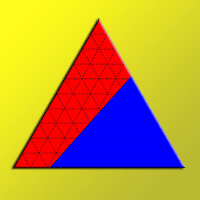
Energy and environmental profile comparison of TMT production from two different companies - a Spanish/Portuguese case study
iForest - Biogeosciences and Forestry, Volume 11, Issue 1, Pages 155-161 (2018)
doi: https://doi.org/10.3832/ifor2339-010
Published: Feb 07, 2018 - Copyright © 2018 SISEF
Research Articles
Collection/Special Issue: COST action FP1407
Understanding wood modification through an integrated scientific and environmental impact approach
Guest Editors: Giacomo Goli, Andreja Kutnar, Dennis Jones, Dick Sandberg
Abstract
Life Cycle Assessment (LCA) is a technique for assessing the environmental aspects and potential impacts associated with a product and has been increasingly used to identify processes or stages in the wood chain with a high environmental impact or to highlight areas where environmental information is unknown. The main aim of this study was to quantify and compare the environmental impacts and the energy used for the production of one cubic meter of Thermally Modified Timber (TMT) by two different companies, one in Spain and the other in Portugal, using the LCA methodology. The LCA study was developed based on ISO 14040/44 standards. The inventory analysis and, subsequently, the impact analysis were performed using the LCA software SimaPro8.1.0.60. The method chosen for the environmental impact assessment was ReCiPe, and for energy use the Cumulative Energy Demand method was chosen. The results show that to produce 1 m3 of thermally modified pine timber the Portuguese company used 14.38 GJ of cumulative energy demand, of which 1.92 GJ was nonrenewable and 12.46 GJ renewable, and the Spanish company used a total of 17.55 GJ, of which 2.52 GJ was nonrenewable and 15.03 GJ renewable. The thermally modified pine timber produced by the Spanish company presented the best environmental results for 13 impact categories in comparison to the 5 best environmental results presented by the Portuguese company. From the weighting triangle, we can conclude that the Portuguese pine boards have a lower environmental impact than Spanish pine boards if a high weight (> 40%) is given to resources, while a weight of <80% is given to human health; otherwise the opposite is true. Regardless of the company, the energy used in the thermal treatment process was identified as the main factor responsible for climate change, acidification, eutrophication, photochemical oxidant formation, metal depletion and fossil depletion. This has to be expected as the treatment is based on heat production and no chemicals are added during the heat treatment process. The round wood production was identified as the leading process responsible for ozone depletion and also presented remarkable contributions to eutrophication and photochemical oxidant formation.
Keywords
Introduction
Wood is a natural renewable material that grows in abundance in Portugal where maritime pine (Pinus pinaster Aiton.) is the forest species with the most planted area, reaching 710 × 103 ha in 2013 and representing 23% of the total forest area ([2]). According to EN-350-2 ([5]), pine heartwood is considered to be in durability class 4 (low durability). However, the wood durability can be increased through the application of wood-preservative systems or by wood modification. Heat treatment is one of the most successful wood modification processes, allowing for wood durability to be improved by three or four times ([19]) to durability class 1 or 2. Heat-treatment has been known for a very long time but it is only in the last decade that several different methods were developed, most of them in Europe ([7], [22]). ThermoWood ([23]) process is a technologically advanced process involving the use of heat and steam. The wood is heated to temperatures from 160 to 230 °C, thus changing its molecular structure, making it more dimensionally stable and resistant to biodegradation, turning it into wood with properties similar to tropical species. The heat-treatment usually varies from medium to high intensity. Thermo D (intense treatment) is conducted at a higher temperature. The resulting products have high dimensional stability and durability, significantly increasing wood life service. This intense treatment ensures wood can be used both indoors and outdoors. It is commonly used for lining walls and cladding (indoors and outdoors), indoor floors and decking. Thermo S (soft treatment) is a medium-temperature treatment that increases the stability of wood, giving it a bright medium brown (honey) tone. The soft treatment is recommended exclusively for indoor use such as floors, linings and other decors. The production process of thermo-modified wood has no chemical compounds at all, thereby avoiding harmful effects to the environment and preserving the natural beauty of wood. An extensive review of the research concerning properties of thermally-treated wood can be found in Esteves & Pereira ([7]), and the relationship between wood modification and the associated environmental impacts in Sandberg & Kutnar ([22]).
