acetylation reduces the number of hydroxyl groups (-OH) that can absorb moisture by hydrogen bonding to largely reduce the equilibrium moisture content and fibre saturation point. Hence, the dimensional stabilisation of wood improves with increasing weight gain, due to acetylation reaction ([72], [73], [44], [76]). Other scientists favour another mechanism: by modifying wood with acetic anhydride, it is observed that the dimensional stabilisation is closely related to the weight percentage gain (WPG) or bulking of the cell wall. As a consequence, the extent of OH-substitution is rather irrelevant ([60], [19], [30], [61]).
As far as biological resistance is concerned, several theories have been proposed to explain the high resistance of acetylated wood to fungal attacks. One theory that has gained large acceptance, is that enzyme penetration is prevented by physically blocking the cell-wall micropores ([60], [19], [20]). In agreement with the above, Highley et al. ([18]) showed that the smallest enzyme of a brown-rot fungus is too large to penetrate the cell wall of wood.
On the contrary, Rowell has postulated that the mechanism of decay resistance in acetylated wood is based on “moisture exclusion”, the equilibrium moisture content of a highly modified wood is too low to support fungal attacks, i.e., there are not enough water molecules at the site of a glycosidic bond, which the fungal enzymes need for hydrolysis ([71], [73]). In a recent review by Rowell ([75]), supported the idea that in the case of a brown-rot fungal attack, the reduced moisture of acetylated wood prevents the fungus from initiating the breakdown of the hemicelluloses as an energy source.
In his doctorate work, Mohebby & Militz ([54]) speculated a third possible mechanism: some minuscule regions in the cell wall are not acetylated, due to the size of the acetate group itself. As a result, these regions are accessible to the free radicals generated by the fungi. In another review, Hill ([20]) concluded that the substrate recognition effects were unlikely to be of importance, given the inherent lack of enzyme accessibility. Therefore, the reduced cell-wall water content was considered to be the most likely mechanism for the high biological resistance of acetylated wood.
However, recent research works ([3], [70]) have demonstrated that the mechanism of substrate recognition by the fungus should be considered as critical, in combination with the lowered moisture content as distributed within the wood matrix.
Nowadays, the company Accsys Technologies in Arnhem (The Netherlands) industrially produces acetylated wood. This wood material is marketed under the commercial name Accoya®; the radiata pine (Pinus radiata) and alder (Alnus spp.) species are currently utilised. On average, Accoya wood attains an acetyl weight gain of approximately 20%. About 40.000 m3 acetylated wood was produced by the company Accsys in the year 2016, and the company plans to raise its present capacity to ca. 60.000 m3 in 2018 ([49]). The main uses of Accoya wood include: exterior windows and doors, decking, cladding, and other civil construction applications ([76]).
The acetylation process currently applied by Accsys Technologies yields chemically modified timber, which has largely improved physical, mechanical, and biological material properties ([19], [30], [73], [44], [2], [14], [76]), which are discussed as follows:
- The biological durability of wood has been improved to the highest durability class (Class 1), similar to the extremely durable tropical species teak (Tectona grandis) and ipé (Handroanthus spp.). Acetylated wood material exhibits a considerably increased biological resistance ([43], [60], [54], [74], [44]).
- Acetylated wood has a fibre saturation point below 15%, and the cell wall attains a high moisture exclusion efficiency ([19]). Consequently, the swelling and shrinkage properties are reduced by 70-80%, as compared to untreated wood ([30], [74]). The reason for that is simply because the cell wall is filled with chemically bonded acetyl groups, which utilise space within the cell wall ([19]) denying space to water molecules.
- Acetylated wood has been proven to be exceptionally resistant to subterranean and Formosan termites ([2]).
- At treatment levels >20% (acetyl content), Accoya wood has been found to possess excellent resistance to marine borer attacks even after 16 years of field exposure in the same or better order than CCA treated pine wood ([99]).
- Acetylated wood can become 15-30% harder than untreated wood ([74]).
- Acetylation technology has negligible impacts on the mechanical (strength) properties of wood material ([74], [44]).
- Acetylated wood is marketed today as a “green” product with several environmental benefits ([30], [42], [95]). According to Van Der Lugt et al. ([95]), acetylated wood demonstrates a much lower carbon footprint than steel, concrete, and unsustainably sourced azobé (Lophira alata). As a result, Accoya wood has showed CO2-negative life-cycle-analysis (LCA) results over an entire life cycle.
Due to the listed advantages of the material, Accoya wood has the potential to be widely used in certain applications. In Germany, Accoya wood, as a new wood material, has recently gained acceptance for use in exterior windows, by the German association of Windows and Facades (VFF). However, a limitation is that only radiata pine (Pinus radiata) and alder (Alnus spp.) are currently used in the process ([49]), and there is a need to widen the number of wood species that can be utilised.
Furfurylation
Research relating to chemical modification of wood with furfuryl alcohol (C5H6O2) was initiated by the renowned researchers A. Stamm and I. Goldstein ([17], [87]). By using cyclic carboxylic anhydrides as key catalysts, furfurylated wood with superior properties better than those produced with the early developed systems was achieved by Scheider ([80]) in Canada. Innovative research work was also carried out by Westin and his collegues ([98]) in Sweden, which led to a novel technology based on stable solutions with substantial impregnating capacities and promising properties, like resistance to decay.
Furfuryl alcohol is a liquid produced from agricultural wastes, such as sugar cane, and corn cobs. Furfurylation is executed by impregnating wood with a mixture of furfuryl alcohol and catalysts, and then heating it to cause polymerisation. The purpose of furfurylation is to improve resistance to biological degradation and dimensional stability by applying a non-toxic, proprietary, furfuryl alcohol polymer.