In general, for all companies, and particularly for wood companies, the environmental performance of products has become a growing concern, due to the increasing restrictive legislation and more consumer awareness of environmental issues. Life Cycle Assessment is a technique for assessing the environmental aspects and potential impacts associated with a product ([15]), and it has been increasingly used to improve wood production as well as to identify processes or stages in the wood chain with a high environmental impact or highlight areas where environmental information is unknown ([12], [8], [9], [22]).
LCA has already been used to study thermally modified timber products ([24], [10], [19]), as well as forest-based products ([25], [13], [11]). Recently, state of the art LCA was conducted in the forestry sector by Klein et al. ([18]) with a special focus on Global Warming Potential (GWP). However, LCA studies are still lacking for the forest sector. In order to allow better comparability between LCA studies, those authors proposed some methodical approaches regarding the harmonization of system boundaries, functional units, considered processes, and impacts allocation. To identify the environmental impacts related to ThermoVacuum treated timber used for cladding and to compare it against alternative products (untreated cladding and preservative treated cladding), Marra et al. ([19]) concluded that the use of thermally treated timber had the lower ecosystem damage, which is the most important category, and ThermoVacuum cladding damage categories were lower than preservative treated cladding.
According to Sandberg & Kutnar ([22]) and ThermoWood ([24]), thermally treated wood products can contribute to mitigating climate change and promoting sustainable development by reducing energy consumption, pollution and emissions while increasing wood performance. In this study, we aim to quantify and compare the energy use and the environmental impacts of thermally modified maritime pine boards production in a Portuguese and in a Spanish company using the LCA methodology.
Materials and methods
The LCA study of thermally modified maritime pine boards was performed based on ISO-14040 ([15]) and ISO-14044 ([16]) standards.
Goal and scope of the study
The aim of this study was to assess and compare the potential life cycle environmental impacts associated with the production of thermally modified maritime pine boards by a Portuguese and a Spanish company. Company decision makers will be informed of the LCA study (cradle-to-gate) results in order to discover which processes provide better opportunities to improve the environmental impacts of production.
Functional unit
The functional unit was defined as 1 m3 of thermally modified maritime pine boards. The choice of this functional unit is in agreement with other thermally modified product systems also assessed from an LCA perspective ([25], [18], [19]).
System boundary
The system boundary for the product system in this study is represented in a simplified way in Fig. 1. The modules included inside the boundaries are raw material extraction and processing, processing of secondary material input (e.g., recycling processes), transport to the manufacturer, heat production and manufacturing. The Portuguese company uses gas (propane) plus wood residues for heat production and the Spanish company uses only natural gas.
Allocation procedure
The forest process delivers pine round wood as a product and industrial and residual wood as co-products. The sawing and planing process of the product system delivers the product, pine boards, and the following co-products: bark, sawdust and chips that can be used as raw materials for other product systems (i.e., particle board, energy etc.). In order to solve this allocation problem, the environmental burdens are allocated to both product and co-products based on their economic value. This is in agreement with other forest-related LCA studies ([25]). According to these authors, as the economic allocation cannot respect the mass and energy balance of the products, correcting modules are defined in order to add or subtract the CO2 uptake. Inputs that can be clearly attributed to specific products (e.g., gas is used only in thermal treatment) are allocated exclusively to them.
As the allocation approach can have a strong effect on the results, a sensitivity analysis was also proposed considering both volume and economic allocations between the product and co-products in order to identify differences in the environmental profiles.
Inventory analysis
The inventory analysis and subsequent impact analysis were performed using the LCA software SimaPro 8.1.0.60 ([21]) and associated databases and methods.
Data type/data collection
The datasets for the products and processes included in the system boundaries are company data and are presented in Tab. 1 and Tab. 2 for the Portuguese and Spanish case studies, respectively. The thermo-treatment used is Thermo D (intense treatment) to reach a durability level which complies with the requirements for durability class 3.2, according to EN-335-1 ([4]) standard, and for use in construction of exterior decks or cladding. The data is related to 2014 and all the wood comes from forests in the region where the facilities are located. All the materials and energy used for the production of the functional unit were accounted for.
Tab. 1 - Dataset for production of 1 m3 of Portuguese thermally treated maritime pine boards.
Process | Inputs | Value | Outputs | Value |
---|---|---|---|---|
Forest | - | - | Pine round wood | 2.09 m3 |
Sawing and planning | Round wood (maritime pine) | 2.09 m3 | Wood boards | 1.09 m3 |
Electricity | 21.8 KWh | Wood residues (out) | 0.592 m3 | |
Round wood transport | 52 t Km | Wood residues (inside heat production) | 0.408 m3 | |
Thermal treatment | Wood boards | 1.09 m3 | Thermally modified pine boards | 1 m3 |
Electricity | 72.33 KWh | Water | 0.109 m3 (steam) | |
Heat from gas (propane) | 925 MJ (19.97 Kg) | - | - | |
Heat from wood residues | 3454 MJ (0.408 m3) | - | - | |
Water | 0. 109 m3 | - | - |
Tab. 2 - Dataset for production of 1 m3 of Spanish thermally treated maritime pine boards.
Process | Inputs | Value | Outputs | Value |
---|---|---|---|---|
Forest | - | - | Pine round wood | 1.86 m3 |
Sawing and planning | Round wood (maritime pine) | 1.86 m3 | Wood boards | 1.09 m3 |
Electricity | 28.28 KWh | Wood residues (out) | 0.77 m3 | |
Round pine wood transport | 35 t Km | - | - | |
Thermal treatment | Wood boards | 1.09 m3 | Thermally modified pine boards | 1 m3 |
Rope | 0.02 Kg | Water | 0.004 m3 | |
Electricity | 24 KWh | Rope | 0.02 Kg | |
Heat from natural gas | 1465 MJ | - | - | |
Wood boards transport | 22 t Km | - | - | |
Water | 0.004 m3 | - | - |
The Portuguese case study was based on maritime pine boards with length = 0.6-2.6 m, width = 100-120 mm and thickness = 26 mm. The average moisture content and density of wood vary from the moisture content (u>70%) and density (d=1000 kg m-3) of “green wood” to that (u=12% and d=565 Kg m-3) of “dry wood.” The electricity consumed in the production processes is delivered by Energies of Portugal (EDP) as “EDP Comercial Empresas” mix (29% hydro, 10% wind, 4.2% renewable cogeneration, 1.7% other renewable, 0.3% urban solid wastes, 10.7% cogeneration fossil, 4.7% natural gas, 29% coal, 9.6% nuclear and 0.3% fuel oil), which is different from the Portuguese average mix ([6]).
The Spanish case study was based on flat boards of maritime pine with the following dimensions: thickness = 21 mm, width = 90 mm and length = 2400 mm. The total of 220 wood boards have a volume of 1 m3. The average moisture content and density of wood varies from the moisture content (u>70%) and density (d=1250 kg m-3) of “green wood” to that (u=11% and d=590 Kg m-3) of “dry wood”. Regarding power sources used for electricity consumption, the ENDESA mix (26.5% renewables: pure + hybrid, 0.1% high efficiency cogeneration, 10.3% cogeneration, 12.9% natural gas combined cycles, 20% coal, 2.9% fuel/gas, 25.3% nuclear and 2% others) was used because ENDESA provided electricity to the factory, and this electricity mix is different from the Spanish average mix ([1]).
As the thermal treatment includes kiln drying of wet wood (u=70%) down to u= 12%, a shrinkage of 9% (in volume) was considered as in Werner et al. ([25]). Air emissions released from the wood are not accounted for because they were considered to be the same emissions that would occur if the wood was used without treatment.
The following assumptions were made for the datasets:
- The infrastructure of thermo-modified pine board production facilities was not taken into account as it has been assumed that its contribution to the overall impact is negligible ([17]).