The polymerisation of furfuryl alcohol in wood is a complex chemical reaction. Even today, the question of whether furfurylation is a distinct chemical modification process remains unanswered. Some scientists believe that it comprises a chemical modification process, since the furfuryl alcohol polymer reacts with itself and possibly reacts with the lignin in the cell walls ([42], [59], [14], [45]). Thus, the furfuryl alcohol complexes are predominantly deposited in the wood cavities and cell walls (Fig. 4). Polymerisation takes place in microscopic cell cavities and is easily detected using optical microscopy. Recent nanoindentation studies have indicated that improvements in indentation modulus and hardness of furfurylated wood cells demonstrate indirectly, but strongly, that furfuryl alcohol penetrates wood cells during the modification process ([45]). Another perception is that furfurylation leads to a permanent “bulking” of the cell wall, meaning that the cells are swollen in a permanent way. One possible explanation is that the furfuryl alcohol polymer inside the cell wall occupies some of the space that is normally filled with water molecules when wood swell in humid conditions ([42]). Various scientists consider wood furfurylation as an impregnation modification process, in which the properties of the furfurylated material appear more like those of a polymer-filled cell wall rather than a reacted cell wall ([74], [44]).
Fig. 4 - Cross section of radiata pine wood with cell walls containing furan polymer (in reddish areas), image through fluorescence microscopy ([91]).
Nowadays, the industrial production of furfurylated wood is carried out by Kebony AS (formerly Wood Polymer Technologies) in Norway. According to Lande et al. ([41]), the industrial process of wood furfurylation is comprised of the following:
- Storage and mixing of chemicals: the treating solutions are mixed in a separate mixing tank where different chemicals (furfuryl alcohol, initiators/catalysts, buffering agents, surfactants, water) are added. The mixed solution is pumped to one of the buffer tanks.
- Impregnation: the wooden material, i.e., treatable softwoods or hardwoods, is vacuum pressure impregnated with the treating solution by a full-cell process with a vacuum step, a pressure step, and a short post-vacuum step.
- Reaction and curing: in-situ polymerisation of the chemicals and grafting reactions with the polymeric components of the wood occur during this step. The curing chamber is heated with a direct injection of steam, and the temperature achieved depends on the product use. The chamber is operated as a closed system during the curing period, except for a ventilation period at the end. The ventilation gas is cooled and the condensate is separated from the gas; thereafter, the condensate goes back to the condensate tank for re-use.
- Drying: final drying of the modified wood material in a kiln dryer is essential to minimise emissions and obtain a desirable final moisture content.
- Cleaning: the emissions during the process are managed by cleaning the ventilated gases.
According to the literature ([41], [42], [40], [74], [44], [48]), the furfurylation process results in a modified wood product that has distinctly improved properties, which are summarised as follows:
- The biological durability of wood is upgraded to “Class 1” ([14]). Decay resistance test results over a period of 9 years have showed that furfurylated wood of moderate loading (30-35% of weight percentage gain) has comparable resistance with that of pine wood impregnated with copper chromium arsenate ([44]).
- The mechanical properties of wood, except for impact resistance, are enhanced when wood is treated with a furfuryl-alcohol polymer. Furfurylated wood is characterised by greater hardness, elasticity, and rupture moduli as compared to untreated wood; however, it is also more brittle ([44]).
- Kebony wood, depending upon the loading, exhibits strong dimensional stability and resistance to weathering ([48]); moreover, its water swelling and shrinking values are over 50% lower than untreated wood.
- Furfurylated wood is extremely resistant to marine borers at high levels (>50%) of weight percentage gain ([99]).
- Recent studies regarding ecotoxicology of furfurylated wood and leachates from furfurylated wood showed no significant ecotoxicity, while its combustion did not release any volatile organic compounds or polyaromatic hydrocarbons above the normal levels of wood combustion ([64]).
- Furfurylated wood is a “green” wood product that holds an ecological label in the Scandinavian market, named “Swan”. Furfurylation of wood is, therefore, believed to be a safe process for the environment ([14]).
The company Kebony AS (Norway) currently produces two different furfurylated wood products:
- Kebony Clear®: furfurylated wood, highly-loaded, dark, hard; currently used for flooring. The wood species used are radiata pine, southern yellow pine and maple.
- Kebony Character®: furfurylated wood, more lightly-loaded; presently used as decking, siding, roofing and outdoor furniture. This is produced from Scots pine wood.
Nowadays, the company Kebony AS has an annual production of approximately 22.000 m3 (2016), and it is increasing its production capacity by building additional facilities in Belgium ([49]).
In addition, Kebony wood has been recently used in the production of exterior windows, like Accoya wood. Following a series of extensive quality tests in Germany, furfurylated wood is presently recommended by the German Association of Windows and Facades (VFF).
Modification with thermosetting resins
Historically, the first experiments on impregnation modification of wood using formaldehyde-based resins were carried out by A. Stamm and his colleagues at the Forest Products Laboratory in Madison, Wisconsin, during the 1940s. Their initial research work included impregnation of wood with phenol-formaldehyde resins with up to 100% resin addition, which resulted in an improved dimensional stability (anti-shrink efficiency, ASE, up to 58%) and improved resistance to biodeterioration against fungi, termites, and marine borers. Initial experiments using wood veneers by applying impregnation with phenol-formaldehyde (PF) resins, heat, and compression were implemented by Stamm & Seborg ([86]), leading to the production of products called Compreg® and Impreg®.
Compreg manufacturing is currently realised at a number of industrial sites in the USA, Pakistan, and India under different brand names. Compreg and related products (Fibron, Permali, Dymonwood, C-K Composites) have potent dimensional stability and high strength properties, like hardness, abrasion resistance, and compression strength ([19]). Products resulting from these impregnation treatments have been used in the manufacturing of knife and tool handles, and musical and electrical instruments, but not directly for preservation purposes ([14]). The volumes of these products are currently very low ([19]).
Research on the impregnation modification of wood with melamine-formaldehyde (MF) resins has increased in recent decades, especially in Europe, with positive results with respect to dimensional stability and biological resistance to brown-rot fungi ([26], [66], [68], [46], [16], [31], [83], [32]). Its main drawbacks are the high production costs and the tendency of such wood products to crack under humid-dry cycle conditions. None of these impregnation modification methods have yet to reach the full-scale level.
Modification with DMDHEU
This technology was transferred from the treatment of non-wood systems. Furthermore, it involves the impregnation of pine wood, a known highly porous species, with the reagent 1.3-dimethylol-4.5-dihydroxyethyleneurea (DMDHEU). This reagent (Fig. 5) was well-utilised in the textile industry until the 1980s, in an attempt to manufacture wrinkle-free fabrics. Wood modification with DMDHEU has been shown to improve dimensional stability and durability, and to slightly reduce the moisture uptake of wood ([58]).
Militz ([52]) was the first scientist to successfully report on the use of DMDHEU in treating wood, with very positive results. Militz tested beech wood treated with DMDHEU and demonstrated its effectiveness by using a variety of catalysts. It was finally found that temperatures of 100 oC were necessary for the effective curing of the resin system. Noticeably, the anti-shrink efficiency (ASE) value of DMDHEU-treated wood was found to be ca. 75%.
Since then, the process has undertaken considerable improvements by Militz and co-workers ([35]), from which commercial application has been finally achieved in Germany. This impregnation modification process is presently marketed by the German company BASF under the commercial name Belmadur®.
This technology is considered to be an innovative modification process under which pine wood, typically Scots pine, is impregnated under high pressure (12-14 atm) and polymerised by curing. The entire process is based on simple production stages. The first stage consists of penetrating the wood with a proprietary DMDHEU solution, an aqueous solution of a chemical agent ([52]). The air is removed from the cell structure by applying a vacuum to ensure that the agent can reach the innermost cells when the solution is applied under pressure. The next stage consists of drying impregnated wood at a slow rate at a temperature of 100-120 °C under humid conditions. This causes the agent molecules to cure by polycondensation, after which water is released ([35], [36]).
The modified product has highly reduced hygroscopic properties ([36], [62], [44]). ASE values of up to 70% can be achieved ([36]), but are normally in the range of 30-40% ([35]). The mechanisms of the reaction between DMDHEU and the cell wall polymers are still not clear ([19], [44]). It has been shown that the modification of wood with DMDHEU produces a bulking effect, while results from Dieste et al. ([12]) have indicated that DMDHEU reduces the pore size of the samples by occupying the void space present in the cell walls.
Belmadur wood production is still sparse in Germany. The producing German company, Münchinger, belongs to the BASF group; and to date, it is focusing on the German market. Key applications thus far have been decking and garden furniture. However, a laminated Belmadur product has gained acceptance by the German association of Windows and Facades (VFF) for use in exterior windows. The resistance of Belmadur wood to marine borers is substantial ([44]). However, the drawbacks are brittleness, tendency to crack, and high emissions of formaldehyde from the product. In addition, the present technical and market developments of Belmadur technology are not known.
The Indurite process
The “Indurite process” has been developed from a comprehensive survey of possible reactions of wood cell walls with polymer systems. The technology was scaled-up by the company Engineered Wood Solutions in New Zealand ([19]), after which it was obtained by the company Osmose. The original concept for Indurite was undertaken to upgrade home-grown radiata pine (Pinus radiata) by impregnation of wood with a water-soluble polysaccharide solution (soy and corn starch). The impregnated material is held in a covered area for a few hours, and then the curing step takes place in a temperature-controlled conventional kiln with the use of certain catalysts in the solution ([19]). A major advantage is that there is no need for significant equipment investments. This modified wood is claimed to be used presently in exterior applications such as cladding and decking. However, the present developments of this technology are not clear.
The KeyWood process
According to Larsson-Brelid ([44]), a new product named KeyWood®, which resembles furfurylated wood, was developed within the EU-funded project “Ecobinders”. The reactant, which contains small amounts of tri-hydroxy-methyl furan (THMF) and furfuryl alcohol, is more water soluble than furfuryl alcohol itself, and easily penetrates the cell wall. After curing the THMF-impregnated wood, the polymer formed within the cell wall resembles the polymer formed by the Kebony process. However, unlike furfurylated wood, no covalent bonds to the cell wall polymeric constituents (lignin, hemicelluloses, cellulose) were detected in the analytical studies within the “Ecobinders” project. Furthermore, due to the higher quantity of remaining hydroxyls in the polymer as well as the lack of bonds to the lignin, the KeyWood product has a higher equilibrium moisture contents than furfurylated wood at the same level of relative humidity. Furthermore, kiln drying temperatures of 125 °C are necessary for sufficient curing; consequently, this temperature causes problems with cracking and brittleness. While the technology was sold to the company Arch SA in 2009, the production volumes seem to be very small. Meanwhile, the present market developments of the KeyWood process are not clear and have not been disclosed publicly.