- The inventory datasets for the background system (such as electricity) were obtained and adapted as necessary from databases presented in SimaPro 8.1.0.60 software and other sources as presented in Tab. 3. Whenever possible, the Ecoinvent unit process V2.2 was used, otherwise another database was chosen to model the system, as in the processes “heat from Liquefied Petroleum Gas (LPG)” and “natural gas” for which the Franklin USA 98 database was used.
Tab. 3 - Dataset for the background system.
Study | Process | Equivalent process | Source |
---|---|---|---|
Portuguese case study | Round wood | Round wood, softwood, under bark, u=70% at forest road/RER U | Ecoinvent database v. 2.2 (adapted according [8]) |
Electricity | Electricity, low voltage, at grid/EDP 2014 U | Ecoinvent database v. 2.2 (adapted according to electricity source of EDP 2014) | |
Heat from gas (propane) | Heat from LPG FAL | Franklin USA 98 database | |
Heat from wood residues | Wood chips, from industry, softwood, burned in furnace 300KW/CH U | Ecoinvent database v. 2.2 (adapted to the study) | |
Spanish case study | Round wood | Round wood, softwood, under bark, u=70% at forest road/RER U | Ecoinvent database v. 2.2 |
Electricity | Electricity, low voltage, at grid/ENDESA 2014 U | Ecoinvent database v. 2.2 (adapted according to electricity source of ENDESA 2014) | |
Rope | Yarn, jute (GLO), market for Conseq | Ecoinvent 3 | |
Heat from natural gas | Heat from nat. gas FAL | Franklin USA 98 database | |
Common | Transport of round wood or wood boards | Transport, lorry >16 ton, fleet average/RER U | Ecoinvent database v. 2.2 |
Life cycle impact assessment (LCIA)
The method chosen for the environmental impact assessment was ReCiPe Midpoint and Endpoint (H) ver. 1.12 / Europe ReCIPE H/A, and for energy use, the Cumulative Energy Demand ver. 1.09 ([21]) was chosen.
At the midpoint level, 18 impact categories are addressed in ReCiPe: climate change (CC), ozone depletion (OD), terrestrial acidification (TA), freshwater eutrophication (FE), marine eutrophication (ME), human toxicity (HT), photochemical oxidant formation (POF), particulate matter formation (PMF), terrestrial ecotoxicity (TET), freshwater ecotoxicity (FET), marine ecotoxicity (MET), ionizing radiation (IR), agricultural land occupation (ALO), urban land occupation ULO), natural land transformation (NLT), water depletion (WD), metal depletion (MD) and fossil depletion (FD). At the endpoint level, most of these midpoint impact categories are multiplied by damage factors and aggregated into three endpoint categories: (i) Human health; (ii) Ecosystems; and (iii) Resources. The three endpoint categories are normalized and the weighting triangle is graphically built showing the outcome of the comparisons between any two items for all possible weighting sets ([14]).
In the Cumulative Energy Demand method, energy resources are divided into five impact categories: (i) nonrenewable, fossil; (ii) nonrenewable, nuclear; (iii) renewable, biomass; (iv) renewable, wind, solar and geothermal; and (v) renewable, water.
Results and discussion
The results show that to produce 1 m3 of thermally modified pine timber the Portuguese company used 14.38 GJ of cumulative energy demand of which 1.92 GJ was nonrenewable and 12.46 GJ renewable, and the Spanish company used a total of 17.55 GJ of which 2.52 GJ was nonrenewable and 15.03 GJ renewable (Tab. 3).
Tab. 4 shows the contributions to the impact categories considered in the ReCiPe Midpoint method for 1 m3 of thermally modified pine boards production by the Portuguese and Spanish companies, and Fig. 2 shows the comparative environmental profiles. The contributions of Portuguese and Spanish treated boards to climate change, particulate matter formation and agricultural land occupation are almost equal. The Spanish treated boards are better (<50%) than Portuguese for ozone depletion, marine eutrophication, water depletion and metal depletion and much better (>50%) for freshwater eutrophication, toxicity (HT, TE, FE and MET), urban land occupation and natural land transformation. The Portuguese treated boards are better than Spanish for photochemical oxidant formation, ionizing radiation and fossil depletion and much better for terrestrial acidification.
Tab. 4 - Impact assessment results associated with the production of 1 m3 of thermally modified pine boards under different company practices. (CC): climate change; (OD): ozone depletion; (TA): terrestrial acidification; (FE): freshwater eutrophication; (ME): marine eutrophication; (HT): human toxicity; (POF): photochemical oxidant formation; (PMF): particulate matter formation; (TET): terrestrial ecotoxicity; (FET): freshwater ecotoxicity; (MET): marine ecotoxicity; (IR): ionizing radiation; (ALO): agricultural land occupation; (ULO): urban land occupation; (NLT): natural land transformation; (WD): water depletion; (MD): metal depletion; (FD): fossil depletion.
Impact category |
Unit | Portuguese thermally treated boards (1 m3) |
Spanish thermally treated boards (1 m3) |
---|---|---|---|
CC | kg CO2 eq | 1.33E+02 | 1.31E+02 |
OD | kg CFC-11 eq | 5.48E-06 | 4.77E-06 |
TA | kg SO2 eq | 7.92E-01 | 1.71E+00 |
FE | kg P eq | 3.16E-02 | 9.54E-03 |
ME | kg N eq | 4.44E-02 | 3.24E-02 |
HT | kg 1.4-DB eq | 6.64E+01 | 1.24E+01 |
POF | kg NMVOC | 1.21E+00 | 1.39E+00 |
PMF | kg PM10 eq | 4.45E-01 | 4.52E-01 |
TET | kg 1.4-DB eq | 2.86E-02 | 6.89E-03 |
FET | kg 1.4-DB eq | 7.13E-01 | 2.34E-01 |
MET | kg 1.4-DB eq | 7.51E-01 | 2.45E-01 |
IR | kBq U235 eq | 1.63E+01 | 1.94E+01 |
ALO | m2 a | 1.80E+03 | 1.90E+03 |
ULO | m2 a | 4.24E+01 | 1.92E+01 |
NLT | m2 | 9.50E-01 | 1.74E-01 |
WD | m3 | 1.58E+00 | 1.05E+00 |
MD | kg Fe eq | 4.08E+00 | 2.27E+00 |
FD | kg oil eq | 4.08E+01 | 5.43E+01 |
Fig. 2 - Comparative profiles of the thermally modified pine boards by company. (CC): climate change; (OD): ozone depletion; (TA): terrestrial acidification; (FE): freshwater eutrophication; (ME): marine eutrophication; (HT): human toxicity; (POF): photochemical oxidant formation; (PMF): particulate matter formation; (TET): terrestrial ecotoxicity; (FET): freshwater ecotoxicity; (MET): marine ecotoxicity; (IR): ionizing radiation; (ALO): agricultural land occupation; (ULO): urban land occupation; (NLT): natural land transformation; (WD): water depletion; (MD): metal depletion; (FD): fossil depletion.
Related to the processes included in the Portuguese product system boundary, the electricity process is the main one responsible for freshwater eutrophication (70%), freshwater ecotoxicity (58%), marine ecotoxicity (55%), ionizing radiation (76%), water depletion (77%) and metal depletion (57%). Heat production from LPG used in the thermal treatment process is the main process responsible for climate change (48%) and fossil depletion (53%). Wood residues burned in the furnace to produce heat, for that process is the main factor responsible for human toxicity (41%), photochemical oxidant formation (35%) and particulate matter formation (59%). Round wood production at the forest road is the main process responsible for ozone depletion (47%), terrestrial ecotoxicity (58%), land occupation (agricultural 93% and urban 92%) and natural land transformation (92%). The contribution of the transport process to the environmental profile is almost negligible (varies from 0 to 3.5%) for most of the impact categories, except for ozone depletion (13%).
Related to the processes included in the Spanish product system boundaries, the electricity process is the main one responsible for human toxicity (71%), ecotoxicity (freshwater 73% and marine 71%), ionizing radiation (89%), water depletion (70%) and metal depletion (54%). Heat production from natural gas is the main process responsible for climate change (67%), terrestrial acidification (82%), photochemical oxidant formation (51%), particulate matter formation (69%) and fossil depletion (74%). Round wood production at the forest road is the main process responsible for ozone depletion (55%), marine eutrophication (48%), terrestrial ecotoxicity (76%), land occupation (agricultural almost 100% and urban 99%) and natural land transformation (97%). The contribution of the transport process for the environmental profile is small (varies from 0 to 10%) for most indicators, except for ozone depletion (22%) and metal depletion (15%).