Modification processes using monomers
Vinyl monomer impregnation of wood, followed by in situ polymerisation, represents another promising way to enhance mechanical, dimensional, and thermal stability, as well as fungal and insect resistance to wood species of poor natural durability. Different commercially available vinyl monomers, such as acrylonitrile, glycidyl methacrylate, methyl methacrylate, hydroxyethylene methacrylate, ethylene glycol, dimethacrylate, butyl acrylate, butyl methacrylate, styrene, acrylamide or acrylonitrile, have been investigated by several scientists ([19], [74]).
According to the nature of the monomer used, polymerisation can take place either in the cell lumens, the cell wall, or both ([80]). Polymerisation can be initiated by different means using either thermal-free radical initiator, or gamma radiation. X-rays, derived from a high-energy, high current electron beam, can be also used to initiate in situ polymerisation of vinyl monomers. X-rays initiate polymerisation and penetrate through thick pieces of wood, allowing polymerisation of the monomers in the cell walls. Having entered the cell walls and then being polymerised within the cell walls, these radiation-cured treatments increased the dimensional stability of treated wood ([14]). Nevertheless, all the abovementioned techniques have not resulted in commercial applications to date.
Thermo-hydro and thermo-hydro-mechanical processes
One group of emerging wood treatments involves the combined use of temperature and moisture through which force can be applied: thermo-hydro (TH) and thermo-hydro-mechanical (THM) processes. In an orthodox definition, no additives are used in the processes beyond water in combination with wood, heat, and external forces to shape the wood. Procedures including impregnation or gluing to lock a shape are, however, usually included in these modification processes.
Human beings have demonstrably been using heat, moisture, and force for the modification of wood since ancient times; it can be assumed that they had long recognised the effects of fire and water on timber, utilising them for their own purposes ([55], [78]). The oldest evidence on THM processing is a heat-hardened tip of a more than 100.000-year-old Lehringen spear found in 1948, buried inside the skeleton of an elephant ([1]). Nevertheless, it was not until the 19th century that the use of water and heat in wood processing was industrialised. In 1849, the inventor of the Vienna Chair and the technology related to its production, Michael Thonét, started a workshop for the production of bent wood furniture. Thonét’s innovations were the first steps towards the industrialisation of a TH/THM process intended for mass production.
Fig. 6 shows a simplified synoptic diagram of the most common TH and THM processes based on what is achieved during the process. Several techniques such as wood drying, reconstituted wood processing, and wood shaping have a long industrial tradition, and will not be discussed in this review. Two processes that have been successfully industrialised will be described more in detail: the thermal modification of sawn timber and surface densification.
Fig. 6 - Classification of thermo-hydro (TH) and thermo-hydro-mechanical (THM) processes ([79]).
Thermal modification
Thermally modified timber is wood at which the composition of the cell wall material and its physical properties are modified by exposure to temperatures greater than 160 °C and conditions of decreased oxygen availability. There are various procedures to accomplish this process, most of which differ according to the way they exclude air/oxygen from the system ([55]). For example, a steam or nitrogen atmosphere can be used in the kiln, or the wood can be immersed in hot oil. Thermal modification processes can be applied to a wide range of wood species, but they need to be optimised for each species. The property improvements gained are highly dependent on process conditions, treatment intensity (temperature, duration), wood species, and the dimensions of the sawn timber.
The effect of thermal modification on wood properties has been reported in the literature from the beginning of the 20th century, when it was found that drying wood at a high temperature increased its dimensional stability and reduced its hygroscopicity and strength ([92], [33], [65], [84]). After the First World War, comprehensive investigations were reported on the influence of kiln drying at moderate temperatures on the strength of wood for the aviation industry in the United States ([100]).
Thermally modified timber was introduced by Kollmann ([34]) and Seborg et al. ([82]), but with limited success. Stamm et al. ([85]) reported the first systematic attempts to increase the resistance to wood-destroying fungi by heating wood beneath the surface of molten metal at temperatures between 140 and 320 °C. Thunell & Elken ([90]) and Buro ([10]) continued the work by Stamm and colleagues by studying the thermal modification of wood in different gaseous atmospheres.
Physical changes in wood due to thermal processing
Wood degrades faster when heated by steam or water ([53], [22]). The thermal modification processes are mainly conducted in a dry environment in an inert gas or in a moist environment with steam at temperatures from 160 to 240 °C. Under these conditions, the hemicelluloses are hydrolysed, and the crystallinity index of cellulose increases, but lignin is only slightly affected ([63]). The pyrolysis of hemicelluloses, a process that should be avoided, begins at about 270 °C, followed closely by cellulose ([73]).
The complexity of the process increases as temperature is altered throughout the process. Degrade products form act as catalysts for further reactions, and moisture available for both hydrolysis and catalysts form continuously, moves from the interior to the surfaces of the timber, and evaporates from the material during treatment. Both the physical and chemical environment inside the wood will change throughout the process.
Thermal modification significantly influences the properties of wood, e.g., hygroscopicity and dimensional stability, resistance against fungi and insects, mechanical properties, and properties such as colour, odour, gluability, and coating performance (Tab. 1). Loss of mass of the timber during thermal modification is a typical effect of the process. A decrease in mass up to 20% can occur depending on type of process. Most properties of thermally modified timber are, similar to the properties of the raw material, affected by the intensity of the heat treatment process, i.e., by the temperature and duration of the process.
Tab. 1 - Main changes of properties for thermally modified timber compared with untreated timber.
Desirable property changes | Undesirable property changes |
---|---|
Lower equilibrium moisture content | Decreased MOR (and to some extent) MOE |
Greater dimensional stability | Decreased impact strength |
Greater durability against decay | Increased brittleness (e.g. complicates machining) |
Lower thermal conductivity | Decreased hardness (Brinell hardness) |
Lower density | |
Dark brown colour | |
Characteristic smell | |
Longer pressing time for gluing |
Most thermal modification processes, even at mild temperatures, decrease the hygroscopicity of wood, i.e., its capacity for reabsorption of moisture from the air, however, in some cases, the decreased hygroscopicity can be recovered by moistening ([47]). As a result of the loss of hygroscopic hemicellulose polymers during thermal modification, the equilibrium moisture content is decreased and, consequently, the swelling and shrinking of the wood are drastically decreased. On average, the equilibrium moisture content is decreased to about half the value of the untreated wood. The hygroscopicity of thermally modified timber can vary considerably with varying process parameters. Thermal modification of timber leads to a reduction in strength and the mode of failure, which generally becomes brittle in nature. The mechanical behaviour of thermally modified spruce was investigated by Borrega & Karenlampi ([8]) in relation to mass loss that occurs during thermal modification. At a constant moisture content, the strength, failure strain, and toughness of timber were found to be reduced due to thermal modification. However, the mechanical properties were not only dependent on the mass loss, but also on the relative humidity in the heating atmosphere. As a function of mass loss, the inelastic ductility and inelastic toughness were lowest when the timber were heated in a dry climate rather than in a moist climate. At a constant ambient humidity, failure strain and toughness were still reduced, but the strength and the stiffness had improved up to a mass loss of 2-3%. This improvement was attributed to the lower equilibrium moisture content of the thermally modified timber when placed in service conditions. Huges et al. ([24]) provided a thorough description of the effect of thermal modification on the mechanical properties of timber, especially toughness properties, and the vital role of water and its interaction with the cell wall components.
Commercial thermal modification processes
Thermal modification of sawn timber, which has been investigated for many years, is now commercialised, mainly in Europe. The first commercial thermal modification unit in Europe was based on the research of Burmester ([9]) and started in Germany around 1980. The process was never industrialised on a great scale ([15]). Burmester studied the effects of temperature, pressure, and moisture on wood properties in a closed system, and the process was named Feuchte-Wärme-Druck (FWD).
The Plato process (Proving Lasting Advanced Timber Option) was developed in the 1980s by Royal Dutch Shell in the Netherlands, and is now used by the Plato Company in the Netherlands. The retification process for thermal modification was developed in France in the late 1980s. A second French process is named Le Bois Perdure. This process starts with the drying of green timber in an oven. The wood is then heated to 230 °C in a steam atmosphere (low O2), the steam being generated from the water from the green wood. Sawn timber processed by this method have about the same properties as timber from the retification process.
As the boiling points of many natural oils and resins are greater than the temperature required for the thermal modification of timber, the thermal modification in a hot oil bath is a feasible option. The oil heat treatment (OHT) process was developed in Germany, and the process is performed in a closed process vessel.
The most common commercial thermal modification process, named ThermoWood®, started in Finland (1993). It has been licenced via the International ThermoWood Association, with many operations throughout Europe and a growing number outside Europe. For example, from 2003 to 2016, ThermoWood® global production grew nearly seven fold, from 25 797 m3 in 2003 to 179 507 m3 in 2016 ([27]). In 2003, 32% of the market area was in Finland, with the majority in the rest of Europe (61%). By 2013, Finland was in the small minority (7%), with the rest of Europe being dominant (76%) and a small, but growing, portion outside Europe (17%). The volumes might appear low, but thermal modification technologies align more with value-added niche segments than with commodity products that have minimal processing. During the 12 years of operation from 2001 to 2013, there was an 18% increase in the sales per year ([50]).
The TERMOVUOTO process is a vacuum-based thermal modification technology that has been developed during recent years in an EU-Eco-Innovation initiative project (TV4NEWOOD ECO/12/333079). This thermo-vacuum modification process is an alternative technology for the thermal modification of timber, during which reduction of oxygen inside an air-tight cylinder (the reactor) is obtained by applying a vacuum, while volatiles and water vapour are continuously removed using a vacuum pump. This process exhibits high energy efficiency, lower rate of mass loss, and less corrosion of the process equipment compared to alternative thermal modification technologies ([4]). Moreover, the thermo-vacuum system does not cause a considerable reduction of the mechanical properties of timber ([11]).
Thermal modification processes have also been established in North America. The Perdure process (Le Bois Perdure) was the first process established in Canada, by PCI Industries, in 2003. Today, there are several industrial plants in the Québec region. The ThermoWood process as well as other thermal modification units are also in production in Canada. In 2012, there were seven manufacturers of thermally modified timber in Canada and 10 in the United States ([79]).
Tab. 2 shows the processing conditions for the previously mentioned thermal modification processes.
Tab. 2 - Examples of thermal modification processes and their processing conditions (modified after [79]). (MC): moisture content; (FWD): Feuchte-Wärme-Druck; (OHT): oil heat treatment; (‡): treatment temperature for different stages of the process is separated by “/”.