Technical wood drying infrastructure, tap water and yarn jute for packaging pine boards were confirmed to contribute less than 1% for all the impact categories.
Although it was not the purpose of this study to prepare an environmental product declaration according to EN-15804 ([3]) for related impact categories considered in the PCR-2012:01V2.01 ([20]) recommendations, the following comments can be addressed.
Terrestrial acidification (TA)
The main source of this indicator is energy production with approximately 84% for Portuguese treated boards (35% is due to heat from wood residues and 33% from electricity) and almost 90% for Spanish treated boards (82% is due to heat from natural gas).
Freshwater eutrophication
Freshwater eutrophication is mainly due to electricity production for Portuguese and Spanish treated boards representing 70% and 80%, respectively. Another important source is fossil fuel burned in harvesting pine round wood representing almost 27% and 14% of this indicator for Portuguese and Spanish boards, respectively.
Global warming (climate change)
Approximately 86% and 81% of this indicator is due to energy production for Portuguese and Spanish treated boards, respectively. Included in that value, heat from gas is responsible for 48% and 67%, respectively.
Photochemical oxidant formation
As for the above indicators, the main source for this indicator is energy production for both Portuguese and Spanish treated boards with 68% and 57%, respectively. However, another 28% and 39% applies to fossil fuel burned in harvesting pine round wood in Portuguese and Spanish treated boards, respectively.
Ozone layer depletion (ODP)
Fossil fuel burned in harvesting pine round wood is still the process that most contributes to this indicator with 47% and 55% for Portuguese and Spanish treated boards, respectively. Electricity and transport are other processes with a significant contribution: 29% and 13% for Portuguese and approximately 22% each for Spanish treated boards, respectively.
Fossil depletion
Heat from gas is the main source for this indicator with 53% for Portuguese treated boards and 74% for Spanish treated boards. Electricity production with 25% and fossil fuel burned in harvesting pine round wood with 12% are other sources that contribute significantly to this indicator for Portuguese treated boards.
In Europe, the characterization factors outlined in EN-15804 (CML-IA method) shall be used. The ReCiPe Midpoint method, used in this study, integrates the “problem oriented approach” of CML-IA that defines the impact categories at a midpoint level. Therefore, the previous comments make sense.
Comparing the results of this study with others in the literature is limited by the restrictions of the data and the use of different methodological approaches in the reports. Nonetheless, some comparisons can be made. Tab. 5 presents a comparison of the results of this study (cradle-to-gate) with those reported in Marra et al. ([19]), where a cradle-to-grave life cycle assessment was performed using the same impact assessment method (ReCiPe Endpoint/Europe H/A/Normalization) to identify the environmental impacts related to ThermoVacuum treated timber used for cladding. As the versions (1.12 and 1.13) of the method used and the life cycle stages were different, we can only conclude that for all functional units, Ecosystems is the most important damage category followed by Resources and Human Health. The highest damage category values for ThermoVacuum treated timber are partially explained by the additional life cycle stages (“use” and “end-of-life”) considered in that study.
Tab. 5 - Comparison of Portuguese and Spanish thermally threated boards with Thermo-Vacuum cladding. (‡) Source: Marra et al. ([19]); (EU eq): European equivalents.
Impact category | Unit | Portuguese thermally treated boards (1 m3) |
Spanish thermally treated boards (1 m3) |
Thermo-Vacuum cladding (‡) (1 m3) |
---|---|---|---|---|
Human Health | EU eq. | 0.0172 | 0.0154 | 0.035 |
Ecosystems | EU eq. | 0.1403 | 0.1362 | 0.26 |
Resources | EU eq. | 0.0228 | 0.0296 | 0.06 |
The weighting triangle
For the impact assessment method ReCiPe Endpoint that uses three damage categories, as described above, SimaPro has an option to automatically generate a triangle during the normalization step. The triangle graphically shows the outcome of the comparison between any two items for all possible weighting sets. Each point within the triangle represents a combination of weights that add up to 100%.