Process | App. Year |
Trademarks | Initial MC (%) |
Temperature(‡) (°C) |
Process duration (h) | Pressure (MPa) | Atmosphere | Comments |
---|---|---|---|---|---|---|---|---|
FWD | 1970 | - | 10-30 | 120-180 | ≈15 | 0.5-0.6 | Steam | Closed system |
Plato | 1980 | PlatoWood® | 14-18 | 150-180/ 170-190 |
4-5/ 70-120 up to 2 weeks |
Super atmospheric pressure (partly) | Saturated steam/ heated air |
A four- stage process |
ThermoWood | 1990 | ThermoWood® | 10 to green |
130/ 185-215/ 80-90 |
30-70 | Atmospheric | Steam | Continuous steam-flow through the wood under processing that removes volatile degradation products |
Le Bois Perdure | 1990 | Perdure® | green | 200-230 | 12-36 | Atmospheric | Steam | The process involves drying and heating the wood in steam. |
Retification | 1997 | Retiwood®, Bois Rétifié®, Réti®, Retibois®, Retitech®, Retifier® | ≈12 | 160-240 | 8-24 | - | Nitrogen or other gas | The nitrogen atmosphere guarantees a maximum oxygen content of 2% |
OHT | 2000 | OHT® | 10 to green |
180-220 | 24-36 | - | Vegetable oils | Closed system |
TERMOVUOTO (thermo-vacuum treated [TVT] wood) | 2010 | VacWood® | 0% (at the TVT phase) | 160-220 | up to 25 | Vacuum 150-350 (1000) mbar |
Vacuum | Closed system, initial low-temperature drying from initial MC in the TV cylinder |
Although thermally modified timber can now be used in many common applications, the market is still limited. Thermally modified timber is suitable for various uses, mainly in which it is exposed to weather and humidity variations above ground, e.g., for outside use in cladding, terraces, decking, garden furniture, saunas, and windows, but it is also suitable for interior use, such as kitchen furniture, flooring, decorative panels, and stairs. However, its properties and low strength do not allow it to be used in timber structures. Thermally modified timber was first developed to improve the performance and durability of softwoods, but it has more recently been extended to boost the performance of hardwoods, allowing certain low-durability hardwoods to be used outdoors with no additional protection. Examples of thermally modified hardwood species are birch, aspen, ash, soft maple, tulipwood, and red oak (with the best results from quarter-sawn timber).
Surface densification
Densification, i.e., transverse compression to achieve permanent deformation of wood cells and, thereby, increased density of low-density species, has been studied in recent decades. The main goal of densifying sawn timber is to increase its hardness and surface abrasion resistance and, in some cases, also to increase its strength. Densifying timber, as reported by Sears ([81]) or Seborg et al. ([82]), leads to a compression of the wood cells throughout the entire volume of the sawn timber, coining the term “bulk densification”. More recently, several studies have focused on densifying not the entire volume, but only the wood cells close to the surface, i.e. surface densification (Fig. 7).
Fig. 7 - Cross-section views of poplar (Populus deltoides Bartr. ex.) at 35× magnification after surface densification showing cell deformation close to the surface.
In comparison to bulk densification, surface densification offers several advantages. From a structural perspective, surface-densified timber has a higher material usage efficiency. For some products, the improved dampening characteristics result from the unmodified part of the timber, which is deemed as an asset. In addition, treatments to avoid the moisture-induced recovery of the densified wood cells back to their original shape only need to affect the densified cells close beneath the surface, and not the entire piece of timber. This may allow a faster and, thereby, less costly treatment processes ([56]).
To create a high-density wood surface, an adequate volume of wood beneath the surface must be softened ([69]). Due to the low heat conductivity of wood, local moistening improves the heat transfer into the wood; this helps to soften the moistened region of the wood and improve its compressibility, while the rest of the wood continues to resist compressive deformation ([96], [39]). Once the desired volume of wood material beneath the surface has been softened, that volume should be compressed via the application of an external load. The main challenges are to steer the densification path so that only the cells just beneath the surface are compressed, and to lock the cells in a compressed state that resists humidity variation in the surroundings.
The first attempts to densify the surface of sawn timber are found in the work of Tarkow & Seborg ([89]), who developed a technique to produce two types of compression deformations during densification: a small elastic compression of the whole wood element, and a large permanent compressive deformation in a thin layer of the surface of the element. The sawn timber was moved between a pair of heated plates at a linear speed of about 8 m min-1. When the compression set after prolonged periods of high humidification was studied, it showed a distinct compression recovery that was dependent on the pressing conditions, such as temperature, humidity, load level, and pressing time. Although the compression set was stable enough to give the product an industrial application, industrial success did not emerge.
Past studies into surface densification of wood were aimed mainly at exploring different process approaches. Before performing the actual densification in a hot press, Inoue et al. ([25]) cut grooves into the wood surface and filled them with water, and subsequently exposed the surface to microwave radiation to plasticise the surrounding wood cells. Pizzi et al. ([67]) used a friction-welding machine to densify two pieces of wood at the same time, separated by a layer of oil to avoid bonding. A similar approach was adopted by Rautkari et al. ([69]), only using one piece of sawn timber at a time to vibrate on the other, fixed heated steel plate. The vast majority of further studies used a rather simple surface densification process in a hot press.
The reported studies clearly show that it is possible to achieve a significant improvement in several wood properties with surface densification and stabilise the densification effectively, even upon repeated exposure to moisture. However, these approaches rely on time- and energy-consuming batch processes, which means that potential advantages over more expensive wood species or non-renewable materials are lost. For this reason, it is necessary to develop a high-speed surface densification process that is both cost- and energy-efficient.
In an on-going industrial-related project at the Department of Wood Science and Engineering at Luleå University of Technology, a continuous roller pressing approach was adopted to successfully densify the surface of Scots pine boards at a process speed of up to 80 m min-1 ([57]). The surface densification process is a workflow consisting of dedicated stages, such as plasticisation, densification, solidification, and stabilisation (Fig. 8). The process is intended to be integrated in a continuous production flow, from sawn timber to final products such as flooring. Even if the process stages seem separated, the integrated process takes advantage of possible synergetic effects between the process stages. This manufacturing concept has also been tested with success in a conventional continuous MDF panel press ([77]). The press consisted of upper and lower heating devices with four separate adjustable heating sections, two sets of rolling elements to reduce the friction between the stationary heating plates, and movable steel belts. The steel belts transferred heat and pressure to the wood while transporting the wood through the press. The total length of the press was 18 m, with a pressing zone of 6 m.
Fig. 8 - The principal setup of the integrated continuous surface densification manufacturing concept (side view). In addition to the plasticisation and densification stages, the pre- and post-treatment stages can be added for the stabilisation of the densified wood, impregnation, colouring, etc.
Life Cycle Assessment
Though many aspects of wood modification treatments are known, the fundamental influence of the process on product performance, the environment, and end-of-life scenarios remain unknown. To contribute to the low-carbon economy and sustainable development, it is essential to integrate interactive assessments of process parameters, developed product properties, and environmental impacts. To perform objective environmental impact assessments of commercial modification processes and incorporate environmental impact assessments into wood modification processing and product development, including recycling and upgrading at the end of service life, the Life Cycle Assessments (LCA) should be applied.
The common LCA methodology is defined in ISO 14040 ([28]) and ISO 14044 ([29]). Since the 1980s, when LCA analysis was first developed, numerous methodologies to classify, characterise, and normalise environmental effects have been developed. The most common are focused on the following environmental impact indicators: acidification, eutrophication, thinning of the ozone layer, various types of ecotoxicity, air contaminants, resource usage, and green-house gas emissions.
The number of LCA studies in the wood sector is relatively limited, geographically distributed, use a variety of databases, and impact assessment protocols ([37]). Kutnar & Hill ([37]) used a cradle-to-gate analysis to present the carbon footprint of 14 different primary wood products. The largest source of emissions for all sawn timber products stem from the removal of the timber from the forest, while for kiln dried sawn timber, the drying process follows closely behind. Kutnar & Hill ([38]) discussed the merits of wood as a building material in relation to the environmental benefits of using wood products. Carbon footprints, including sequestered carbon, of wood products with different “end-of-life” scenarios and susceptibility to degradation were compared. They concluded that the interactive assessment of processes parameters, developed product properties, and environmental impact, including recycling and disposal options at the end of the service life, towards up-cycling after their service life based on the cradle-to-cradle concept, are essential research needs that must be further investigated.
Werner & Richter ([97]) reviewed the results of international research on the environmental impact of the life cycle of wood products used in the building sector compared to functionally equivalent products from other materials. The study concluded that fossil fuel consumption, potential contributions to the greenhouse effect, and quantities of solid waste tend to be minor for wood products, compared to competing products. Furthermore, impregnated wood products tend to be more critical than comparative products with respect to toxicological effects and/or photo-generated smog, depending on the type of preservative. Bolin & Smith ([6]) compared environmental impacts related to borate-treated sawn timber, and concluded that cradle-to-grave life cycle impacts of borate-treated lumber framing were approximately four times less for fossil fuel use, 1.8 times less for GHGs, 83 times less for water use, 3.5 times less for acidification, 2.5 times less for ecological impact, 2.8 times less for smog formation, and 3.3 times less for eutrophication than those for galvanized steel framing. The results of the cradle-to-grave life cycle assessment showed that alkaline-copper-quaternary (ACQ)-treated timber impacts were 14 times less for fossil fuel use, almost three times less for GHG emissions, potential smog emissions, and water use, four times less for acidification, and almost half for ecological toxicity than those for wood plastic composite (WPC) decking ([7]).
Van Der Lugt & Vogtländer ([94]) performed carbon footprint calculations of acetylated timber with system boundaries “cradle to grave” and compared them with those of steel, concrete, and unsustainably sourced azobe. The functional unit was the bearing structure of a pedestrian bridge, with a size of 16 × 3 meters. The results showed that acetylated wood has a considerably lower carbon footprint than steel, concrete, and unsustainably sourced azobe, and slightly lower than sustainably sourced azobe. Since the calculation also included carbon sequestration, and due to the limited emissions during production and bio-energy production during the end-of-life phase, all sustainably sourced wood alternatives, including acetylated wood, show CO2-negative LCA results over the full life cycle.
Hill & Norton ([21]) discussed the environmental impact of the wood modification process in relation to life extension of the material. By determination of carbon neutrality they identified the point at which the benefits of life extension compensate for the increased environmental impact associated with the modification. The effect of increased maintenance intervals of modified wood products could be a powerful argument in favour of their use.
Manufacturers of modified wood products, to some extent, have considered the environmental impacts related to their products; some companies have also obtained Environmental Products Declarations (EPDs). However, a more detailed consideration reveals that the global environmental impact of timber modification processing and further uses of the modified wood products are not yet included in the development of processes and products ([38]). Moreover, their environmental impacts are, to a considerable extent, still unknown, which must change to meet the demands of increasingly conscientious business and consumer markets desiring to make environmentally responsible decisions regarding the goods and services they decide to patronize.
Conclusion
In this review paper, the development of modified wood according to chemical (acetylation, furfurylation, and impregnation modifications) and thermal-hydro-mechanical processes (thermal modification and surface densification) recently introduced on a European market were discussed. Though many aspects of these modifications are known, the fundamental influence of the process on product performance, the environment, and end-of-life scenarios are still to be included in the research and development of the wood modification technologies. This requires an analysis of the entire value chain, from forest through processing, installation, in-service, end-of-life, second/third life (cascading), and, ultimately, incineration with energy recovery.
Modified wood and the resultant products must place more emphasis on the interactive assessment of process parameters, developed product properties, and environmental impacts. Energy consumption considerably contributes to the environmental impact of modified wood. However, the improved properties during the use phase might reduce the environmental impact of the timber processing. It is important to note that the effective use of wood throughout its whole value chain from forest management, through multiple use cycles and end-of-life disposal, can lead to a truly sustainable development.