The line of indifference in the weighting triangle and the sub areas with their specific ranking orders is presented in Fig. 3. The line represents weighting factors for which Portuguese and Spanish treated pine boards have the same environmental loads. From the weighting triangle we can conclude that the Portuguese boards have a lower environmental impact than Spanish boards if a high weight (>40%) is given to Resources, while a weight of <80% is given to Human Health. Otherwise the opposite is true.
Fig. 3 - Weighting triangle showing the line of indifference and sub-areas with their specific ranking orders.
Sensitivity analysis
As reported before, the allocation approach can have a strong effect on the results. In order to identify differences in the environmental profiles, a sensitivity analysis was done to determine the effects of different assumptions on LCA results, based on using volume or economic allocations between the product and co-products. Factor allocations for the products and co-products studied are presented in Tab. 6. If we consider mass allocation instead economic allocation, the environmental profiles of Portuguese and Spanish thermally treated boards are better. For Portuguese treated boards, the indicators reduce to between 2% for human toxicity to 20% for land occupation and transformation. For Spanish treated boards the indicators reduce to between 4% for terrestrial acidification to 29% for land occupation and transformation. In this case, Spanish treated boards are now better than Portuguese for 14 (instead of 12) impact categories of the 18 considered in this method. PMF changed from -2% to +1% and ALO changed from -5% to +6% related to economic allocation.
Tab. 6 - Allocation procedure.
Allocation Factors | Portuguese thermally treated boards (1 m3) |
Spanish thermally treated boards (1 m3) |
||
---|---|---|---|---|
Economic allocation |
Mass allocation |
Economic allocation |
Mass allocation |
|
Wood boards | 0.64 | 0.5 | 0.79 | 0.56 |
Wood residues | 0.36 | 0.5 | 0.21 | 0.44 |
Considering the use of electricity from the Portuguese grid (instead of EDP) and from the Spanish grid (instead of ENDESA) the results show that Spanish treated boards are now better than Portuguese for 13 (instead of 12) impact categories. PMF changed from -2% to +1% related economic allocation.
Conclusion
Our results showed that 1 m3 of Spanish thermally treated pine boards are more energy intensive (17.55 GJ m-3) than Portuguese (14.38 GJ m-3). Spanish treated boards present the best environmental results for 12 impact categories, while Portuguese only presented the best environmental results in 6 impact categories.
For both product system boundaries, the electricity process is the main process responsible for ecotoxicity (freshwater and marine), ionizing radiation and depletion (water and metal) and for freshwater eutrophication. Heat production from gas used in thermal treatment process is the main factor responsible for climate change and fossil depletion. This process is also the main one responsible for terrestrial acidification (82%), photochemical oxidant formation (51%) and particulate matter formation (69%) for the Spanish functional unit. Fossil fuel burned in harvesting round wood is the main factor responsible for ozone depletion, terrestrial ecotoxicity, land occupation (agricultural and urban) and natural land transformation. Moreover, this process is the main one responsible for marine eutrophication (48%) for the Spanish functional unit. The contribution of transport processes to the environmental profiles is almost negligible for the Portuguese product (varies from 0 to 3.5%) for most impact categories except for ozone depletion (13%) and is non-significant for the Spanish product (varies from 0 to 10%) for most indicators, except for ozone depletion (22%) and metal depletion (15%). Wood residues burned in the furnace to produce heat for Portuguese treated boards is the main factor responsible for human toxicity (41%), photochemical oxidant formation (35%) and particulate matter formation (59%).
The environmental indicators for both Portuguese and Spanish treated boards are better if mass allocation is used instead of economic allocation.
Acknowledgments
This work is financed by national funds through FCT - Fundação para a Ciência e Tecnologia, I.P., under the project UID/ Multi/04016/2016. We would like to thank the COST Action FP1407, the Instituto Politécnico de Viseu and CI&DETS for their support.