Acknowledgments
The authors acknowledge COST Action FP1407. Furthermore, the support of Wood Wisdom-Net+ and the Slovenian Ministry of Education, Science, and Sport of the Republic of Slovenia for their support of the Cascading Recovered Wood projects; European Commission for funding the project InnoRenew CoE (#Grant Agreement 7395 74) under the Horizon2020 Widespread-Teaming program, and infrastructure program IP-0035; the Swedish Research Council for Environment, the Agricultural Sciences and Spatial Planning (FORMAS), project 942-2016-64 and 2014-172 are also acknowledged.
References
Gscholar
Gscholar
Gscholar
Gscholar
Gscholar
Gscholar
Gscholar
Online | Gscholar
Gscholar
Gscholar
Gscholar
Gscholar
Gscholar
Gscholar
Online | Gscholar
Gscholar
Gscholar
Gscholar
Gscholar
Gscholar
Gscholar
Gscholar
Gscholar
Gscholar
Gscholar
Gscholar
Gscholar
Gscholar
Gscholar
Gscholar
Gscholar
CrossRef | Gscholar
Gscholar
Gscholar
Gscholar
Gscholar
Gscholar
Gscholar
Gscholar
Gscholar
Gscholar
Gscholar
Gscholar
Gscholar
Gscholar
Authors’ Info
Authors’ Affiliation
Luleå University of Technology, Wood Science and Engineering, SE-931 87 Skellefteå (Sweden)
University of Primorska, Andrej Marušič Institute, Muzejski trg 2, SI-6000 Koper (Slovenia)
InnoRenew CoE, Livade 6, SI-6310 Izola (Slovenia)
TEI of Thessaly, Research Lab of Wood Science and Technology, Griva 11, GR-43100 Karditsa (Greece)
Corresponding author
Paper Info
Citation
Sandberg D, Kutnar A, Mantanis G (2017). Wood modification technologies - a review. iForest 10: 895-908. - doi: 10.3832/ifor2380-010
Academic Editor
Giacomo Goli
Paper history
Received: Jan 30, 2017
Accepted: Aug 13, 2017
First online: Dec 01, 2017
Publication Date: Dec 31, 2017
Publication Time: 3.67 months
Copyright Information
© SISEF - The Italian Society of Silviculture and Forest Ecology 2017
Open Access
This article is distributed under the terms of the Creative Commons Attribution-Non Commercial 4.0 International (https://creativecommons.org/licenses/by-nc/4.0/), which permits unrestricted use, distribution, and reproduction in any medium, provided you give appropriate credit to the original author(s) and the source, provide a link to the Creative Commons license, and indicate if changes were made.
Web Metrics
Breakdown by View Type
Article Usage
Total Article Views: 92246
(from publication date up to now)
Breakdown by View Type
HTML Page Views: 61847
Abstract Page Views: 8785
PDF Downloads: 20126
Citation/Reference Downloads: 212
XML Downloads: 1276
Web Metrics
Days since publication: 2819
Overall contacts: 92246
Avg. contacts per week: 229.06
Article Citations
Article citations are based on data periodically collected from the Clarivate Web of Science web site
(last update: Mar 2025)
Total number of cites (since 2017): 323
Average cites per year: 35.89
Publication Metrics
by Dimensions ©
Articles citing this article
List of the papers citing this article based on CrossRef Cited-by.
Related Contents
iForest Similar Articles
Technical Notes
Improving impregnation properties of fir wood to acid copper chromate (ACC) with microwave pre-treatment
vol. 8, pp. 89-94 (online: 01 April 2014)
Research Articles
Pre-treatment with sodium silicate, sodium hydroxide, ionic liquids or methacrylate resin to reduce the set-recovery and increase the hardness of surface-densified Scots pine
vol. 10, pp. 857-864 (online: 26 October 2017)
Research Articles
Physical, chemical and mechanical properties of Pinus sylvestris wood at five sites in Portugal
vol. 10, pp. 669-679 (online: 11 July 2017)
Research Articles
Compositions of compounds extracted from thermo-treated wood using solvents of different polarities
vol. 10, pp. 824-828 (online: 25 September 2017)
Research Articles
Testing common hornbeam (Carpinus betulus L.) acetylated with the Accoya method under industrial conditions
vol. 10, pp. 948-954 (online: 19 December 2017)
Research Articles
Hardness and contact angle of thermo-treated poplar plywood for bio-building
vol. 14, pp. 274-277 (online: 29 May 2021)
Research Articles
Physical-mechanical properties and bonding quality of heat treated poplar (I-214 clone) and ceiba plywood
vol. 8, pp. 687-692 (online: 17 December 2014)
Research Articles
Mechanical and physical properties of Cunninghamia lanceolata wood decayed by brown rot
vol. 12, pp. 317-322 (online: 06 June 2019)
Research Articles
Characterization of technological properties of matá-matá wood (Eschweilera coriacea [DC.] S.A. Mori, E. odora Poepp. [Miers] and E. truncata A.C. Sm.) by Near Infrared Spectroscopy
vol. 14, pp. 400-407 (online: 01 September 2021)
Research Articles
Study on the chemical composition of teak wood extracts in different organic solvents
vol. 14, pp. 329-336 (online: 09 July 2021)
iForest Database Search
Search By Author
Search By Keyword
Google Scholar Search
Citing Articles
Search By Author
Search By Keywords
PubMed Search
Search By Author
Search By Keyword