References
Gscholar
Gscholar
Gscholar
Gscholar
Gscholar
Gscholar
Online | Gscholar
Gscholar
Gscholar
Gscholar
Gscholar
Online | Gscholar
Gscholar
Gscholar
Authors’ Info
Authors’ Affiliation
Bruno Esteves
Idalina Domingos
Centre for the Study of Education, Technologies and Health, Campus Politécnico, 3504-510 Viseu (Portugal)
Jalel Labidi
Chemical and Environmental Engineering Department, University of the Basque Country, 20018 San Sebastian (Spain)
Corresponding author
Paper Info
Citation
Ferreira J, Herrera R, Labidi J, Esteves B, Domingos I (2018). Energy and environmental profile comparison of TMT production from two different companies - a Spanish/Portuguese case study. iForest 11: 155-161. - doi: 10.3832/ifor2339-010
Academic Editor
Giacomo Goli
Paper history
Received: Dec 30, 2016
Accepted: Nov 21, 2017
First online: Feb 07, 2018
Publication Date: Feb 28, 2018
Publication Time: 2.60 months
Copyright Information
© SISEF - The Italian Society of Silviculture and Forest Ecology 2018
Open Access
This article is distributed under the terms of the Creative Commons Attribution-Non Commercial 4.0 International (https://creativecommons.org/licenses/by-nc/4.0/), which permits unrestricted use, distribution, and reproduction in any medium, provided you give appropriate credit to the original author(s) and the source, provide a link to the Creative Commons license, and indicate if changes were made.
Web Metrics
Breakdown by View Type
Article Usage
Total Article Views: 38258
(from publication date up to now)
Breakdown by View Type
HTML Page Views: 32016
Abstract Page Views: 1936
PDF Downloads: 3585
Citation/Reference Downloads: 15
XML Downloads: 706
Web Metrics
Days since publication: 2271
Overall contacts: 38258
Avg. contacts per week: 117.92
Article Citations
Article citations are based on data periodically collected from the Clarivate Web of Science web site
(last update: Feb 2023)
Total number of cites (since 2018): 6
Average cites per year: 1.00
Publication Metrics
by Dimensions ©
Articles citing this article
List of the papers citing this article based on CrossRef Cited-by.
Related Contents
iForest Similar Articles
Research Articles
Changes in moisture exclusion efficiency and crystallinity of thermally modified wood with aging
vol. 12, pp. 92-97 (online: 24 January 2019)
Research Articles
Life cycle assessment of tannin extraction from spruce bark
vol. 10, pp. 807-814 (online: 25 September 2017)
Research Articles
Dielectric properties of paraffin wax emulsion/copper azole compound system treated wood
vol. 12, pp. 199-206 (online: 10 April 2019)
Research Articles
Fuel consumption comparison of two forwarders in lowland forests of pedunculate oak
vol. 12, pp. 125-131 (online: 11 February 2019)
Research Articles
Comparison of alternative harvesting systems for selective thinning in a Mediterranean pine afforestation (Pinus halepensis Mill.) for bioenergy use
vol. 14, pp. 465-472 (online: 16 October 2021)
Research Articles
Comparison of timber-house technologies and initiatives supporting use of timber in Slovenia and in Sweden - the state of the art
vol. 10, pp. 930-938 (online: 07 December 2017)
Research Articles
Examining the evolution and convergence of wood modification and environmental impact assessment in research
vol. 10, pp. 879-885 (online: 06 November 2017)
Research Articles
Identification of wood from the Amazon by characteristics of Haralick and Neural Network: image segmentation and polishing of the surface
vol. 15, pp. 234-239 (online: 14 July 2022)
Research Articles
Modifying harvesting time as a tool to reduce nutrient export by timber extraction: a case study in planted teak (Tectona grandis L.f.) forests in Costa Rica
vol. 9, pp. 729-735 (online: 03 June 2016)
Research Articles
Hardness and contact angle of thermo-treated poplar plywood for bio-building
vol. 14, pp. 274-277 (online: 29 May 2021)
iForest Database Search
Search By Author
Search By Keyword
Google Scholar Search
Citing Articles
Search By Author
Search By Keywords
PubMed Search
Search By Author
Search By Keyword